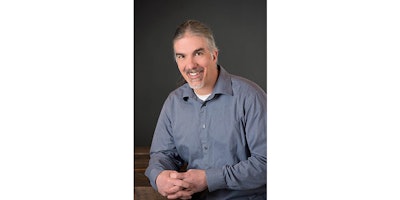
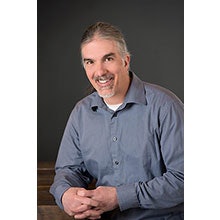
Computerized maintenance management systems (CMMS) are proven to reduce downtime, save on asset and facilities repairs and optimize the efficiency of asset tracking in a variety of industries, from hospitality to pharmaceuticals. Food manufacturing is no exception.
With so many opportunities to save money, control costs and streamline reporting and repairs, one would think CMMS adoption would be a no-brainer. However, decision makers are sometimes content with current systems and unwilling to swallow any upfront costs of new maintenance systems, especially if they don’t see their systems as broken. Their thoughts: If it’s fine as is, why fix it?
Unfortunately, this line of thinking can be incredibly damaging to day-to-day operations — and the bottom line. So how do maintenance managers justify a CMMS to their CFOs? It could be as simple as showing them the numbers.
CMMS can pay for itself in a matter of months
It’s true that robust CMMS, like most enterprise software, has upfront costs for implementation. Besides the cost of software, businesses must also spend time and resources training employees on the new technology and integrating the solution with other systems, such as HR, Active Directory and Procurement.
Once up and running, however, CMMS can work to drastically reduce the costs associated with downtime and maintenance repair. Some firms lose out on thousands and even millions of dollars a year on equipment and systems failure. These losses are likely due in part to reactive maintenance strategies that only address issues after machines have failed. This entails unforeseen downtime and requires repair technicians to act without proper preparation, often in chaotic, rushed environments.
Because modern CMMS serves as the main hub surrounding preventive maintenance scheduling, parts availability, staff certification documentation, safety notes, inspection logs and more, technicians and coordinators can often schedule downtime in advance for preventive measures. This allows businesses to address problem areas before they become an especially costly issue requiring specialized labor, additional parts or the replacement of the asset entirely. With a well-designed CMMS, repair technicians can also work with operations managers to minimize costs by scheduling downtime during off-peak or otherwise more convenient periods.
Here’s how CMMS can save money
Let’s consider a machine that processes meat products. Without a preventive or total productive maintenance strategy in place, the machine might break down unexpectedly during peak operating hours. This requires staff to halt production and alert maintenance professionals, who must then assess damage on the fly, before making potentially difficult and time-consuming repairs — and that’s assuming necessary parts are readily available. Additionally, health risks from contaminated products or worker accidents might complicate the issue further and involve regulatory agencies, such as the FDA or OSHA. The ability for your organization to quickly respond to log inquiries, inspection reports and other documentation via CMMS could mean the difference between penalties and business as usual.
Imagine another scenario, in which employees are using a Total Productive Maintenance (TPM) and predictive maintenance (PdM) strategy supported by CMMS. An operations professional would have spotted issues in the equipment during day-to-day operations thanks to their involvement with a CMMS that receives machine events, like spikes in vibration or temperature. A repair technician could plan ahead to address the event before the machine actually shuts down while running, working with operations managers to plan the best time to work with minimal impact to productivity. Since the technician will have time to prepare the right tools and processes planned to attend to the machine, he or she will be more efficient and likely more successful in addressing the issue.
Without predictive maintenance, there is greater risk of failure
Downtime is unavoidable within the food manufacturing industry. With so much wear and tear on complex moving parts, equipment repairs are inevitable. What is not necessarily inevitable is being completely unprepared for the breakdown of equipment during production. In many cases, machines are run to the ground with issues addressed only once they have broken down, and in what could be prime hours of productivity. While malfunctions may be begrudgingly seen as a fact of life in the food manufacturing industry, they are not necessarily inevitable — and that should ring alarm bells for any CFO.
While it may sound cliche, time is, in fact, money. By not re-evaluating existing systems against the functionality inherent in modern CMMS, such as TPM, PdM and safety management, businesses are missing the opportunity to save time, increase communication and grow production capabilities — the real driver of profit. That alone should be enough to convince a CFO with an eye on the bottom line.