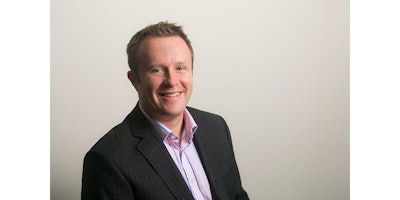
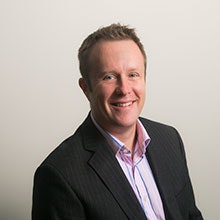
The food value chain is complex and elongated when you consider the entire process from raw materials and ingredients to formulations and recipe development, production and consumerization. The complexity is magnified by factors such as differences in cross border regulation, distributed cross border manufacturing processes and large raw materials and ingredient supplier networks.
Food companies are under pressure from various angles — from speed to market to compliance and delivering innovative new food products rapidly, to reducing costs/applying efficiency gains, to overall operations. Each one of can be impacted in some fashion with technology and data management.
So what areas or departmental groups of the food production value chain that can be "tooled up" with technology and which ones can see the consequential benefits? All of them.
To compete, meet regulations and address their business pressures, food companies need to answer fundamental questions such as:
- Can we use this ingredient in production for sale in this specific country? This allows companies to rapidly repurpose existing products or alter a raw material/ingredient/formulation to take advantage of a new opportunity.
- What raw materials are part of this ingredient batch? This allows companies to rapidly get a handle on any potential regulatory implications thus reducing their overall risk exposure.
- There is an issue with this batch of raw material — what batches of current product are affected and in which regions?
- What changes to formulation X do we need to make to be able to sell this product in country Y? This allows an existing product to be rapidly re-formulated to meet regional specifications.
- What opportunities do we have to reduce the cost of production by changing raw materials and ingredients? This allows for a production process or material sourcing to be quickly assessed when making decisions to create a new product.
- Have we made anything like this before? This allows for the rapid exploration of existing know-how so that to accelerate new product development.
- Can we change this ingredient with an alternative? This allows for assessments to be made on downstream implications of an ingredient change.
This list of questions is not exhaustive, but each of these have can potentially impact the business’ bottom line.
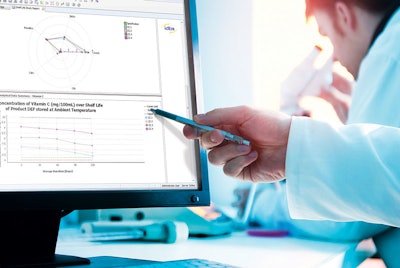
Samples and Material Tracking
There are many industry standards for the sharing and publication of raw materials and ingredient information, but that available information needs to proliferate through the value chain. It is good to have the pallet on the loading bay and to know what is in it, where it has come from and what has happened to it. However, when this raw material is used in downstream processes to produce ingredients and products, that information needs to be "inherited" and "surfaced" when necessary.
This problem is called genealogy. This is the relationship of something to their parents and children. In this context, it is the systematic linking of all "parents" — raw materials, into "children" — including ingredients and formulation, all the way through to final product batches.
This sounds simple, but is complicated by the various relationships that exists when multiple raw materials go into an ingredient that goes into multiple products.
Tracking this critical genealogy manually can be very time consuming and difficult. Data management systems designed to provide a rapid view of both upstream and downstream relationships of various elements can reduce time taken to answer the important questions and enable business agility and regulatory compliance.
Collecting Reusable Data in the Early Stages of Food Production
Everything that is done during the food production value chain needs addressing at the data management level. When something is tested, from raw material to the ingredient of final food product, the results of that testing need to be accessible with all associated contextual information available. It means that when the value is captured — let’s take something simple like pH or color — it needs to be captured in a way that makes it reusable and consumable. It cannot be stored in a document or spreadsheet as text or in a cell. It must be captured in a way that means the value is known to be pH 7.8 or viscosity 4.5T. If the data is stored and captured this way, it is consumable and can be easily managed by others.
The above pH and viscosity example is simple, but when you extrapolate this to a formulation process or manufacturing process where every parameter, unit operation and process step can be identified, reported and linked to other results, the power and value increases dramatically. For example, where have we used a formulation unit operation of extrusion at <20 microns and what was the resulting texture like in taste testing? Now this data has significant value and can help with new product development and innovation — try finding that in a report in the corporate document store.
This is not to say that "unstructured" data is not also important. Take an example — “we left the milling to run for an extra 10 seconds” — the overall texture and tracked parameters were not affected but someone then noticed a 5 percent increase in yield downstream. Now the causal nature of these things needs to be tested but the value is obvious for innovation and intrinsic corporate knowledge exploitation.
Formulations & Recipe Development
As said earlier, answering questions is at the heart of where IT can help in the food value chain. So let’s take another example.
Where is that tasty recipe that we developed 20 years ago that we canned (excuse the pun) due to customer feedback? They didn’t like the taste then, but new consumer feedback shows that a customer segment actually wants something like that now.
Now, the creation of a formulation is a tricky and intricate business — it involves lots of process steps, ingredients and testing — both analytical and taste. Unit operations are combined and changed to see how each element affects the overall outcome of the process on the food product.
To answer the formulation question above, the testing result needs to be captured in a way that makes it retrievable. Writing it in a spreadsheet or text document does not make it readily available. The data must be structured to enable the rapid identification of the relevant recipe by a set of key attributes.
Manufacturing
Execution control, real time feedback on manufacturing processes, regulatory and QA implications all play a big role in how manufacturing is organized and managed. This area, much more than any other, has been effectively supported for a long time by IT and data management, PAT (Process Automation Technologies), MES (Manufacturing Execution System) and robotics. With this history, the manufacturing side of many organizations is the one that is the most developed and robust, using process automation to reduce regulatory risk and optimize processes.
Market Feedback
How is our new product doing in the market post launch? Structured and unstructured data is combined and analyzed for trends using a variety of sources — the days of post-launch questionnaires being conducted by people with clipboards are numbered. These various streams of feedback are already providing food companies with valuable insights into how the brands and products are faring in near real time. The key will be combining it with other data elements and structuring it in a way so that it can be effectively consumed by the upstream parts of the value chain.
Summary — The Power of Data in the Food Production Value Chain
Food is of great importance to everyone and the value of data to companies that operate within this space should not be underestimated. However, the structure and type of data that is collected and how it is collected is of great importance if it is to be of use and value. Properly structured, reusable and connected information is critical in answering typical regulatory or research and development questions quickly. A knowledge base of well-structured data, properly linked and covering end-to-end, raw material to product should be treated as a corporate asset. Furthermore, if used properly, this connected data can provide value to organizations against the backdrop of the typical business drivers of innovation, new product release speed and regulatory compliance. So collect data once, connect it to other data to maintain context and collect it properly so it is reusable and can be surfaced when and where you need it and then reap the rewards.