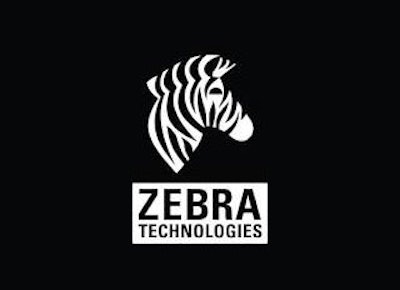
In difficult economic times, Lean thinking strikes a chord for manufacturers as it promises to reduce costs, improve quality and transform the bottom line by eliminating waste in every area of the value stream, including factory management and supplier networks. Its goal is to eliminate non-value added processing from the customers’ perspective, enabling less inventory, less space, less resource, less time and less cost to produce more – and all highly responsive to customer demand.
Lean manufacturing is about the obsessive elimination of waste – waste being defined by lean practitioners as what customers would perceive as processes and actions that don’t add ‘value’, and for which they don’t want to pay. Given the current difficult conditions for much of manufacturing in the developed world, lean is also commonly associated with getting more from less. But for the tightest definition, go to the U.S. National Institute of Standards and Technology (NIST) Manufacturing Extension Partnership (MEP), which describes lean as “A systematic approach to identifying and eliminating waste through continuous improvement, flowing the product at the pull of the customer in pursuit of perfection.”
Succinct, yes, but useful too because implicit in that sentence is a clear warning for Lean manufacturing wannabes to avoid cherry picking lean initiatives and methodologies – such as simply setting up kanban replenishment, focusing on reducing set-up times, or doing the workplace 5Ss (sort, set in order, shine, standardize and sustain) somewhere in production or a warehouse. Instead, this definition of lean manufacturing leads instantly to the strategic, top down view, as enshrined in lean’s five governing principles.
First, deliver value with, as above, the customer at front of mind. Second, identify the value stream (by value stream mapping all the stages of production, warehousing and ultimately the entire business). Third, make the value flow, with a goal (mostly unreachable) of single piece flow, by moving from the current state to a chosen future state – and remembering, crucially, that information also needs to flow. Fourth, make-to-order, meaning only make or do anything when you need to – using, for example, JIT (just in time) principles. And fifth, strive for (almost unattainable) perfection, using the methodologies and tools for both continuous and blitz (kaizen) improvements. Underpinning all of that thinking is removal of the seven prevalent wastes of lean manufacturing – those aspects that, again, fail to add value.