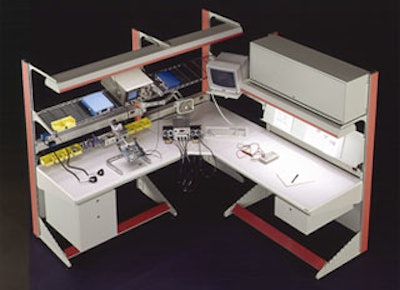
In today’s modern assembly facilities, the design and flexibility of the workstation is critical to maintain quality, workflow, and ergonomics. Unlike the old, static, welded frame workbenches and workstations of the past that were never moved or reconfigured, modern workstations incorporate a modular, flexible, adaptable design, with a wide variety of options that allows the end user tremendous flexibility in reconfiguring the furniture to meet an ever changing production environment.
Circuit board assembly used to be a fully mechanical process with through-hole components relying on bent leads to secure them to the board before manually applying solder. Component preparation was also a manual or semi-automated process to form, straighten or cut leads to facilitate assembly. Today, fully automated equipment handles most of those same operations, including X-ray inspection and in-line circuit inspection. As a result, the role of the workstation has evolved to accommodate a production staff that is highly trained to perform multiple high level functions, often at the same workstation. Productivity is more important than ever to maintain a competitive edge over offshore manufacturers, so the workstation must be designed to adapt and change as production requirements change. No longer is it acceptable to simply scrap that old workstation and start over just because it no longer meets your current needs. Workstation designs that allow for quick and easy reconfiguration is the only viable option in today’s competitive environment. Carefully researching the workstation systems on the market, while planning for future needs, will result in substantial cost savings over both the short and long term while providing considerable ergonomic advantages.
Workstations that are considered “state-of-the-art” can and will provide more than just a worksurface. Examples of features should include ESD protection, height adjustability, casters for mobile applications, cleanroom certification, shelving (solid or wire), overhead task lighting, tool and equipment stands, test equipment carts, mobile maintenance stations, overhead mounting options for electric tools, LCD monitor arms, tote bin bars, tool trollies, material transfer technology (ball transfer, conveyors, flow racking), and rack mount/enclosures for continued adaptability in a changing environment.
In a typical SMT assembly facility, these modular workstations can be found in a variety of areas, such as: machine programming centers, solder paste/metrology set-up, post process assembly of non-wets and odd form components, in-line inspection, box build assembly, rework and repair, product packaging, quality control, and supervisory or management areas. With a wide variety of module sizes available, nearly any possible configuration can be provided to meet the often limited footprint available in today’s modern assembly facility.
A variety of workstation styles are available to meet the specific requirements for nearly any manufacturing, lab or assembly application. Below is a brief description of styles along with advantages and disadvantages for comparison:
Basic 4-Leg Workstations
The 4-Leg Workstation is still a very popular configuration for many industrial applications as it provides a very solid, rigid platform that will support heavy loads (500 – 1000 lbs.) while still offering the option to add a variety of accessories above or below the worksurface. Examples shown above include a slotted upper back frame that can be added to accommodate a wide variety of accessories including shelves, task lighting, power and data bars, bin rails, and much more.
ADVANTAGES:
- The slotted frame allows the accessories to be located at any vertical position required for the application.
- Options such as drawers, keyboard platforms, CPU holders and footrests can easily be added below the worksurface to maximize use of all available space.
DISADVANTAGES:
- Often times the upper back frame will be narrower than the worksurface to allow the back frame to be mounted properly to the workstation frame. For example, if the worksurface is 72” wide, the upper back frame would be 60” wide.
- Weight capacity of shelving will typically be less than the shelving used on the slotted back frames.
A more conventional configuration would utilize the shelf and shelf riser option. The risers supporting the shelves can be provided with or without power or data ports. Power or data bars can also be mounted to the worksurface (between the shelf risers). Task lighting is available as an under-shelf mount style.
ADVANTAGES:
- This option is often selected to achieve a lower profile appearance and it often preferred if a more basic bench style is preferred.
DISADVANTAGES:
- Shelf height is not adjustable, and task lights can only be mounted below the shelf.
- Adding additional shelving can only be accomplished by stacking another shelf and riser combination.
Pedestal Style Workstation
The pedestal style workstation is often referred to as a “Lab Bench” or “Tech Bench.” This workstation configuration has been in existence for more than 50 years and is still very popular with wet and test labs typically found in universities, hospitals, biotech companies, and medical clinics.
ADVANTAGES:
- Very solid platform to support heavy equipment
- Excellent choice for tasks involving microscopes where vibration may be an issue
- Wide variety of storage and drawer options
- High capacity for power and data ports in the shelf risers and worksurface mounted power bars.
- Shelving supported with metal under-frame for higher weight capacity.
DISADVANTAGES:
- Shelf height is non-adjustable. Dictated by shelf riser height.
- Worksurface height is non-adjustable. Dictated by height of drawer or support pedestals.
Cantilever Style Workstations
The cantilever style workstation is the often considered to be the most versatile due to its modular design and high-tech appearance. The vertical columns used to support the worksurface, shelves and other accessories will vary from manufacturer to manufacturer, but typically they are offered in either a (1) front-slotted column or (2) aluminum extrusion equipped with slotting on the inside and outside face. Other than the overall appearance, both column styles work equally well to support the worksurface and any accessories required.
ADVANTAGES:
- Nearly infinite height adjustability for worksurface and accessories
- Excellent weight capacity
- Modular design allows for multiple workstation configurations
- Starter + Adder modules to achieve continuous worksurface runs
- Easily convert a single-sided workstation to double-sided
- Multiple column height options available.
- Wide variety of accessories and options available.
- High-tech appearance with many ergonomic features
DISADVANTAGES:
- There are few, if any disadvantages to the cantilever style workstations. This design combines the best of all other bench styles to give the user all the adjustability and accessory capacity to configure their assembly area in nearly any possible combination.
Electric or Hydraulic Height Adjustable Workstations
Workstations that offer height adjustability through the use of either hydraulic lift cylinders or linear actuator screw gear systems provide the end user with the next level of ergonomic advantages, especially if the assembly operation requires frequent working height changes. These lift systems control the worksurface height via manual hand crank or electric push button assist. Some linear actuator electric assist systems can even be programmed to adjust to a variety of preset heights by programming the control panel. Although these systems are more expensive than fixed height workstations, they off the end user complete control of the working height issues that are often associated with some assembly operations.
ADVANTAGES:
- Worksurface height is vertically adjustable via hand crank or electric assist
- Height adjustment range is 12”-15” overall, depending upon system selected.
- Weight capacity of lift systems range from 500 – 1000 lbs.
- Upper frames can be added to support shelves, lights, power bars and more.
- Casters can be added to make the workstation mobile.
DISADVANTAGES:
- Height adjustable systems are more expensive than fixed height workstations
As SMT assembly trends continue to evolve into the age of nano-electronics, how is the job function of your people and equipment going to change in the future? Lean manufacturing, as well as state and federal legislation, may also have an effect on the end users requirements for workstation designs of the future. While we don’t have the answers to those questions yet, we can be certain that workstation manufacturers will be working closely with the SMT industry to insure the designs will change as the industry dictates.
Read more at www.custom-products.com.