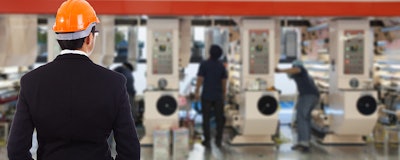
Streamlining old, redundant, or antiquated plant operations is the fastest way to reduce costs and increase profits.
Of course, there is waste during manufacturing and there is waste along the supply chain. You probably know the basic general manufacturing economics driving key issues, concerns, and spend. The real conversation to have is about the LEAN manufacturing process that you have in place, and whether or not you are exploring all the efficiencies available to further LEAN the supply chain, cost of acquisition, the number of hours required to produce a part, and the Work-in-Progress (WIP).
Moreover, when considering LEAN, and when comparing your company to peers, is your company operating at lower cost of operation coupled with a higher through/output per employee? Are you generating a great capital investment return on infrastructure, while operating with a continuous improvement mentality in every process that makes up the operation? What is the throughput in a given manufacturing hour? Is there room to implement consolidated billing?
How about automated replenishment via RFID, or a vending solution or some type of keep fill? Combined all these things these can eliminate or drive down the cost of acquisition for PO creation and/or number of invoices you may have to pay along the supply chain. Other factors that drive up costs but are easy to rectify include risk avoidance, lost-time accident prevention, and maintenance repair. You may also look at modern applications technology in metalworking or surface conditioning, such as abrasives, and find further avenues for improvement.
On a more granular level there are many hidden impediments that slow down production. Let's say you're a second-tier aerospace industry supplier for jet engines. How many hours does it take to produce the component? What can be done to apply modern technology to choose the right programming methods, cutting tools, geometry, and coding — even the right holding method? And so on.
Off the floor is another matter entirely. What is the process for purchasing the products that are used on the floor? What are the steps taken in the procurement process of those products? Are you stuck in the old three-bid process?
Oftentimes you can lower the cost for the way you procure these products, just by auditing the methodology for how you get them, dispense them, or replenish them at point-of-use. Wasted movement costs time and money, if you’re bringing these materials into a central storage, you also need folks to inventory, manage, and disperse them at point-of-use. For replenishment, instead of a minimum-maximum trigger, you could deploy an automated process that ensures the correct amount of materials are dispensed, with the least amount of effort, while eliminating lost time and product waste.
Again, it is absolutely paramount to LEAN your manufacturing and your supply chain because you are looking for it to be Just-in-Time, more predictive, and more analytical, while allowing data to drive key decisions proactively versus reactively. Auditing and upgrading processes requires bold action and commitment. For this article we’ll focus on issues specifically affecting metalworking and machine working.
Before identifying problem areas, first ask, are you really focused on reducing the cost of operations, not the piece price of the products you buy? The overall cost for this includes labor, machine utilization, and throughput-per-hour, as well as what can be invoiced per hour. One mistake that hugely impacts efficiency is Set-Up Time, which is a ripe area for improvement at almost any plant you walk into. When production waits with the machine spindle idle; or waits on it to be properly set up or waits for proper tooling to be placed in its proper position, all you are doing is eating away at profits.
The second thing to ask is are you deploying the best, most Modern Machining Practices, and are you using the most advanced cutting tools materials? You’ll probably find errors within the cutting tools themselves, in some cases specifically how they are held; or what the holding mechanism is; and then also, the process by which the tools are actually moved.
But you can't just rush in and make changes. This must be a collaborative, investigative approach driven by data that informs what is accurate/what is capable under your roof. Proper analysis, investigation, training, testing and coordination is required. You don't want to combine a modern cutter with an old holder, then move it like you always did. If you do it that way, it'll end up being a more expensive line item. You can't push a modern peg into an old hole!
Realistically, you may have to spend 30 to 50 percent more on that line item to get the best hold, movement, and training, but then your throughput will go up dramatically, along with higher integrity of machining that is also very defined and very controlled. Simple math tells us if the plant is producing 30 percent more product per hour in the same number of hours, it is worth far more than cutting the price 30 percent off a finished product. Best of all those savings go direct to the bottom line net profit.
With so many moving parts and stakeholders, improving plant efficiency across the floor and across the supply chain is a challenging and daunting task. You can read about it, you can hear about it, but ultimately you may find it is more difficult to apply these changes without guidance. As you begin to think about how you will improve your manufacturing and production capabilities, here's a quick checklist of common red flag areas to help get you started:
- Don't use Method and Tooling and Holders and Processes that mirror decades-old technology and thought process
- Reduce reliance on Undertrained/Undereducated Operators
- Control the manufacturing process from the engineering standpoint, then control how it's held and used from the top down versus old way of floor up. Education is the key, collaborate and focus on the future technologies
- Improve processes versus relying on cheap labor from emerging markets
- Analyze both production and the supply chain/cost of acquisition
- Look at investing in modern machine technology that can create extra capacity/lower the cost of manufacturing
- Educate employees and those affecting manufacturing
- Stair-step the re-engineering of manufacturing and supply chain processes across-the-board
Phillip Canipe is Vice President, Southwest Region at Stellar Industrial.