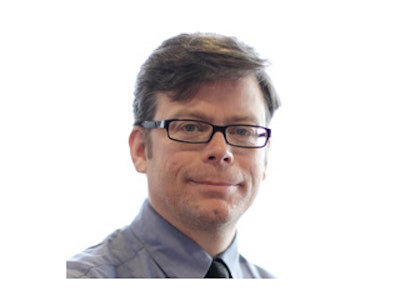
Just-in-time (JIT) deliveries, little to no inventory, outsourcing, sole sourcing — all of these “lean” concepts have been at the heart of operations management for years now. But more and more companies are starting to ask themselves a simple question: Just how lean do we really want to be? In answering that question, many are starting to rethink the way they manage their processes and supply chains.
The first warning shot across the bow of lean, and a sign that supply chains might be overstretched, came in the form of the Severe Acute Respiratory Syndrome (SARS) outbreak in China in 2002-2003. While the epidemic caused some delivery delays and lost sales, for the most part manufacturing in the region went undisturbed, so companies continued looking for ways to keep their supply chain lean.
Tom McNamaraClose to 10 years later, a series of unfortunate events began with an earthquake and tsunami hitting Japan in March of 2011. In contrast to the relatively subtle supply chain shifts which resulted from the SARS outbreak, this dual disaster caused many local automotive suppliers to completely shut down, resulting in worldwide shortages of vital components.
In November of that same year, major flooding struck Thailand, throwing the supply chains of several high-tech companies into utter disarray. Seagate, a major provider of hard drives for PCs, said at the time that it would probably take two years to get its supply chain back to normal. Shortly thereafter, in 2012, a major explosion at a specialized chemical plant in Germany (Evonik Industries) resulted in global automotive supply chain disruptions and compromised manufacturing across the globe.
A key lean trend is consolidating suppliers and doing away with redundancies. Although this certainly creates cost efficiencies, the main suppliers who are left quite often end up providing needed parts to many companies in the same industry. And if these companies are all depending on the same supplier, or only a few suppliers, unforeseen production problems or sudden shifts in demand can easily send ripples throughout multiple systems.
[Continue reading...]