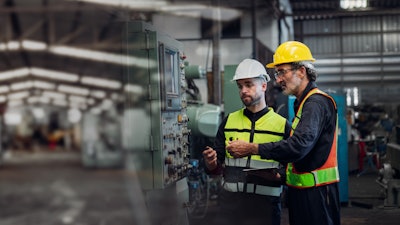
Factories carefully track materials, machines and products through the production process—but operator identity is often a missing link for optimization. Operator authentication at the machine level allows managers to track who operates each machine, at what times, and for what purposes. Understanding “who” can help factories resolve production problems, optimize the workforce, and drive productivity and quality improvements.
The Missing “Who” in Industry 4.0
With Industry 4.0 and the “Industrial Internet of Things” (IIoT), the manufacturing industry has embraced tracking machine usage, raw materials, parts, finished products and much more, giving them a highly granular view of the “what,” “when,” “where,” “how,” and “how much” of every production process.
What is missing from the equation is often “who.” Many factories still use offline operator logs or simple spreadsheets to track operator activities—if they are tracked at all. Outside of basic time and attendance data, there may be little tracking of exactly what individual workers are doing over the course of a shift.
A robust machine authentication system enables tracking of operator identity—the “who” in production processes—along with all other aspects of production. Adding this missing link into production data enables new forms of process and workforce optimization.
Many production facilities do not authenticate individual users at the machine level or even at the line level. Physical keys or fobs or a shared password or PIN may be used to unlock access to machine controls. These methods offer only marginal protection against unauthorized machine access and provide no visibility into which operator was at a machine at any given moment in time. To get the operator data needed for workforce tracking and optimization, plants must be able to link a unique operator identity to each machine each time it is used.
The Value of Knowing “Who”
User authentication at the machine level helps manufacturing plants improve security, safety and data-driven decision-making. Using a unique operator identity for log-in at the machine level provides multiple benefits for manufacturers.
- Improved security: Shared access control methods (e.g., physical keys and fobs, shared PIN numbers) are not secure—anyone might get their hands on them to access machines they are not authorized to use. A unique operator identity provides higher security and accountability.
- Safety and compliance: A unique operator identity can be linked to training and credentialling systems, ensuring that only trained, authorized operators can access machines.
- Workforce tracking and productivity: Having employees sign into each machine with a unique operator identity provides better visibility into how workers use their time and how productive they are in each shift.
- Product quality tracking and troubleshooting: Linking operator identity to production machinery can help supervisors or process engineers get to the bottom of production and product quality problems. For example, if a product quality issue is consistently linked to specific operators, supervisors can provide additional training or work with employees to troubleshoot the problem.
Understanding operator identity can be especially important in high mix/low volume production environments, such as the aerospace parts industry. When plants are building a handful of customized, high-value parts, it is especially critical to solve any product variation issues quickly. It is also important to ensure that all machine operators are trained and authorized for the machines, processes and design files that will be utilized.
How Operator Identity Drives Workforce Optimization
Machine authentication also enables workforce optimization. Operator identity is another data point that can be used to optimize production processes. There are several ways that operator data can be used to drive continuous improvement for factories.
- Labor cost tracking: Tracking who is using which machines and for how long provides more granular information about labor costs for improved cost accounting. What are the true labor costs for different products, based on machine time and operator hourly wage? Can costs be lowered by reconfiguring the workforce to shift some lower-cost (less skilled) workers to take on tasks currently performed by workers over-skilled for a particular job?
- Workforce utilization and scheduling: Machine authentication enables better monitoring of how employees use time across each shift. It also allows supervisors to analyze workforce utilization and make effective scheduling decisions. Are some workers idle at times because they don’t have the training needed to operate available machines? Are some machines idle at times because there are no workers available with the needed skills or credentials? Are production tasks spread evenly and fairly across the workforce?
- Training and hiring decisions: Supervisors can use operator information to decide what type of training is needed and by whom. In addition to providing targeted training to resolve production problems, managers can look at the training needs of the workforce as a whole. Are more operators with specific skill sets or credentials needed to maximize production capacity? Can skill gaps be met by up-skilling existing workers, or are new hires needed with particular skill sets?
- Performance improvement. Operator identity tracking allows supervisors to match production outcomes to specific operators. If there are variations in output, quality or speed between operators, supervisors can use that information to identify best practices, set up mentoring relationships between workers, or identify workers needing performance improvement or ready for advancement. Data can also be used to match workers with the machines and tasks they do best.
Implementing Operator Identity Tracking and Workforce Optimization
“Workforce tracking” is not always universally embraced by the workforce being tracked. Implementing new systems to track operator identity and performance data requires a thoughtful, positive approach to gain worker buy-in.
- Keep it positive: Workforce tracking should not be used punitively but rather to improve outcomes for both individual workers and the business.
- Explain the benefits: Ensure line workers understand that operator tracking benefits them, not just their bosses. Having accurate user data can take bias out of the system and provide objective, concrete data points for performance measurement. Workers benefit by having clear metrics for performance improvement, proof of exemplary performance, and data-driven training recommendations for up-skilling.
- Make it easy: Don’t give workers another set of passwords to remember or a second ID badge to carry. The simplest way to implement machine authentication is to use universal RFID readers that work with the ID badges they already carry for building entry and time-and-attendance.
- Communicate clearly: A phased, deliberate roll-out plan with clear communication and training can go a long way toward increasing acceptance of operator identity tracking.
With the right approach, workforce tracking can provide substantial benefits not only for supervisors and managers but also for individuals. Tracking is also the first step to workforce optimization: matching worker skill sets and schedules to the needs of the organization and driving continual improvement at the individual, team and business levels. It all starts with knowing “who.”
Mike Harris serves as the head of business development for ELATEC Inc., which is in Palm City, Florida. In his position, Mike is responsible for connecting ELATEC market needs and its internal teams, including Product Development, Engineering, and Sales. He has a Master of Science degree in Physics from Southern Methodist University and held global product management positions at Elo Touch Solutions and Ocular LCD Inc prior to joining ELATEC.