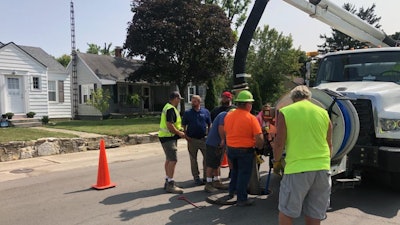
Sewer maintenance is an ongoing challenge for cities and municipalities. Moreover, gaps in best practice training can cost public works departments unnecessary time and expense in labor, water and energy costs when cleaning sewer lines.
Making matters worse, our comprehension of sewer line cleaning has evolved alongside the advancements in hose nozzle technologies, which in some cases directly contradicts current practices. So, when conducting training classes across North America, Dan Story, an Operations Manager and national trainer at KEG Technologies, first addresses a common misconception. Many have been trained to quickly run sewer line hoses up the line to effectively remove debris. However, this “hurry up and clean” approach is counterproductive and can potentially redirect sewage flow into homes, commonly known as “blown toilets.”
“For years, sewer maintenance crews have been taught to shoot a nozzle up a line in a hurry and clean as they come back,” said Story, whose company provides Tier 1 to Tier 3 nozzles, chain cutters, floor cleaners and camera nozzle systems to the industry. “But this is not a race. If you are not slowing down to cover all the ground, it simply is not going to work very well.”
Instead Story trains sewer crews to “clean as you go in and rinse as you come out,” added Story. “With this approach, 95% of the time you will clean a line in one pass instead of making a whole lot of passes.”
For Story, who travels across the United States and Canada conducting training on sewer cleaning techniques, misconceptions abound in the industry and often reflect a lack of understanding of the fluid dynamics of high pressure nozzles. Over time, additional best practices have been developed through a process of trial and error.
As part of his training sessions, Story provides the following additional tips for sewage line cleaning:
“Read” the results
Story said you can learn a lot by paying attention to what is happening in the line going in and coming back.
“Crews need to be trained to understand what they are ‘reading’ coming out of the pipe. The information can tell you whether you are going too fast or too slow, how much debris is in the line and whether the line is clean after the first pass – or not,” said Story.
When going up the line, for example, it is beneficial to observe the amount of debris present.
“If there is minimal debris returning, it indicates that the pipe is in relatively good condition, with a low accumulation of debris. So, I can accelerate my speed. However, an excessive amount of recovered material suggests the need to slow down. In such cases, the flow of water acts as a conveyor belt, effectively carrying the debris out.”
When the water flow confirms the pipe has been cleaned at the right speed, the maintenance crew can then lower the pressure in the hose to between 900 – 1,000 PSI and come back through the pipe at the same speed. This final single “rinsing” pass can leave the line totally clean.
“The trick is paying attention to your hose. Make sure your hose comes back clean and then you know your pipe is clean. How much debris is in the first pass? This information can tell you whether you’re going too fast or too slow. Remember to never outrun your flow because your flow is your conveyor belt. If there is a lot of material on the hose, it is telling me to slow down. If my hose stays clean, I know I am moving at a good pace,” said Story.
Another common sewer cleaning misconception is that you don’t need to open the upstream manhole when cleaning sewer pipes. This can actually increase pressure in the system and lead to blown toilets, where sewer gases flow up the laterals and cause sewage water to overflow from residential toilets.
According to Story, approximately 95% of blown toilets can be attributed to how the operator cleans the lines. However, identifying certain signs can help mitigate these issues. For instance, a sudden rush of water during the return flow could indicate the upstream manhole was closed instead of being left open.
Protect your investment
Slowing down and observing the results allows for cleaning to be performed in a single pass, which helps safeguard the hose from potential damage.
“If you are going into each pipe once, rather than three times, to clean it, you are basically tripling the life of a three to four thousand dollar hose,” said Story.
