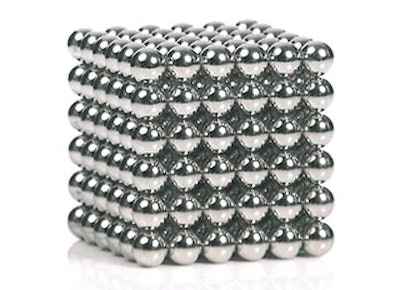
On May 12, 2014, the U.S. Consumer Product Safety Commission (CPSC) settled its long-running proceeding against the manufacturer of Buckyballs. The matter, which saw the CPSC pursue novel and arguably questionable enforcement tactics, provides lessons for all manufacturers.
Buckyballs are small rare earth magnets that were sold as an adult desk toy with express warnings that they should be kept away from children. Despite this, the CPSC received reports that some children had ingested Buckyballs and similar products. Such magnets, if ingested, can cause gastro-intestinal injury and removal sometimes required surgery.
The CPSC initially worked with Buckyballs to conduct an educational campaign about the hazards, but ultimately asked retailers to stop selling them (even though they were not illegal) and filed an administrative proceeding seeking a recall. Soon after, the company that manufactured Buckyballs went out of business. When that happened, the CPSC amended its complaint to add its CEO, seeking to force him personally to conduct a recall under what’s known as the “responsible corporate officer” doctrine. Under the CPSC’s interpretation of that doctrine, any corporate officer responsible for product safety decisions would be personally responsible to conduct a recall, even without piercing the corporate veil.
Lessons for Manufacturers
Though some aspects of this case are unique, there are several lessons for manufacturers in the CPSC’s approach to its enforcement action against Buckyballs.
1. Product Risk Assessment
Every manufacturer introducing a new product must conduct a risk assessment, particularly if 1) the product is truly innovative and first in the market, and 2) if the product is outside of a manufacturer’s particular area of expertise. In both situations, a manufacturer has less knowledge and understanding about the risks of a product, as well as the potential consumer use and abuses. Without that knowledge and understanding, there is the real potential for an unintended and unexpected hazard to surface when the product reaches the market and for serious product liability exposure for the manufacturer.
2. Insurance Coverage for Responsible Corporate Officer Claims
As the CPSC takes a more aggressive attitude, companies should give new consideration to whether recall insurance is now warranted. If a company already has recall insurance, it is worth reviewing the policy terms to see if they are still adequate, or if better terms are available in the marketplace.
In addition, manufacturers should ensure their policies will protect them if the CPSC continues to assert the responsible corporate officer doctrine, as it did with Buckyballs. Although the doctrine is not limited to officers of defunct companies, it is particularly problematic for officers of companies without the financial wherewithal to defend them. Standard director’s and officer’s insurance policies do not appear to apply to such claims, but small companies with risky products may want to seek out a product that would provide the necessary coverage. Every company should review officer indemnity provisions in its policies and employment agreements to make sure they cover claims under the responsible corporate officer doctrine.
3. Planning for CPSC Enforcement and Recalls
CPSC issues are often business emergencies and it is best to have an internal and external team in place that can analyze and respond to issues as they arise. This is best done in advance and is time well spent. Similarly, planning for a recall in advance will ensure that if one occurs it will proceed smoothly and effectively.
Manufacturers must also have a crisis management plan. Like the team managing CPSC issues, it is too late to assemble a crisis management team after the crisis begins. Companies should make sure that they have identified appropriate public relations, legal and other crisis management expertise prior to needing it. Crisis management is most effective when the team understands the client’s business and challenges beforehand. Crises move quickly and time spent creating and educating a crisis management team in advance will help considerably.
4. Build a Relationship with the CPSC
It is also important to have a relationship with the CPSC. The manufacturer of Buckyballs had an ongoing dialogue with the agency. That the dialogue did not ultimately prevent litigation should not lead to the impression that there is no reason to have one. In fact, the vast majority of CPSC issues are resolved short of litigation, and the most successful companies cultivate a relationship on several levels.
Manufacturers should take the opportunity to meet with the CPSC commissioners and key staff just as an introduction. It always helps to have some name recognition in advance of an issue. If an issue does arise, companies should not hesitate to have an in-person meeting with the CPSC. While much of the exchange with any regulator is necessarily in writing, it is often a good idea to exchange ideas face-to-face.
Moreover, manufacturers should cultivate relationships with the CPSC through trade associations. The most effective trade associations have continuing interactions with the CPSC and regularly seek input from members on policy directions.
Conclusion
If there is one main takeaway for manufacturers from Buckyballs it is the importance of planning and preparation in mitigating risks from CPSC enforcement actions. Manufacturers should do as much research as possible in advance of launching a new product, have a plan for recalls and crisis management, and build a relationship with the CPSC. Following these steps will go a long way to introducing successful products into the marketplace.
Disclaimer: This is for general information and is not intended to be and should not be taken as legal advice for any particular matter. It is not intended to and does not create any attorney-client relationship. The opinions expressed and any legal positions asserted in the article are those of the authors and do not necessarily reflect the opinions or positions of Miles & Stockbridge P.C., its other lawyers, or Manufacturing Business Technology.
Timothy L. Mullin, Jr. is principal withMiles & Stockbridge’s Products Liability and Mass Torts Practice Group and a member of its Manufacturing and Distribution Industry Team.He represents manufacturers in product liability cases and in client matters related to the CPSC, including corrective action plans (recalls), civil penalties and reports and investigations under the Consumer Product Safety Act. He also provides risk management counseling to manufacturers. Mullin was co-counsel for the Buckyballs manufacturer’s officer named in the CPSC administrative proceeding.
To read more manufacturing and technology news, sign up for our newsletter. You can also follow Manufacturing Business Technology on Twitter @MBTwebsite.