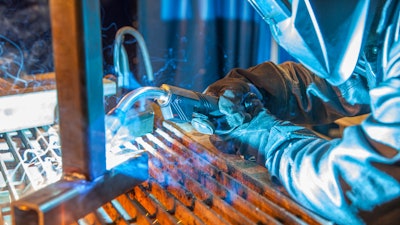
Optimizing MIG gun performance starts with the basics: proper storage and handling, scheduling planned downtime for preventive maintenance and regular inspection for issues or wear. Proper maintenance is especially key to getting the best results. It can extend consumable and MIG welding gun life, as well as help prevent problems like bird-nesting or burnback that can cost time and money for troubleshooting and rework.
Consider these five tips and best practices to get the best performance from your MIG gun and consumables.
Tip 1: Inspect and tighten all connections
Before you start welding, check all connections to make sure they’re tight. Start with the front of the gun and work your way back to the feeder. It’s also a good idea to inspect all consumables and equipment to make sure they’re in good condition with no damage.On the welding gun, a tight neck connection is essential to carry the electrical current from the welding cable to the front-end consumables. Loose connections at either end of the neck can cause poor electrical conductivity. This can result in weld defects and, potentially, MIG gun overheating. Also, visually inspect the gun handle and trigger for missing screws or damage.
A rotatable neck on a welding gun can be rotated to the desired position for welding, which increases operator comfort and flexibility. But if you’re using a rotatable neck, be sure the hand nut on the neck is tight and the neck is secure in the cable fitting.
Ensure that all connections are tight before welding. Start with the front of the gun and work back to the feeder. This inspection can help prevent electrical resistance that could lead to premature consumable failure and gun overheating.Bernard
Tip 2: Check for cable issues
Inspect the welding cable for any cuts, kinks or damage to the outer cover. Cuts in the cable can expose the internal copper wiring, posing a potential safety hazard. This type of damage can also cause cable failure due to electrical resistance that causes heat buildup.
Also, be sure the cable’s power pin is fully inserted and tightly connected at the feeder. A loose feeder connection can cause electrical resistance at the joint — and eventually an overheated gun — in addition to the potential for wire bird-nesting at the feeder.
Tip 3: Take care with the liner
One key step for producing quality welds is installing a clean MIG gun liner that is the correct size. Improperly installed or trimmed liners are a common source of weld quality issues and time spent troubleshooting — and liners can be the most difficult part of the gun to inspect and maintain.
Liners that are trimmed too short are a frequent cause of wire feeding problems. For the best results, follow the manufacturer’s instructions for proper liner trimming and wire installation or look for a consumables system that offers error-proof installation, such as AccuLock S consumables.
It’s also important to keep the liner off the floor during installation. Otherwise, it can pick up dirt and debris that can then be passed into the weld pool where it may cause defects. A dirty liner can also hinder shielding gas flow, which can cause porosity. In addition, fragments of welding wire can chip off and build up in the liner, which over time can result in burnback, bird-nesting and poor wire feeding.
To avoid these time-consuming problems related to dirt and debris, maintain the liner by periodically blowing clean compressed air through it. This will clear any buildup or blockages. Take the extra minutes needed to complete this task during wire changeovers or when you’re removing wire from the gun.
Tip 4: Spend time on front-end consumables
The front-end consumables on a MIG gun, which include the gas diffuser, nozzle and contact tip, are exposed to heat and spatter. As a result, these consumables typically require frequent replacement — though regular inspection and maintenance can help extend their life as well as improve gun performance and weld quality. Follow these maintenance steps for front-end consumables.- Gas diffuser: The diffuser connects to the gun neck and carries the electrical current to the contact tip. It also provides gas flow to the weld pool. Check the diffuser to ensure that all connections are tight, and inspect the diffuser’s O-rings for cuts, cracks or other damage. Replace as necessary.
- Nozzle: This consumable focuses the shielding gas around the weld pool. Spatter can easily build up inside the nozzle, obstructing gas flow and resulting in inadequate shielding gas coverage, which causes weld problems. Watch for spatter buildup in the nozzle and use welper pliers to remove it.
- Contact tip: This is the last point of contact between the welding wire and the welding gun. A common problem with contact tips is keyholing, which occurs when the welding wire wears an oblong-shaped slot into the tip’s bore as it passes through. This can put the wire out of center and result in problems like erratic arc. When troubleshooting wire feeding issues, a good first step is to change the contact tip or switch to a larger tip size. Also, be sure to replace tips when they look worn.
Tip 5: Ensure proper storage
Last, proper storage of MIG gun consumables helps extend MIG gun and consumable life and produce the best results. Store your MIG gun in a coiled position when it’s not in use. Good options are hanging the gun or laying it flat, such as on a shelf. Don’t leave MIG guns on the floor where the cables can be stepped on or run over and damaged.Preventive maintenance for better results
The bottom line is this: The better care you take of your MIG welding gun and consumables, the better results you can achieve. Time spent on preventive maintenance will pay off later in less time spent on troubleshooting and rework. Planning for this upkeep is a crucial part of keeping production flowing smoothly and avoiding costly unplanned downtime.
---
Mark Teach has worked with ITW Welding Group since 2000, holding various positions. He has been responsible for specialty products for the Bernard and Tregaskiss MIG gun division; assisted sales teams with installation, troubleshooting and training on the robotic and handheld MIG gun process; and currently serves as MIG gun sales specialist for the Great Lakes region.