Beyond the wear and tear on the equipment there are also operational costs to consider such as water, fuel, as well as the productivity of the operators. “Cleaning more efficiently and effectively means lowering the operating costs per pipe and increasing what a city’s public works department can do,” explained Story. “And today, everybody is trying to figure out how to do more with less.”
A very high-efficiency Tier-3 nozzle running 60 gallons a minute at 2,000 PSI will impact a plate nine feet away with 98 pounds of force.KEG Technologies
Nozzle selection matters
Story cautions departments not to overlook the importance of nozzles even when expensive trucks are purchased for providing a water supply. While a department may have invested a half-million dollars for a truck to clean sewer lines, its impact is only as good as the nozzle at the end of the hose. “If you are using a cheap hundred dollar nozzle, well now you have a hundred dollar truck because it is the nozzle that cleans all of the pipe, not the truck,” explained Story.
As is known throughout the industry, there are tiers of nozzles which are rated for water efficiency from Tier 1 (about 30% efficient), Tier 2 (50-60% efficient), to Tier 3 (75-98% efficient).
However, even within the Tier 3 category, there are significant differences in levels of efficiency. Opting for the lower end Tier 3 nozzle with 75% efficiency could still lead to additional trips to refill. Also, such units may not remove restrictive sewer buildup or blockage in a timely manner.
According to Story, a Tier-1, 30-degree drilled nozzle running 72 gallons a minute at 2,200 PSI will only exert 13 pounds of force to move debris nine feet away from the nozzle. In contrast, a very high-efficiency Tier-3 nozzle running 60 gallons a minute at 2,000 PSI will impact that plate nine feet away with 98 pounds of force.
“When you put the right nozzle on, you can do things that you never thought were possible,” said Story. “You will not have to sit there and spend all day doing what you need to do.”
What sets the most efficient Tier 3 nozzles apart from others in the category is fluid mechanics engineering on a par with the aerodynamics of race cars or jet fighters.
In the case of KEG’s Tier 3 nozzles, the high-performance fluid mechanics design leaves little room for power losses and excessive turbulence. After exiting the jetter hose, water travels into the body of the nozzle before moving through smooth, curved channels. This design enables the water to maintain its power and speed before entering the nozzle’s replaceable titanium ceramic inserts. Next, the water is funneled from a short conical shape to a larger, longer cylindrical shape, allowing a tight water pattern to emerge.
The internal workings of the nozzle, including the way the water gets turned, redirect the energy of the high-pressure water entering the nozzle as efficiently as possible. This results in what is needed for the task: more thrust and power using less water.
Optimal technique is key
Effective cleaning involves more than just using a powerful nozzle. It also entails understanding the proper positioning and placement of the nozzle within the pipe.
“We teach about the difference between laying a nozzle on the bottom of the pipe and centering it into the pipe,” said Story. “We teach about the flows and angles based on the size of the pipe -and the condition of the pipe based on the last camera footage.”
KEG trainers teach how to use a banked turn with the water hose to get more power with less water.
“If there is an issue with roots or heavy grease, you want to use a controlled rotation nozzle which will cut and chop it up enough to avoid debris going through the manhole and creating blockages downstream,” said Story. He recommends using a nozzle capable of breaking up blockages to a particulate size small enough to go all the way to the treatment plant without creating a problem downstream.
The science behind best practices
With the advancement of nozzle technologies, there is a need for municipalities to get everyone on the same page about the proper techniques for cleaning sewer lines.
“What surprises even experienced sewer and storm professionals is the science that is behind the best practices,” said Story. “What we teach is based on understanding fluid dynamics. We look at the horsepower of your truck that drives the water pump for a rate of volume at a particular PSI level. We factor in the efficiency of the nozzle. What we want to get to is how to run the truck at a lot lower RPM and PSI that will clean the line easier, better and more efficiently.”
“We can show operators how to use less water, less fuel and cause less wear and tear. Bottom-line, it’s about how to get more work done while using fewer resources. And of course, this reduces the risk of the worst case scenario of blowing up toilets in people’s homes,” adds Story.