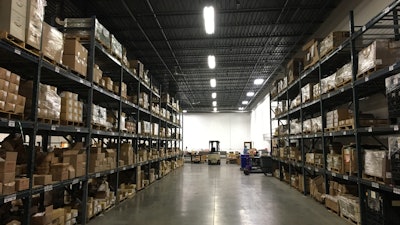
2020 taught supply chain companies that to compete in today’s fast-changing, on-demand world, you need to be nimble. It’s more important than ever before to get products out the door faster, more accurately and with fewer employee resources.
But while 80 of IT and operations decision-makers in the manufacturing, logistics, retail and distribution industries believe that modern technology is key to competing in the on-demand economy[i], only 35 percent of them say they have a clear understanding of where to start deploying that technology[ii].
The challenge is incredibly daunting for small- and medium-sized supply chain businesses, some of which continue to rely on manual processes to support their warehouse operations. But the good news is that technological advances have made it easier for these companies to introduce modern warehouse technology into their supply chain operations. Innovative technology solutions are now easier to deploy, more intuitive to use and deliver a faster return on investment (ROI).
Not surprisingly, the first step in realizing a solid ROI on your investments involves identifying areas where technology can help you quickly streamline operations. Start by looking at daily tasks performed by your employees. Although this may seem obvious, companies often fail to step back and truly study their day-to-day operations. When they do, they often quickly uncover new ways to streamline workflows and increase productivity.
Boosting Front-line Worker Productivity
Suppose your employees spend hours a day using basic barcode scanners that perform poorly and result in costly productivity losses. By simply introducing more intelligent scanners that can accurately read damaged, torn or poorly printed barcodes from any angle, you eliminate the need for multiple scans saving time and money.
Or maybe your employees need scanners that are more rugged and can accurately scan barcodes that are close or far away or scan multiple barcodes with a single trigger pull. Such solutions enable forklift drivers, for example, to quickly complete multiple inventory scans without getting off the vehicle - saving hours of lost productivity every day.
Investing in wearable scanners that speed the scanning process can result in significant labor savings as well. Setting up mobile thermal printers near inbound and outbound operations can also boost efficiency by eliminating the need for workers to walk back and forth to centralized printers to retrieve shipping labels. And newer thermal printer models are much easier to operate and reload, saving time on employee training and operation.
Increasing Team Productivity and Safety
After looking at individual processes, consider ways to streamline operations across teams. For instance, mobile devices that support group communications enable faster collaboration between workers – and help keep employees safer by allowing a virtual, daily “group huddle.”
Mobile devices including wearable technology, such as smart glasses, that are integrated with the warehouse management system (WMS) are essential for streamlining operations across teams. For instance, employees equipped with head-mounted displays can view easy-to-follow picking instructions at eye level, enabling them to pick multiple orders simultaneously. Managers can dynamically assign order fulfillment instructions based on a picker’s current location, availability or even order urgency.
Small upgrades that improve operations for multiple workers can also deliver significant productivity improvements with minimal investment. For instance, rugged tablets mounted on lift trucks or pick carts can facilitate faster, more efficient materials transport.
Similarly, technology can help keep workers safe during the pandemic by issuing alerts when employees get closer than six feet from each other – and create a record when employees are in close contact for a specified period of time. These data records allow easy contact tracing if an employee tests positive for COVID-19, and they can also be used to uncover congested workflow areas so warehouses can take steps to reduce the likelihood of exposure. To illustrate, in high-volume picking areas, a warehouse operator might restructure the picking process to reduce congestion or consider transferring materials via conveyers or collaborative robots to reduce person-to-person contact.
Improving Asset Visibility
After improving employee and overall workforce productivity, the next logical step involves gaining greater asset visibility. Technology such as radio frequency identification (RFID) registers tagged inventory via an RFID reader as soon as it is taken off the truck and wheeled through the dock doors. RFID readers located throughout the warehouse give visibility to precisely what’s in stock and where it is stored.
This is particularly important for warehouses that support retail operations, given that U.S. retailers alone lose nearly $145 billion annually due to out-of-stock inventory, according to IHL Group.[iii] Having more visibility into each piece of inventory can significantly reduce out-of-stocks and the associated lost revenue.
The reality is that 77 percent of respondents agree that they need to modernize their warehouse operations but admit they are slow to implement new technology.[iv] But in today’s on-demand world, being slow to implement new technology could put you in danger of losing business to more agile competitors.
Fortunately, getting started is easier than many businesses think. Companies can begin modernizing their warehouses simply by taking a good, hard look at their daily operations to determine where efficiencies can be gained.
And companies do not have to complete this analysis alone. When choosing a technology partner, select the one that will conduct an in-depth assessment of your operations before you buy.
A good operational assessment uncovers areas where technology can help you streamline operations with insights into how fast a return on that technology investment will be realized. With this information, you can implement new technology with confidence that it will produce a solid return for your business.
To learn more about how technology is helping warehouse operators modernize their operations and future-ready their supply chains, click here.
Wheeler
Mark Wheeler is the Director of Supply Chain Solutions at Zebra Technologies, where he is responsible for Zebra’s warehouse and supply chain solutions global strategy. He collaborates closely with customers’ supply chain operations teams, solution partners, and Zebra’s product development teams to align emerging technology solutions with customer needs. Mr. Wheeler has held numerous positions in supply chain execution throughout his 30-year career, including strategic consulting, automated warehouse design and build and complex systems integration. He holds a Bachelor of Science (BS) in mechanical engineering from Carnegie-Mellon University.
[i] Zebra Technologies, Warehousing Vision Study, 2019, page 2. https://www.zebra.com/content/dam/zebra_new_ia/en-us/solutions-verticals/vertical-solutions/warehouse-management/vision-study/2024/warehouse-vision-study-en-us.pdf
[ii] Zebra Technologies, Warehousing Vision Study, 2019, page 3. https://www.zebra.com/content/dam/zebra_new_ia/en-us/solutions-verticals/vertical-solutions/warehouse-management/vision-study/2024/warehouse-vision-study-en-us.pdf
[iii] IHL Group, Out of Stocks, Out of Luck, 2018, page 7. https://www.radial.com/sites/default/files/out-of-stock-solutions.pdf
[iv] Zebra Technologies, Warehousing Vision Study, 2019, page 6 https://www.zebra.com/content/dam/zebra_new_ia/en-us/solutions-verticals/vertical-solutions/warehouse-management/vision-study/2024/warehouse-vision-study-en-us.pdf