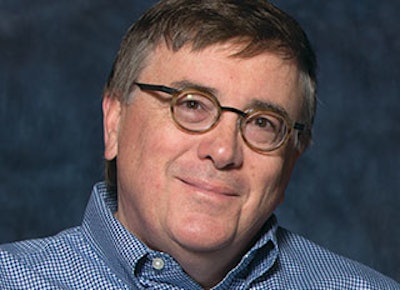
This article originally appeared in the May/June 2014 print issue of Food Manufacturing.
The Food Manufacturing Brainstorm features industry experts sharing their perspectives on issues critical to the overall food industry marketplace. In this issue, we ask: Which innovations in food labeling should food manufacturers be paying attention to, what benefits do they offer and how are they best implemented?
The greatest innovation in roll-fed labeling is happening in adhesive application. Roll-fed labelers have used multiple versions of a rotating glue wheel system since the invention of roll-fed labeling over 40 years ago. This technology is proven and widely used, but it has several inherent deficiencies:
- Voids in applied glue patterns
- Inconsistent glue application
- Limited control over amount of glue applied to a label
- Glue slinging, stringing and build-up
- Glue degradation caused by repeated recirculation and overheating
- Multiple mechanical components that make set-up, operation and maintenance difficult
Recent innovations that are being offered as alternatives to the traditional glue wheel system include spray application systems, label reels with adhesive pre-applied to the label web, and extrusion application systems.
From my perspective, extrusion-based systems have the greatest potential to become ‘what’s next’ in roll-fed labeling.
Extrusion technology provides a platform for fully automatic, recipe-driven, hot melt adhesive application. Unlike spray systems for roll-fed labeling, which are limited in speed and high in maintenance, a PLC-driven extrusion system can precisely extrude a film of hot melt adhesive and apply it to preprogrammed locations on a label. Using a controlled combination of pressure and temperature, extrusion technology delivers consistent, void-free glue patterns of adhesive to labels regardless of changes in production speed.
In addition to improving the accuracy of glue application, extrusion technology reduces glue recirculation and reheating by more than 90 percent and it eliminates dozens of mechanical components, thereby reducing glue waste, improving labeling quality and increasing uptime by making the labeler easier to set-up, operate and maintain.
Another unique advantage of an extrusion based system is its ability to use a wide range of hot melt adhesives never before used for roll-fed labeling. This capability is based on the fact that extrusion can smoothly process adhesives that simply will not run on glue wheel or spray glue systems. This may prove to be the greatest breakthrough offered by an extrusion based glue application system.
Manufacturers should be aware of all innovations related to glue application, and they should fully understand and evaluate these new technologies before deciding which approach is best for their application.