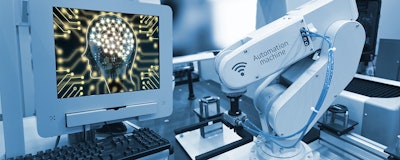
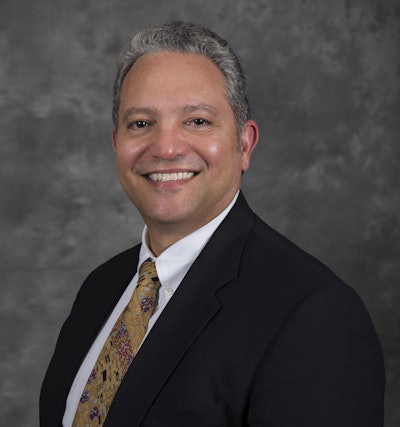
The term Digital Manufacturing represents a virtual mountain of change for all kinds of industries, from electronics to aircraft carriers. As we head into a new year, it’s time to step back and take a fresh look at how we’ll make progress up the mountain in the near, mid, and long term. While the promised land of end-to-end digital integration of machines, processes, systems, and people may be years from realization, the preparatory steps required will easily fill that time. Joining this trek at a later date will leave you struggling through the wilderness while your competitors enjoy the view from the top. This is especially true for complex discrete manufacturers — those producing aircraft, ships, energy infrastructure, medical devices, and the like. As global demand and competition intensify, enterprises in these industries — and their entire value chains — are under pressure to streamline and connect everything from design to production to maintenance of the product.
Operational Excellence
There are scores of immediate opportunities to push forward and make progress on operational excellence, supply chain visibility, change control, and quality management. Investments in digital platforms, smart machines, IIoT, and analytics are moving along. Leading-edge enterprises and industries (Aerospace & Defense, for example) are far enough along to strengthen their initiatives by incorporating lessons learned in recent years — and to set an example for those organizations in less mature stages. Some leaders are sharing their experiences directly with partners and indirectly through industry and trade conferences hoping to raise the bar for their entire supply chain.
When it comes to modernization initiatives, much is made of the hype cycle. We recommend not getting distracted by the newest, flashiest point solutions. Don’t let the buzz distract from the real tasks at hand: establishing a roadmap with phased milestones, gaining clarity around technology use cases, developing the required talent, and advancing IT infrastructure and integration to reach higher levels of orchestration.
MES Momentum
In 2018, we’ll see integrated Manufacturing Execution Systems (MES) re-emerge as a central component of Digital Manufacturing implementations. While there has been a flurry of activity and discussion around build-your-own (BYO) manufacturing apps, concerns about their security and reliability are building. BYO app proponents promise easy made-to-order point solutions, and mobile access to real-time metrics. It all sounds great until lack of strategic data architecture, integration, and control leaves you with you a mishmash of tools and apps that don’t play well together and can’t be efficiently maintained.
MES is still on top of implementation wish lists. Unlike custom BYO apps, MES provides coordinated data, security and workflow governance. The substantial benefits are well documented; every manufacturer wants to see their productivity and visibility increase while their time to market shrinks. Plants that get their act together and organize their manufacturing systems have seen a payoff — often tenfold.
MES platforms and integration tools aren’t frozen in time; they are being continuously improved and reshaped with new coordinating functions, industry-specific features, and more adaptive interfaces. Even as IIoT takes center stage, and platform vendors fuel the app craze, many smart manufacturers are rediscovering why MES capabilities are critical to coordinating processes across the factory and into the supply chain.
Driving Forces
Pioneering industry leaders figured out that the biggest value in digitally connecting processes and equipment is not the resulting analytics and intelligence — better metrics is more like the icing on the cake. The biggest value is to leverage connectivity in order to reach higher levels of orchestration and process optimization. The ability to extract and gather mountains of rich data is exciting (often overwhelmingly so) but the real value lies in higher quality products that require less time, effort, and money to produce; enhanced control over the supply chain, and radically improved integrated processes from design to production to maintenance. These outcomes should be the main driver for investment and implementation.
Sensors and data streams provide powerful mechanisms for bridging equipment and hardware to IT systems, but IIoT platforms are not a replacement for ERP, PLM, and MES. IIoT platforms provide great data acquisition, UI, and analytics tools, but that’s not enough. Organizing and putting context on manufacturing data is not trivial; making meaningful, efficient use of it requires manufacturing intelligence experience and specific data science skills. Clarity around IIoT platforms and various types of analytics will begin to crystallize as those who have struggled through early adoption focus on scaling the practical use cases for these tools alongside enterprise systems.
Astute IT teams are already rebelling against the wave of BYO apps. We know better than to allow silos of data to propagate all over the shop floor. Smart manufacturing is about architecting systems and processes around a single version of the truth (e.g., the Digital Thread and Digital Twin).
Over the next year, approaches to bridging operational technology (OT) on the shop floor to information technology (IT) and enterprise systems in a secured and controlled manner will mature. IT leaders should guide manufacturing BYO apps use by insisting on using MES experts to create, manage, and integrate them. MES developers will do their part by improving integration interfaces that enable IT to hook custom apps and devices like wireless smart glasses where they are needed on the shop floor while maintaining the same level of governance provided by native MES apps. We need to build in data sharing, digital handovers, and common integration architecture and semantics in order to deliver the full potential of connectivity and real-time data.
Getting Ready to Climb
Laying a solid foundation for Digital Manufacturing systems is paramount. Completing digital transformation initiatives is a multi-year process, and the outcomes will shape success and sustainability for even longer. Leadership buy-in, enterprise culture, and change management capabilities will play key roles. Security and interoperability standards are central. Workforce (re)training is a major issue that will require ongoing, industry-wide collaboration with education and government institutions gearing up to help. The groundwork is serious and substantial; be sure to start with solutions robust and flexible enough to support the journey.
Connectivity and real-time data are quickly becoming the new norm in manufacturing — paper-based systems are simply insufficient. To leverage promising technology innovations in Digital Manufacturing — technologies like smart machines, machine learning, augmented reality, OT-IT bridges, and robotics — the scaffolding of MES needs to be in place. Strategic, integrated implementation of these innovations is essential to the realization of the Model-Based Enterprise, the Digital Thread, and the resulting step improvements in optimization of operations, workforce, change management, supply chain, quality, and customer service.
We’re not sure how fast we’ll make it to the top of the mountain, but we know half the battle is packing the right tools for the journey. To reach new heights in 2018, harness the power of MES.
Conrad Leiva is VP Product Strategy and Alliances at iBASEt.