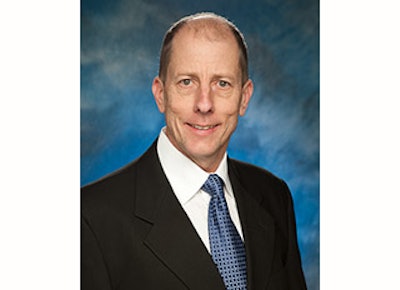
Chem.Info sat down with Andrew Scherz, Senior Product Manager at Epson America, to talk about the GHS deadlines chemical companies now face and offer some strategies for a smooth implementation of the new standards.
Q: Can you break down some of the key facets of the GHS changes?
A: There are two key drivers coming together to spur the need for the Occupational Safety and Health Administration’s (OSHA) upcoming GHS requirements. First, the expansion of global commerce is shrinking our world while simultaneously requiring more entities (e.g., nations, regulatory agencies and businesses) to collaborate on ways to standardize safety and shipping information across borders. Secondly, demand for worker safety continues to be a growing priority. This year alone, ‘hazard communication’ was ranked second on OSHA’s list of top 10 violations. Put these two factors together and it raises the challenge as to how companies can ship hazardous materials all over the world without exposing workers to unknown risks.
To try and solve this challenge, an international standard for labeling hazardous goods was established. Known as the Globally Harmonized System of Classification and Labeling of Chemicals, in the U.S. this standard is being integrated into OSHA’s revised Hazard Communications Standard (HCS). The prevailing notion behind GHS is to use internationally recognized pictograms which can be comprehended regardless of regional dialect to communicate critical chemical handling and safety information to workers even if they cannot read the label. This is the core purpose of GHS in a nutshell.
Q: What are the key deadlines companies must be aware of?
A: There are four critical dates companies must adhere to:
•December 1, 2013 – Employers are responsible for training workers on the new label elements and Safety Data Sheet (SDS) format. Less than one month away, this deadline is particularly important because companies abroad and domestically have already begun shipping products using the new GHS-compliant labeling requirements.
•June 1, 2015 – Chemical manufacturers and distributors must complete reclassification of chemicals and fully comply with the new GHS standards. In addition, labels and SDS’s must be updated to comply with the new GHS-formatting.
•December 1, 2015 – Distributors have a six month allowance until this date to ship products labeled under the old system. Beyond this exception, distributors must comply with all of the GHS provisions under the revised HCS.
•June 1, 2016 – From training to updated workplace documents, employers must be fully compliant with the new GHS standards including any new updates to hazards or program revisions.
Q: What are the greatest impacts on the processing industries?
A: The simplest and most critical impact is that labeling of hazardous goods will become much more complicated and challenging. Firstly, existing labels that are being used to identify chemicals in the workplace will no longer be considered legally compliant by OSHA. Additionally, the new GHS compliant label formats will need to meet more stringent standards for text and graphics. Therefore, chemical manufacturers will have to place added care on managing the data featured on these labels.
The required changes under GHS also involve the inclusion of very specific graphics. To provide a clear, internationally recognized architecture of hazard types, the GHS standards mandate the use of colored pictograms. From an implementation and technology perspective, this means that traditional monochrome printer technologies will no longer suffice for printing the new label designs. Therefore, manufacturers must ensure that both their software and printing hardware are capable of capturing required content onto the new GHS label structure.
Q: What are their options in terms of methods for complying?
A: Companies will need to manage new label content and printing technology to achieve GHS compliance. For larger companies with an array of formulations that must be shipped to diverse regions, integrating sophisticated software systems provided by companies like the Wercs and 3E can streamline operations and ensure that chemical labels have accurate product information. For smaller companies with fewer designs, the new content can likely be managed in-house or with the help of a compliance consultant.
With regards to printing technology, manufacturers need to explore printers capable of producing the new colored pictograms. Manufacturers can select from a broad portfolio of technologies including: two color thermal transfer, color laser and color ink jet. There are pros and cons to each technology, but in general, ink jet provides the lowest up front equipment cost, the lowest cost per label and the greatest label image durability. For the large majority of applications, Epson’s color ink jet technology is an excellent overall solution.
Q: How does Epson’s technology meet these needs?
A: Epson's industrial color label printers are designed for high-duty, commercial environments. These printers leverage Epson’s proprietary pigment inks to deliver incredibly durable images, especially when coupled with special polyethylene label stock. This ink media combination is incredibly durable; it is the first ink jet solution to achieve strict BS 5609 certification. Required by chemical shippers, this standard ensures that labeling is chemical and water-resistant so that labels do not degrade, smudge or fade. Not all printer and media combinations can meet this standard.
Epson’s on demand color labeling solutions produce vibrant images, ensuring that all label aspects are clear and vivid including branding and graphics. From an operational standpoint, Epson’s ink jet solutions create a simplified, one step process that reduces inventory of labels to blank stock and provides the flexibility to print finished labels on demand as needed. If any branding, graphics, color highlights or pictograms change, there is no need to throw away pre-printed stock. Everything is produced instantly, in the exact format that is required.
Q: How do you get plant managers/decision makers to buy into this technology?
A: Seeing is believing. The best sales pitch we have is getting a real label sample in front of managers. The first thing they will see is how great it looks, but the acid test resonates with them on a whole different level. Every plant manager has concerns about various materials that will destroy or degrade labels that are used to communicate key information. Letting plant managers get their hands on a sample and apply alcohol, acetone or other harsh chemicals that labels are likely to encounter is ultimately one of the most compelling ways we can communicate durability. In an environment where workplace safety largely depends on clear label communications, label durability can be a huge area of concern. But with the acid test, once they get a hold of a sample and try to destroy it, the label’s resounding durability serves as a strong testament to the technology.
Want to hear more about navigating the steps towards GHS compliance? Check out Andy's presentation at The Chem Show: "Guiding Operations Towards GHS Compliance," a part of the 'Environmental Issues In Manufacturing' series, Dec. 11th at 10:30-12:00pm EST.