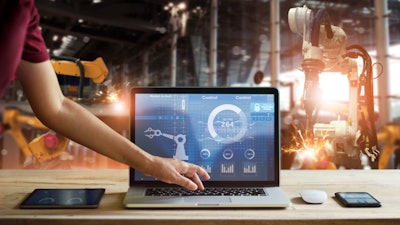
In the modern industrial landscape, the convergence of Information Technology (IT) and Operational Technology (OT) has become increasingly crucial for organizations across a variety of sectors. IT encompasses the systems, networks and software responsible for data management and analysis, while OT deals with the hardware and software used to monitor and control physical processes.
The amount of data available is exploding due to the rapid development of 5G wireless, OPC and other system-wide IP standards, which are driving an increase in the number of devices installed and connected at facilities. However, the lack of seamless connectivity between IT and OT systems poses significant challenges, especially in storing, analyzing and integrating data.
Effective data analysis is essential to make business decisions, so how can this be possible? For decades, decision-makers have had to work with insufficient information to make decisions on operations, supply chains and reducing costs or increasing efficiency. Though utilizing the best information available to them, it has historically been difficult to understand all the variables affecting complex operations.
Modern systems have the capability to share data widely and securely, facilitating better decision-making and live insight into processes. Imagine an opportunity for a large contract, but the customer needs untried materials or brings new product requirements. The plant needs a fast changeover to meet these needs while maintaining maximum product quality. Can you make this possible for your customer, or would an ad-hoc change to your processes result in excess manual effort, higher costs and reduced efficiency?
Understanding the Problem
Poor connectivity between IT and OT systems makes storing and retrieving data difficult. OT systems generate vast amounts of real-time data, including sensor readings, machine logs and operational metrics. This data is often isolated within OT silos, hindering the establishment of centralized data repositories. Lack of direct data-sharing between IT and OT can also lead to data duplication, inconsistencies or even potential data loss, when leveraging ineffective storage processes.
Limited connectivity between IT and OT also presents significant obstacles when analyzing data. When integrated with IT systems, OT data can provide valuable insights that aid in decision-making, process optimization and predictive maintenance. However, the disjointed nature of these systems hampers the seamless flow of information, making it challenging to extract meaningful patterns or correlations. In addition, analyzing data in silos limits the potential for cross-functional analysis, hindering organizations from understanding their operations holistically without laborious and error-prone database ETL processes.
Benefits of Tight Data Integration
One benefit of integrating IT and OT is achieving maximum traceability throughout the production chain. Traceability ensures tracking and verification of the history, location and usage of components, materials and products. As a result, organizations can achieve end-to-end visibility, enabling them to trace the origin of raw materials, monitor quality at every stage, and improve compliance with regulatory requirements by having OT data available for broad analysis at a business level. Conversely, the lack of integration limits traceability efforts, compromising product quality, safety and customer satisfaction.
Integrating IT and OT also promotes flexibility in industrial processes, allowing organizations to adapt to changing market dynamics and optimize operations. By sharing data seamlessly, businesses can gain real-time insights into production metrics, machine performance and resource utilization. This data facilitates agile decision-making, quick response to issues and the ability to fine-tune processes for improved efficiency. Without integration, organizations face limited flexibility and insufficient information to make educated decisions, making it challenging to implement responsive strategies and define the data and communication technologies for efficient engineering, flexibility and scalability.
Integrating the disparate data silos formed by IT and OT systems also offers substantial sustainability benefits. By combining data from various sources, organizations can identify energy inefficiencies, reduce waste and optimize resource consumption. For instance, by analyzing data from OT sensors and IT systems, organizations can pinpoint energy-intensive processes and implement measures to enhance energy efficiency.
Moreover, integrated data enables accurate carbon footprint calculations, aiding sustainability reporting and compliance, and data, aggregation, contextualization and transparency across all layers from the OT shopfloor to the IT top floor, which allows both IT and OT users to understand correlations.
The poor connectivity between IT and OT systems poses significant challenges for organizations in storing and analyzing data. By bridging this gap, businesses can achieve maximum traceability, flexibility and sustainability and make confident decisions in real-time to identify and eliminate bottlenecks in production. Increased transparency provides an overview of all relevant data and allows for the seamless flow of information enabling cross-functional analysis and enhancing decision-making.
The integration of IT and OT systems is crucial for organizations striving to gain a competitive edge, optimize processes, and unlock the full potential of their data resources in today's interconnected world.
Luis Narvaez is the U.S. Product Manager for SIMATIC PLCs and Industrial Security at Siemens.
Chris Liu is the Product Manager for Siemens Industrial IoT technology Industrial Edge for the U.S.