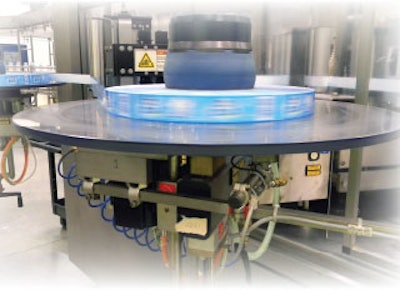
This article originally appeared in the January/February 2014 print issue of Food Manufacturing.
Nestlé Waters North America is the largest bottled water company by volume in the United States. The company prides itself on its sustainability efforts, including its many LEED-certified facilities and eco-friendly packaging.
The bottled water industry is a fast-growing market and the second largest commercial beverage category by volume in the United States, according to the International Bottled Water Association. The Beverage Marketing Corporation states that in 2013, U.S. consumers drank 10.1 billion gallons of bottled water — an average of 31.8 gallons per person.The industry owes much of its success to increasing health concerns, as many shoppers are making the switch from sodas to bottled water. Many bottled water companies also are making an effort to supply consumers with a sustainable packaging option by increasing the amount of recycled plastic used in their bottles, as well as by “lightweighting,” or reducing the overall weight of plastic used to produce the bottles.
One company on the forefront of these sustainable practices is Nestlé Waters North America, the largest bottled water company by volume in the U.S. Headquartered in Stamford, Conn., Nestlé Waters employees approximately 7,500 workers in its 29 plants located throughout the U.S. and Canada.
The company produces various types of bottled water including spring, purified, sparkling, drinking, distilled, mineral and flavored water, as well as ready-to-drink tea. Nestlé bottled waters are sold through retail outlets and also are distributed directly to home and office delivery customers. The company runs America’s largest beverage delivery system, serving more than 1 million customers.
A Pure Process
Nestlé Waters has two bottling facilities at its Allentown Campus in Breinigsville, Pa., with additional spring sites in seven locations throughout eastern Pennsylvania. The Allentown Campus produces bottled water for retail sale, with one facility bottling Deer Park® Natural Spring Water and the other focusing on Nestlé Pure Life® Purified Water.
There is a clear distinction between the Deer Park and Nestlé Pure Life waters produced at the Allentown Campus.
Spring water like Deer Park is collected from the spring water sites, where water is loaded into a tanker truck and taken to the facility where the water is offloaded into silos. From the silos, the water goes through a microfiltration process, which removes any inorganics, such as clay particles without changing the mineral content of the water. The water then goes through ultraviolet treatment before being packaged into bottles. Because the mineral content of spring water does not change, Nestlé is able to label its spring water as a natural product.
Nestle Pure Life is a purified water product received by pipeline from the local municipal water supply. Once this water is received, it travels through a carbon filtration system that removes chlorine from the water. The water is then sent through reverse osmosis filtration, which removes dissolved minerals and any unwanted contaminants that may be present in the water. The filtered product is finally sent through a remineralization process to add minerals back into the water in order to create a flavorful product.
Bottled water products must meet unique drinking water regulations. The Food and Drug Administration requires that bottled water meet the same — and sometimes more stringent — standards as those for tap water. Throughout production, samples are taken from every bottling line to ensure products meet FDA regulations, as well as Nestlé’s internal standards for both quality and taste.
The Lightweight Champion
Nestlé Waters maintains a strong focus on lightweighting its bottles. Both Deer Park and Nestle Pure Life liter-sized bottles use 33 percent less plastic than comparable bottles, making it the lightest branded liter-sized bottle produced. This results in less fuel and carbon, as well as fewer materials used to produce the raw resin that goes into the plastic bottles.
The 580,000-square-foot Nestlé Pure Life East facility on the Allentown Campus produces a 0.5-liter bottle in various pack sizes. All six of the plant’s bottle-production lines produce the Eco-Shape™ bottle, a 0.5-liter bottle that weighs 9.16 grams. This bottle contains 25 percent less plastic than the previous Eco-Shape bottle, and 60 percent less plastic than Nestlé’s original, pre-Eco-Shape 0.5-liter PET bottle that was first introduced in the mid-1990s.
Nestlé Waters also produces a 0.5-liter bottle that is 8.99 grams, as well as an 8-ounce bottle weighing in at 7.95 grams. The company currently is working to lighten their bottles even further, with the lowest-weight 0.5-liter bottle currently down to 7.53 grams.
Nestlé is always in the pursuit of lightweighting, says Michael Franceschetti, Factory Manager of the Nestlé Pure Life East plant. “We keep on reducing the amount of plastic in our bottles,” he says. “Imagination is amazing. The technology available for lightweighting now allows you to put a bottle out to the consumer that has very little plastic in it, which is important to us.”
Not only does the Nestlé Pure Life East plant process water, but it also creates its own plastic bottles. The facility houses seven injection machines designed to produce preforms, which are small, test-tube-like plastic vessels that will eventually become full-size bottles.
Preforms flow down the line into the blow molders, where the preforms are stretched into bottles. At peak production, the Pure Life East plant can produce more than 9 million bottles per day. Finished bottles are then filled with their corresponding water products.
The process from creating the preform to a finished product takes about a half-hour. Finished products quickly make their way to grocery shelves, Franceschetti says. “There’s been days when I walked down to the supermarket and saw our product on the shelf that was produced the same day.”
Finished product not immediately shipped to retail customers is stored in the Pure Life East facility’s warehouse, which can hold approximately 1.6 million cases of inventory.
The Nestlé Pure Life East plant makes approximately 2.8 million preforms per year. About 1.6 million preforms are utilized in the Pure Life East facility, while the rest are sent to its sister plant. Franceschetti says that producing preforms helps enhance the plant’s efficiency and performance. “[Producing our own preforms] helps make us self-sufficient as a manufacturing business.”
Sustainability Matters
Nestlé Waters maintains a strong commitment to sustainability. The company was the first beverage manufacturer in the U.S. to build a facility that received the U.S. Green Building Council’s Leadership in Energy and Environmental Design (LEED) Certification. Today, Nestlé Waters has 10 LEED certified plants, encompassing 3.7 million square feet.
The Nestlé Waters Pure Life East plant received LEED Gold Certification in 2009, becoming the first food manufacturing facility in Pennsylvania to obtain that status.
The plant was designed with a focus on the environment. The facility saves 66 kWh of electrical energy per 1,000 liters of bottled water produced, due to onsite bottle production, ongoing reducing of plastic used in bottles, use of natural light and light conservation, and heat energy recovery. In addition, the plant conserves about 220,000 gallons of water each year.
The value of sustainability also shines through in the Allentown Campus’ day-to-day operations. The two facilities have achieved a 100 percent recycling rate for materials including corrugate, PET, LDPE, HDPE, preforms and pallets. By increasing communication and improving utilization of its tanker fleet, the plants have been able to reduce their number of tankers on the road by 1,200 annually.
Franceschetti says Nestlé Waters commitment to sustainable business practices not only benefits the company — it helps the consumer as well. “It’s about the environment and using less resources to be able to service our customer sustainably.”
By maintaining self-sufficient production practices and sustainability efforts, Nestlé Waters can look forward to smooth sailing.