
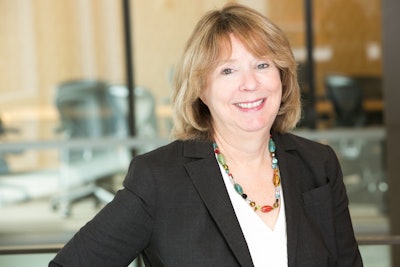
In an era when labor is of prime concern to all industries, it is especially critical for the manufacturing world due to scarcity of skills, increasing cost of goods and needed efficiencies in the overall process. The industry is looking for additional ways to optimize and save in the cost of the hourly labor spend.
The standard process for identifying savings has been to look at reducing the workforce in times of decreased capacity, as well as adjusting shifts or reducing schedules. However, there are other ways of realizing cost savings that may not have been utilized by assessing other data or processes, which may not result in a reduction in headcount.
In working with organizations to uncover those potential cost savings, there are three areas within the process that are not normally considered, but based on many assessments may result in both hard and soft dollar returns of between .05-2 percent of the hourly spend. These areas are:
- Workforce Management Systems: Many manufacturers use one of the leading Time and Attendance systems, with functionalities that provide modules the address many business goals. These systems are often implemented with a ROI goal, but rarely utilized to their full potential to track metrics, effective scheduling on the plant floor, overtime utilization or something as simple as call-in pay. While assessing the current state of the system, the findings can be:
- Paying for licenses for functionality that has never been used or configured
- Modules that can identify scheduling opportunities based on seniority, hours worked or skill set
- Configuration that is out of date or not utilized properly based on pay policies or regulatory compliance
- Using the Date You Already Have: While inconsistency or not using the full power of the plants Time system can result in immediate savings, there are also hidden potential in the data from those systems, as well as the Payroll or HR System. By doing an analysis of the data, including overtime hours, missed lunches, rounding or scheduling then reviewing the policies that drove the decisions behind the data, clear patterns can become apparent in configuration updates or process realignment. For example, after analysis that was completed last year for a large consumer product manufacturer that one plant (out of nine) had significant overtime due to only the most senior workers being trained in the areas needing overtime. By cross-training or at times hiring, the overtime spend could be significantly reduced.
- Who is Managing the Overall Process? In addition, if a HR, Payroll or Time system is not consistently managed, the plants may be independently managing the process, training and how potential enhancements requests are handled and prioritized. By having a core team, or a Center of Excellence modeI, managing all elements allows for the engagement of the right teams, including HR, Finance, IT and, most importantly, Operations to give feedback and prioritize what is important to the overall organization. This model can also manage and create training and communications that is standard and repeatable, which can help the data to be consistent and accurate, which can affect the downstream processes including employee paychecks and financial reporting.
While the assessment of these three areas seem straightforward, most manufacturing organizations have not taken the steps to engage the right resources or tools that can give them the insights to their data. In the previously mentioned assessment of nine plants, by reviewing the processes, systems, policies and governance estimated savings was between $17-22 million. Some of those savings were over a period of time, while others could be realized quickly by adjusting specific parameters within time system or tightening processes where supervisors or employees may not be utilizing the system properly. Only by getting to the data and focusing on the impacts from the processes and policies, can trends and potential savings be identified.
The assessment of these areas can also open the dialogue with the Operations leadership about what is important in their plants. Whether that is lack of the right talent, extensive overtime or manual processes that result in lack of accuracy or administrative overload, engaging the plants in the path forward gives them a voice in the overall process, which is important for acceptance and adherence. The ability to get buy-in from the plant leadership is key to the success of any initiative, especially one that can produce efficiencies and savings.
In this era where all options are being evaluated to enable the manufacturing world to produce better products in more efficient and cost-effective manner, and still keeping the workforce engaged, it is important to look at alternatives to the standard reduction in workforce model. By thinking differently and looking at what is already being used and how it is being used, there are opportunities to realize savings.
Data. Processes. Policies. Technology. You just need to know where to look.
Jenine Bogrand is a Manufacturing Sector Leader for LaborWise, Deloitte Consulting LLP.