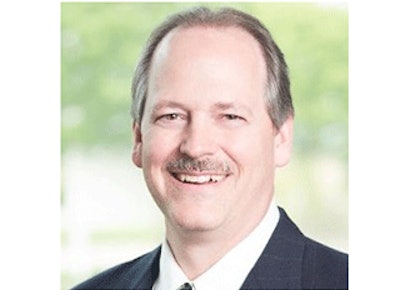
From the book The Omnivore’s Dilemma to the documentary Food, Inc., the public is more educated than ever about where they get their food and what happens as it travels from farm to fork.
Along with that vested interest, the government has in recent years boosted its oversight of the food supply chain through the most aggressive regulatory overhaul since the mid-20th Century. Though the FDA has exercised its right to mandatory recalls a handful of times, every year hundreds of voluntary food recalls threaten the reputation of the brands that sell them.
As a result of these legal and cultural influences, businesses must be deeply aware of the systems and solutions they have in place to comply with new laws, respond to changing customer habits and preserve their brand in the event of a recall. Each factor poses challenges for the industry but also opportunities for positioning your company as a responsive, proactive leader in mitigating risk.
Capturing the Right Data
The FDA’s Food Safety Modernization Act (FSMA), signed into law in 2011, installed the most comprehensive food safety laws the U.S. has ever seen. Traceability and robust record keeping are central to compliance as companies may need to prove they’re documenting the right information at a moment’s notice.
FSMA puts greater emphasis on foodborne illness prevention than previous regulations, which took a more reactive approach. The laws hold every link of the supply chain accountable and require companies to closely monitor their operations.
This involves capturing the right data when a product comes in a facility’s door, tracking its lifecycle while it’s there, and delivering complete visibility into who it’s been shipped to and when. If there’s a recall, the regulations put the burden on distributors to make sure they’ve tracked the products, traced them to their destinations and can assist in returning them to the vendor.
Fortunately, there are solutions that can help ensure this process goes off smoothly. Software systems on the market enable you to capture and store detailed information so you can efficiently provide reports to officials and notify facilities downstream in the supply chain if they’ve received a recalled product.
Supporting a Quick Trip from Farm to Fork
The local, natural foods movement has been one of the most sweeping trends in recent years, as consumers opt for fresh veggies, fruits, meat, dairy and more produced within a tight radius of their homes. Neither strawberries shipped out of season from Mexico to Chicago, nor bags upon bags of frozen foods will cut it anymore for many consumers.
The trend, however, requires greater agility from the supply chain to get fresh produce to the table within a shorter timeframe. In the past, distributors could predict a few weeks or even a month in advance what would be coming through their facilities. Now they must identify what’s coming out today that they’ll distribute tomorrow. In some cases, they must re-plan the whole system multiple times in a single 24-hour period.
As a result, warehouses have become even more dynamic environments as they shift to meet rapidly changing demands. They must carefully integrate a workable plan with their warehouse management systems and be prepared to adapt that plan so they can quickly respond to orders as they arrive and move them into the next phase of the supply chain.
Reining in Recalls
No matter the reason—labels that don’t mention allergens, bacteria-tainted lunch meat—food recalls are never good for business. The pressure is greater than ever in this 24/7, social-media fueled news cycle. A family farm could be out of business overnight as a result of a listeria outbreak.
But how companies handle food safety issues that arise is just as important as trying to prevent them in the first place.
Instant access to information about the products flowing through the supply chain allows companies to craft a more intelligent response to a crisis. Rather than waiting a week or more, distributors can make quick, fact-based decisions with the help of software that collects data from their operations.
A perceived lack of response is almost as deadly as not responding at all. But once you have the information you need, you can spread the message that the company knows what happened, has a plan for handling it, and has begun recalling the right products.
While these recent shifts have complicated the food supply chain, a fresh approach to the technology and systems that support your business will keep risk at bay.
Bill Tomasi is Global Director of Product Management at IBS, a world leader in distribution resource management software, providing ERP and WMS business applications for the wholesale, distribution and manufacturer/distributor markets. For more information about IBS, or to contact Mr. Tomasi, email [email protected].