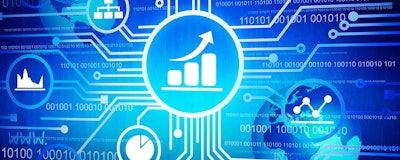
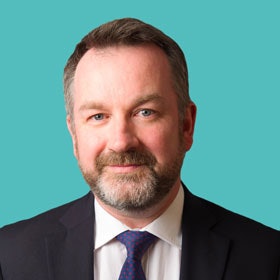
Throughout history, the manufacturing industry has been at the forefront of innovation. Dramatic improvements in high-performance computing (HPC) including machine learning, fluid dynamics and advanced material design have formed the latest nexus between manufacturing and innovation, translating into phenomenal new technologies and even serving as the foundation for entirely new industries.
Intersect360 Research reported in November 2017, that HPC is a strong, growing segment of enterprise computing, forecasted to grow to nearly $44 billion by the year 2021. As the pace of development surges forward and use of computational aided intelligence in manufacturing begins to take shape, manufacturers must now consider new approaches to address computing performance to accelerate the innovation cycle and evolve how design, testing and production gets done.
With the integration of business and technical processes, manufacturing value chains have become smarter and now encompass all stages of the product lifecycle – from the idea and development to production, testing, use, maintenance and recycling. This has resulted in explosive growth in computing power and improved computational frameworks which together have propelled HPC-enabled applications into a competitive advantage. Take for example the automotive manufacturing industry, where HPC has been eliminating the need for traditional assets and procedures like the crash test dummy and the wind tunnel throughout the last decade. Today’s automakers rely on HPC for advanced crash test simulations, such as LS-DYNA that uses finite element analysis. HPC has also radically improved the way products are manufactured at commercial scale. HPC-enabled modeling and testing allows researchers to virtually experiment with a new material without the need for a physical prototype, allowing manufacturers to cut costs in the development cycle and improve design. HPC eliminates risk in the design phase, enables manufacturers to run simulations needed for product safety and compliance, as well as security checks and testing needed to bring products to market.
Throughout the product lifecycle, requirements for HPC can widely differ often growing exponentially as manufacturers see the benefits that HPC applications bring to the overall business. The positive impact of HPC on manufacturing companies is confirmed by numerous studies, including one by market research firm IDC, which found that 97 percent of companies that adopted HPC said they could no longer compete or survive without it. Despite these critical business benefits, why have many manufacturers not yet adopted HPC?
There are several reasons. Traditional data center design is built to support the demands of every application in the corporate IT stack. While this approach to compute may seem like the obvious choice, this one-size-fits-all methodology prevents the manufacturer from realizing the true benefits that HPC offers. HPC has unique specifications that need advanced infrastructure and hardware, power and cooling resources. For many, the cost for added infrastructure purpose-built for the demands of HPC applications have simply outstripped the standard capabilities of an enterprise-class data center. In addition, the depth, experience and skill of the technical team needed to get the most out of HPC workloads – from analysis to application – is another element required for successful HPC implementation.
To address issues such as these, a number of large scale manufacturers decide to collocate their hardware to specialized data centers that are specifically suited to handle the high intensity compute of HPC. Data centers offering this specialization are few and far between, and when considering them, key selection criteria include the availability of low-cost power, and the climate, which if cool enough, can enable free, ambient air cooling of the HPC hardware — cutting out almost 40 percent of the cost of hosting. With this approach, as you would expect, data center location and site selection becomes key.
Forward-thinking German manufacturers — BMW and Volkswagen took this approach when reviewing the location of their HPC workloads. Back in 2012, BMW moved a number of their HPC clusters for its iSeries electric vehicles to Iceland, and was able to run crash test simulations and fluid dynamics modeling while significantly lowering its HPC power costs by more than 80 percent compared to Germany. Iceland offers 100 percent geothermal and hydro-electric sources of power, plus ambient air cooling due to the country’s temperate climate, allowing advanced manufacturers like BMW to significantly reduce not only the cost, but also the carbon footprint of its HPC deployment. Volkswagen also moved more than 1MW of it HPC applications to Iceland and they are enjoying similar benefits by collocating their infrastructure to Iceland.
While collocation to specialized low-cost, cool locations was maybe the first step towards reducing HPC operating costs, the cloud is now also becoming an increasingly viable option, even for intensive compute such as that enabled by HPC platforms. A cloud-based HPC product and especially those offering an on-demand service, allows manufacturers massive flexibility for their workloads, enabling them to augment their existing deployments (be these in-house, collocated or cloud reserved) with rapidly provisioned HPC power, via the Cloud, when needed. This also enables a move from CAPEX to OPEX and provides manufacturers with compute stores for product design and development without the balance sheet burden.
Nick Dale is Senior Director at Verne Global.