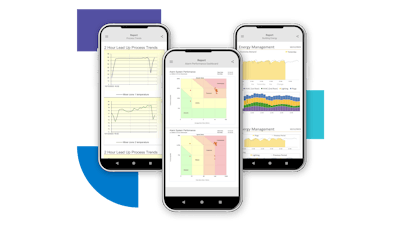
Digital transformation, IIoT and Industry 4.0 are critical to operations and can enable smarter decision-making across manufacturing and supply chains. To remain competitive, particularly in light of worker shortages, IIoT and complementary technology must be embraced.
This increased connectivity and information modeling empower decision-makers, enable faster response times and drive increased productivity.
Across all industrial sectors, nearly 31% of production processes and equipment and 30% of non-production processes and equipment have some kind of smart device embedded in them. McKinsey estimates that IIoT will have a total economic impact of as much as $11.1 trillion per year and will be the biggest source of value of all disruptive technologies.
Of these settings, factories and other process-driven production environments such as hospitals and farms, are likely to reap the greatest benefits from the adoption of IoT systems.
Reports created by third-party software provide a visualization of historized process information and correlate related process variables, compute metrics on that data and visually graph such data for easier pattern and anomaly detection.SmartSights
Aging Infrastructure and Modern Demands
While the promises of Industry 4.0 are powerful, many manufacturers face an implementation challenge: an abundance of legacy equipment that can’t integrate with new smart technology.
According to a study from the Manufacturing Leadership Council, over 70% of manufacturing equipment in North America is more than 20 years old. The good news? Digital transformation doesn’t require wholesale replacement of production infrastructure.
Through strategic integration of digital capabilities into legacy systems, manufacturers can achieve remarkable improvements without massive capital expenditure. In this way, digital transformation becomes an incremental journey, not a binary leap, and even the oldest machines can contribute to modern, data-driven manufacturing.
Operations and Technology
The ultimate goal of adopting modern systems is to have a wholly efficient, maybe even an autonomous process that cuts out excess fat, ballooning costs and wasteful operations. Focus should be on end-to-end process improvement, which will, in turn, help shape collaboration within the organization.
That means investing in training and education, process automation, related hardware and new tools or software. Continuous operational improvement starts with capturing data from machine assets. This data provides immediate insights for both people and systems, enabling them to make better, faster decisions and drive automation.
Characterized by increasing automation and the employment of smart machines and smart factories, informed data helps to produce goods more productively across the value chain. By collecting additional data from the factory floor and combining that with other enterprise operational data, a smart factory can achieve information transparency and better decisions.
Accurate, real-time production data is pivotal to shop floor operations and the effective operation of each machine asset.
Once real-time process information is gathered, the next logical step is to define conditions of concern on those process variables. For example, ‘Is an oven too hot or a motor spinning too slowly?’ ‘Is a tank nearing empty or a pressure too high?’ ‘Are there issues with the centrifugal pumps drawing liquid?’
SCADA systems provide for such conditions to be defined and tracked, monitoring process variables and surfacing active conditions to HMI. These condition-based events and alarms add another level to optimizing the process: they allow greater situational awareness for plant operators by calling attention to irregularities and suboptimalities.
Real-time process variables and alarm conditions can then be captured over time and calculations can be performed to improve planning and offer solutions to detect patterns in the data.
Data is Key to Increasing Efficiency
While accurate, real-time and historical data is pivotal to operations, harnessing this data effectively requires advanced technology and analytical capabilities. Vast amounts of data are collected for industry reporting, predictive maintenance and safety enhancements, for example, but manufacturers may be challenged to effectively manage and analyze the data.
While monitoring and alarms can improve system efficiency, they don’t automate the labor-intensive reporting process or provide much-need analytics that extract raw or summary values over a discrete time period.
Automated third-party reporting software, however, tracks all areas in a production facility. The finished reports are then distributed directly to preferred destinations, which streamlines the decision-making process and enhances operational efficiency.
The ability to harness this data effectively can lead to smarter decision-making, improved processes and a competitive edge. Analyzing historical data allows operations management to identify patterns, trends and anomalies that may otherwise go unnoticed.
Historical data analytics can help companies transition from reactive to proactive planning and keep planning aligned with operations. As the data is collected it is summarized as key metrics and the final output is published into a formatted document accepted by regulatory agencies.
Integrating additional software accelerates digital transformation with advanced data collection for overall equipment effectiveness (OEE) and manufacturing execution systems (MES), enabling plant personnel to have valuable insights into the operations and helping them make better and more informed decisions.
By deploying third-party advanced software, manufacturing plants can accelerate and drive OEE uplift, avoid problems before they occur and reduce engineering time by up to 70%. Additionally, for a $1 billion company every 1% improvement in OEE, like integrating advanced software that reduces equipment downtime, is worth approximately $7 million annually, further lessening costs and improving operational efficiencies.
Third party analytics software provides advanced data collection for OEE and MES solutions, seamlessly integrating with ERP, CMS, or production systems.SmartSights
The Future Includes IIoT
Rapid globalization, technological advancements, changing consumer preferences and evolving government policies are reshaping industries. Trying to meet these challenges with manually intensive processes and outdated technology is difficult.
However, by adopting IIoT and leveraging advanced technology such as real-time data collection and automated processes, manufacturing operations can increase productivity and efficiency, reduce costs and help manufacturers avoid problems before they occur.
Prioritizing operational excellence through plant efficiencies not only fosters growth but also positions organizations for continued success in an ever-evolving business landscape.
Digital transformation isn’t a single event, it’s a continuous journey. And those who embrace it thoughtfully, starting with the systems they already have, will be best positioned to lead in an increasingly dynamic industrial landscape.
---
Cody P. Bann is the vice president of engineering at Texas-based SmartSights and may be reached at [email protected]. David Nolan is the industry solutions manager at Austin, TX-based SmartSights and may be reached at [email protected].
SmartSights is a provider of data-driven analytics, reports and notifications, serving the industrial sector. The company helps users to monitor service levels and respond to incidents from the plant floor, central office or remote locations. The company designs its tools to enhance team productivity, boost efficiency and integrate operational visibility with actionable insights.