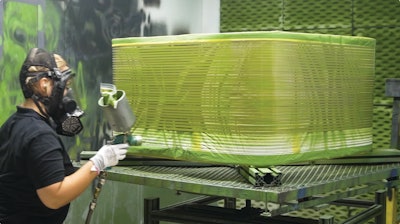
Stainless steel is regarded as one of the most suitable materials for the manufacture of medical devices and many other types of products. When compared to the potential alternatives, stainless steel provides superior hygienic properties, precision control and customization options, among other benefits.
This was recently demonstrated when a producer of health and personal care products needed to make changes to their printing process.
The customer was dissatisfied with the inaccurate and inconsistent results they were seeing with their embossing and silicone printing, so they turned to Belt Technologies for a steadier, more reliable and cost-effective solution.
The team at Belt resolved the problem by creating a customized printing process with increased precision and adhesion, allowing the customer to open production in new markets.
The Process and the Problem
The client is a global technology company with a broad portfolio of systems, products, services and applications in the markets of energy, paper, raw materials and automotive. In this specific instance, the application was a printing process to create complicated patterns on toiletry products like toilet paper or adult diapers.
The method consisted of pushing silicone through a grown nickel screen using a scraper blade, and also included a traditional embossing process that used a complex, loom-woven belt constructed from polyethylene terephthalate (PET) fibers.
Unfortunately, the screens had thin walls with sharp burrs around the perforation pattern, which both affected the silicone print medium and negatively impacted the final product’s print quality and adhesion.
The screens would only last a couple months, which resulted in costly turnover and a weaker end product. The customer sought a new solution that incorporated a more robust material and offered cost-saving benefits.
The Improvement
After discussing the issue with the client, Belt Technologies created an entirely new conveyor which consisted of custom cylinder belts and pulleys. The solution provided the customer with a perfect fit to solve the issues of bonding and print clarity.
“We have a wide range of stock products, but creating custom solutions is really where we shine,” said Brian Harbison, managing director of Belt Technologies. “For this project, we knew our PureSteel material would make the process more precise and the pattern clearer. We were able to double the thickness and create more height, which allowed for the intricate patterns to be created by thousands of perforated holes.”
Beyond the bonding and print clarity, the Belt team was able to add a Teflon coating to help ensure the silicone would not stick to the cylinder.
“Turning a flat piece of metal into a perfect disk is a difficult task,” continued Harbison. “We tried numerous flat welds before we found the right formula to create the current products, and it works extremely well.”
The Results
The partnership with Belt Technologies provided the customer with increased thickness, more accurate hole patterns and an anti-stick coating, while also making the process more cost effective. The Belt team’s work succeeded in eliminating the customer’s need to emboss products, allowing them to rely solely on the new silicone solution.
The Secret Behind the Success of Stainless Steel
There are several reasons why the client experienced optimal results with stainless steel, including the intrinsic benefits of hygiene, precision and customization.
When it comes to hygiene, conveyor belts can create problems in two different ways: pieces may come off the belt itself and contaminate the product, or insufficient cleaning methods might leave bacteria on the surface.
In fact, polymer, plastic and metal mesh conveyors could potentially increase the risk of product contamination during production. This is because belts made from polymeric materials often incorporate fibers for added strength which can become detached when the belt rubs against guides or rough edges. These particulates can then make their way into the product, leading to potential contamination.
In contrast, stainless steel has a smooth impermeable surface that offers no hiding places for bacteria or other microbes. The complete lack of gaps, recesses and crevices also makes stainless steel much easier to clean than traditional materials.
Because endless metal belts are resistant to high temperatures and corrosion, the conveyor systems can easily be cleaned with chlorine, high-pressure steam or most other washing methods. In addition, our PureSteel products do not require dust-generating lubricant that could introduce foreign substances into cleanroom environments or damage intricate machinery.
When it comes to precision and durability, metal belts offer unique designs that guarantee zero slip and absolute accuracy. Stainless steel drive tapes substantially reduce chordal vibration, motion loss and backlash that can often result in inaccurate positioning.
Belt Technologies’ timing belts can be fabricated with a pitch accuracy of ±0.0005 inches, which is understandably valuable in designing, indexing, positioning or processing equipment.
As for durability, stainless steel has a tensile strength ranging from of 180 to 300 KPSI (thousand pound-force per square inch), depending on the alloy and temper of the metal. That means relatively thin and lightweight belts can be designed to handle the stresses of almost any application.
Belt Technologies’ stainless steel products are made with a wide variety of specific alloys, width and thickness combinations, perforation patterns, coatings and attachments to best fit exacting requirements and specifications.
The perforations in our belt’s pitch profiles are created by mechanical and laser cutting, die-and-cut presses and rotary-pinned perforation rollers. While custom pitch profiles vary by manufacturer, our team can create perforations in stainless steel belts as thin as 0.002 inches, as narrow as 0.040 inches and as wide as 36 inches.