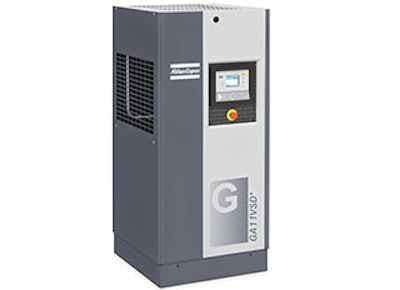
Members of Atlas Copco’s global product team launched the new GA VSD+ range of compact, oil-injected, rotary screw compressors that can reduce energy consumption by 50 percent compared to a traditional load/unload compressor of the same type.
The new range was designed with energy efficiency and customer needs in mind, with a motor that significantly exceeds the latest NEMA Premium efficiency requirements. Built upwards, like a mini skyscraper, the motor and drive train share a single drive shaft and are vertically aligned, reducing the total footprint by up to 55 percent compared to other compressors on the market. In addition, the motor drive train is completely enclosed, resulting in a NEMA 4 rating for protection against dust, debris and water. A single closed oil-circuit cools the motor and lubricates the element and bearings, resulting in a very reliable and compact compressor that is also extremely quiet (down to 62 dBA).
IMPO magazine talked to John Senay, Product Marketing Manager- Piston and Oil Injected Screws <30kW with Atlas Copco Compressors about the latest in energy-efficient compressor technology, NEMA Premium Efficiency requirements, and the future of energy efficiency.
Q: How are the latest energy-efficient compressor technologies becoming even more energy efficient?
In the last twelve months, the compressor industry has seen the release of several innovative, patented air compressor technologies that significantly reduce energy consumption. These recent advancements derive from improvements throughout the compressor design and contribute to dramatic increases in energy efficiency.
One of the most efficient compressor designs prior to 2013 was the variable speed drive (VSD) compressor, which provided average energy savings of 35 percent compared to a traditional load/unload compressor of the same type. After years of research and development, Atlas Copco has increased energy efficiency by up to 50 percent by revolutionizing the design of the VSD compressor and launching the VSD+ product line. These compressors use a vertically-aligned design where motor and drive train share a single drive shaft that significantly reduces the footprint, allowing the compressor to be installed closer to the point of use. The introduction of a single, closed oil-circuit that cools the motor while lubricating the element and bearings contributes to a more reliable compressor. A fan design that mimics the wings of an owl contributes to a highly efficient cooling mechanism while simultaneously decreasing noise levels.
All of these little changes make a big impact when combined in one air compressor. The simplified design of these compressors, coupled with advancements in technology, provide energy savings throughout the entire lifetime of the compressor.
Q: How can manufacturers best implement the latest and greatest energy efficient technologies?
Even with the significant efficiency developments in compressor technology, a recent poll conducted by Atlas Copco Compressors revealed that 64 percent of plants surveyed have not made any changes to their compressed air systems in the last two years. While compressor technology has evolved, many facilities are not yet benefitting from the potential energy savings that come with technology upgrades.
In order to implement the latest energy efficient technologies, manufacturers should first evaluate their compressed air system usage to determine potential savings from upgrading to more technologically advanced equipment. One easy way to determine production needs while minimizing operational running costs is through the employment of energy and air consultants who perform compressed air system audits.
An audit can range from basic inspections to a full audit survey. In all instances, an audit should highlight recommendations that improve system efficiency and reliability to ultimately lead to reduced operational costs. Typical savings range from a 30 percent to 50 percent reduction in operating costs if the customer implements all of the audit suggestions. The introduction of these changes will result in ongoing energy savings and increased profits.
Q: What are the advantages of a motor that exceeds the latest NEMA Premium efficiency requirements?
The number one advantage of a motor that exceeds the NEMA Premium efficiency requirements is the ongoing energy savings it provides through its efficiency. The NEMA Premium energy efficiency motors program was established to specify highly energy efficient products; NEMA Premium labeled electric motors help purchasers choose the most efficient motor systems, reduce electrical power consumption and costs, and improve system reliability. Air compressors with motors that exceed the latest NEMA Premium efficiency requirements significantly reduce overall energy consumption and put manufacturers in an excellent position to meet future efficiency requirements.
Q: What do you see for the future of energy efficient compressor technology?
The future of air compressor technology lies in the variable speed drive compressor. Before the introduction of highly energy-efficient VSD technology, a traditional load/unload compressor of the same type suited some manufacturing processes better than a VSD compressor. Now, with the introduction of VSD+ compressors that can reduce energy consumption by up to 50 percent, the traditional load/unload type of compressor can be replaced with a VSD compressor for the majority of processes. Additionally, the return on investment for switching to a VSD compressor is higher and the payback time is shorter than ever before.
The evolution of air compressor technology is a lot like the automobile industry. As new technologies that reduce fuel consumption are perfected, more drivers are demanding the new technologies in order save money and contribute to a healthier planet. The air compressor industry is also revolutionizing technology and offering a more sustainable option for compressed air users.
With rising energy costs and growing demands for environmentally sustainable processes, it has never been more important to implement technologies that reduce energy consumption. By investing in new technology, compressed air users can reduce energy consumption and operation and maintenance costs while increasing performance and contributing to a healthier, more sustainable planet.