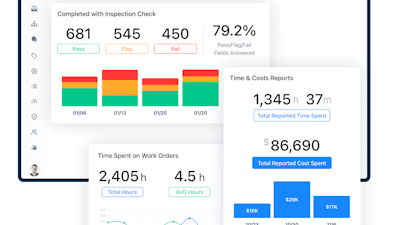
As a former manufacturing director of a large facility, I was tasked with โimplementing a digital transformationโ - a vague request with a checkbox next to it. In my case, this meant using smart sensors to collect more data. Our goal was to improve performance and increase capacity.
However, with disconnected systems and teams, it was difficult to know where to start. I needed more information: why by how much, where are the bottlenecks, how many sensors, whereโs the value mapping, how do we engage our teams, what is the proposed project ROI?
The โwhyโ and the โwhatโ of digital transformation can be challenging when piecing together insights for digital strategies. Itโs even more complicated when certain functions, like maintenance, are disconnected from production health KPIs when ingesting and accessing relevant data.
Yes, adopting more modern, connected solutions can and does help address asset performance and capacity challengesโbut only if those solutions are designed with the end-user in mind and the deployment strategy considers their journey to adoption.
Alarmingly, nearly 60% of IoT projects fail. A common pitfall is the absence of a project charter that is understandable and actionable by the teams tasked with optimizing and maintaining the equipment. Maintenance technicians, for instance, are typically on the plant floor, working offline on manual inspections that are later keyed into work orders; their current workflows are a far stretch from the capabilities modern autonomous Computerized Maintenance Management Systems (CMMS) deploy, with data-driven workflows, in-app two-way messaging tools, pre-built integrations, visual instructions, and more.
A survey of 400 technology executives found that nearly half have yet to see any improvement in performance or profitability from their digital investments. This disconnect highlights a crucial truth: successful digital transformation hinges on clear communication and user adoption.
IIoT frontline view - Enabling frontline workforces to visualize your most important IIoT sensors on mobile devices amplifies their value.MaintainX
Setting Your Team Up for Success
To achieve the desired outcomes of a digital maintenance strategyโwhether higher production capacity or extended equipment lifespanโmanufacturers must effectively marry IIoT technologies and human floor-level insights. This starts with creating a clear roadmap that considers the machines and technologies and the people operating and maintaining them. For instance, deploying a mobile-first CMMS with smart sensors and AI analytics can make predictive maintenance a reality. However, this is only possible if the team buys into establishing a unified technology stack from cloud to edge with specific instructions that allow them to execute easily and efficiently.
How to Get Started
Outline a project charter: Every IIoT initiative should start with creating a project charter, outlining the current state, desired state, architecture requirements, timing, scopeโand, importantly, the โwhyโ and โwhoโ behind the โwhatโ so the team can align on critical objectives and responsibilities. Key questions to address in the charter include:
- What are the specific goals of this IIoT implementation based on your business case (e.g., increased production capacity, reduced downtime, improved quality)?
- How will new alerts and data points be integrated and prioritized into existing workflows?
- Which meters make sense to continue with manual charted readings?
- How will the IIoT implementation impact existing maintenance tasks?
Answering these questions upfront will ensure a smoother transition and maximize the chances of successful adoption.
Communicate the plan: Once your project charter is established and your cross-functional team is assembled, itโs crucial to ensure everyone understands not just the technology but also the rationale behind the changes. Teams often receive technical training on the device but may lack guidance on managing increased data flows or adapting to existing workflows. Transparent communication and ongoing support are essential to empower workers to embrace and utilize the new tools effectively.
Identify the most critical assets: Asset health is the ideal starting point for those beginning their IX journey. Instead of a mass deployment of IIoT sensors, prioritize your most important equipment. Work with stakeholders to understand how machine data is currently collected and visualized. This collaborative approach ensures the team knows what to monitor and measure, allowing for a smoother transition and better control over asset and production performance. Every enterprise will be different. โMeasure what mattersโ should be your guiding principle.
Establish one-point lessons: Seek out CMMS solutions with built-in visualization, such as digitized instructions and checklists with one-point lessons (OPLs). These OPLs simplify complex procedures by providing step-by-step visual guides accessible on mobile devices. This streamlined approach empowers technicians to complete tasks quickly and accurately, improving efficiency and reducing error.
Introduce gamification: A workforce survey found that 89% of employees would be more productive if their work were gamified. Consider a maintenance team that adopts a mobile-first CMMS to collect machine data and log every task associated with work orders; they can use it to track their inspections and procedures via scorecards to analyze their performance and progress. Teams can compete across locations, setting achievable goals for completed work orders, parts inventory accuracy, or improved mean time to repair (MTTR). Start by allowing the team to familiarize themselves with the tool, then gradually introduce benchmarks to keep the momentum going. Celebrating early wins and applying the PDCA improvement cycle helps establish ownership and accountability.
Succeed, then scale: A โflip the switchโ approach to IIoT adoption is key to avoiding overwhelming your team. Start small, with the team agreeing on critical assets and ensuring they are comfortable with the new tools and processes before expanding. This allows you to identify and address any issues early on, providing a smoother, more successful rollout across locations. Ultimately, small wins will build confidence and pave the way for larger-scale, value-focused success.
When digital transformation strategies are properly deployed and designed with empowered frontline teams in mind, executives will see performance and ROI increases. Itโs already happening for someโusing digital tools to unlock higher asset performance and a more efficient workforce has increased profitability by 4 to 10% in some organizations.
Following the proper steps will get you there. The best path forward is to do your research, ask questions, consider your technicians, consult with groups that have seen success, and lean on your technology partners for guidance along the way.
For more information, visit www.getmaintainx.com.