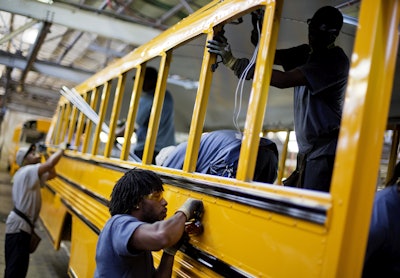
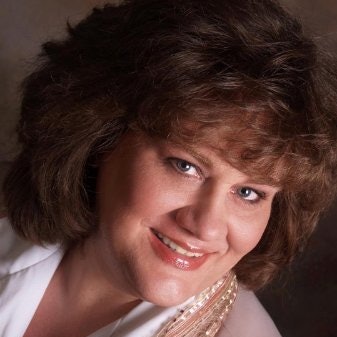
I keep hearing that there is a "skills gap" in the manufacturing industry. Really? Are we sure about that? Could it be that:
People don’t qualify for the jobs for reasons other than a “skills gap?”
People don’t know the jobs exist?
People don’t want the jobs?
Before we talk about this supposed “skills gap” can we do a little investigating to find out what is really going on? Because if there really is a “skills gap” I, like everyone else, want to understand what industry specific skills are missing in our country and fix that. However, in order to fix it, we need to determine what we mean by a “skills gap” (if in fact there is one), why it is happening and if a skills gap truly exists, what are the specific steps needed to address the problem discovered.
But let's back up for a minute and talk about what we mean when we say "skills gap." A "skills gap" indicates that a specific skill or set of skills that is needed in a particular industry (and usually needed to be performed by a specific occupation within that industry) is/are for some reason not available from the local workforce's set of abilities.
Ok...but before we start training people to acquire those skills, we need to determine if there may be other issues keeping the manufacturing industry from getting the employees they need.
Therefore, my first question is, "Are manufacturing jobs indeed going unfilled?" Now that, in and of itself is a question mired with additional questions because"manufacturing" can represent everything from potato chip manufacturing to computer chip manufacturing...so we first need to start grouping these manufacturing companies in some sort of logical way so that we can begin to compare apples to apples (skills sets with skills sets).
Next, looking at these categories of manufacturers we have created for our region, we need to determine if the jobs in all of the categories of employers in manufacturing are going unfilled, or just a few of the categories (just high tech, just low tech, etc)? And what are the specific skills represented in these jobs that are going unfilled?
In order to figure out what specific skills are needed that are unable to be obtained by employers, we need to see a list of all job postings that were not able to be filled in a particular region in manufacturing and what, if anything is similar about those job postings skills requirements? But while we're at it, lets also look at what are the hours people are being asked to work in these job postings, what are the wages people are being paid to perform these jobs, etc., because this supposed “skills gap” may be being assumed when in fact it is being caused by other issues. So let's really examine these unfilled job postings for what they may have in common. This would begin to provide some clues, but it certainly is not a definitive answer as to WHY the jobs are not being filled.
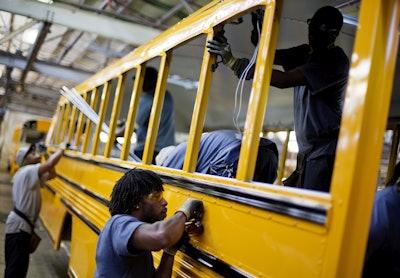
Once we indeed determine which specific types of jobs are going unfilled, we need to figure out why the jobs are going unfilled, and there are really just two main reasons for jobs going unfilled:
Scenario 1) if the applications coming in for the job posting in manufacturing are unqualified? (and what exactly makes them “unqualified?”)
Scenario 2) If there simply not enough people applying for the jobs?
So first, let’s take scenario 1…if the applications coming in are unqualified, WHY are they unqualified?
Possibility #1) There is a "personnel reason" for applicants not qualifying (something other than their industry specific skills) that makes them ineligible for the position. For example,
- Do they not have the number of years of experience to qualify them to do the job?
- Do they have bad references?
- Can they pass the background check or credit check?
- Is their resume or application being presented in a sloppy manner?
Possibility #2) They cannot pass the interview stage. For example:
- They cannot pass a required drug screening?
- They do not communicate effectively orally?
- They do not dress/act appropriately at the interview?
Possibility #3) They do not have the “industry specific skills” needed to do the job?
Now, if this really is the only issue keeping them from getting the job, than that would be a “skills gap.” So if that skills gap does exist, WHY?
- Does the public know how to acquire the skills for this particular job?
- Are there enough people needed to do this job to warrant a training course be provided?
- Do people in the region who would want to do this work, have the basic academic skills needed to acquire the industry specific skills needed to do the job?
- Is more training needed? (are there already training programs but they are at capacity?)
- Is effective (and industry accepted) online training for these skills available? If so, who is providing that training? Are these online training opportunities being accessed? Are people taking these courses able to complete them?
- What certifications or industry credentials are required?
- Are people failing out of the training programs?
- Are the training programs in step with what the industry actually needs people capable of doing?
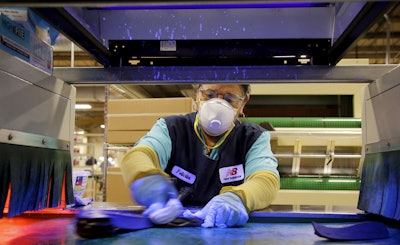
Now let’s take a look at scenario #2, which is that there are not enough people applying for the jobs.
1) Is this a demographics situation?
- Are there simply are not enough people in the region to do the jobs that are being offered?
- Does the region need to improve/grow its infrastructure to support a talent attraction effort to bring in workers for the industries that need workers and are unable to acquire the workforce needed from local pools of labor?
2) If people in the local region are not aware of the job opportunities, why?
- Are employers/educators/associations addressing career awareness in manufacturing? How is manufacturing education integrated:K-12, voc schools, Colleges, Private schools,Online? Are job centers providing any workshops to introduce manufacturing career awareness? Are manufacturing employers doing any occupational awareness?
3) If they don't want the jobs, why?
- Are wages being offered reasonable for the local economic climate?
- What jobs are people taking (and why) instead of these manufacturing jobs?
- Are jobseekers looking for more convenient hours?
- They want more convenient locations to work in?
- They want a cleaner work environment?
- Is there room for career advancement?
- Does the manufacturer have a bad reputation in some way that makes people avoid working there? (environmental issues, "mean" bosses," unreasonable expectations of workers?)
- Is the employer importing people to work in their company to keep wages artificially suppressed?
Here is my point…I don’t think we really know if we have a “skills gap.”
Show me a region that has done an exhaustive study that effectively answers all of the questions above, including understanding the demographics of the region, a wage analysis of the region, an analysis of job postings, interviewing HR managers, educators/trainers, CEO’s and jobseekers…and I will show you a region that either no longer has a “skills gap” or is at the very least, well on their way to not having a skills gap.
You cannot develop strategies for solving perceived problems. You must understand deeply what the problems actually are and then look for the right people to come to the table to work together on fixing the issues.
If any of you would like help with conducting an in-depth study in your region that gets to the truth about why you have what people may be calling a “skills gap,” give me a call. I can help.