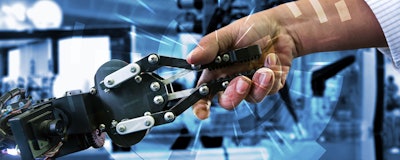
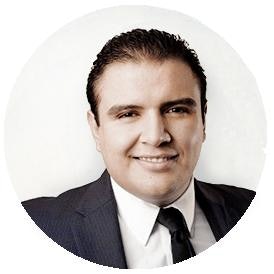
Porfirio Lima, CEO of Sensai, takes a few minutes to discuss artificial intelligence in the manufacturing space with Manufacturing Business Technology.
Manufacturing Business Technology: Even just a few years ago, AI seemed like a futuristic ploy, but it's here and now — what do you think accelerated the demand in the manufacturing industry?
Porfirio Lima: I’d like to paraphrase Stanford University Professor Tony Seba, where he shares, “single technologies themselves are not what causes disruption, technology convergence is.” I love this sentiment and believe there is so much truth in it.
There are many factors advancing digital transformation and incorporation of AI in manufacturing, but I feel the below are the top five drivers:
- Cloud computing makes it easy to store, process and deliver massive amounts of data in a very cost efficient and agile way.
- The convergence of OT & IT across organizations helps drive higher productivity through digital transformation.
- Reduced costs of edge devices and wireless sensors enable cost effective ways to instrument and monitor certain asset conditions.
- A greater understanding of the potential of Machine Learning and Data Science to solve issues that can’t be solved in Excel.
- A top management interest to look into new ways to digitize their business models and products as we live in an age of constant disruption. It is truly — disrupt or be disrupted.
Manufacturing Business Technology: Can you expand on what you think are the most promising aspects of AI for manufacturers?
Porfirio Lima: I believe the single most promising aspect of AI for manufacturers is related to its capacity of delivering a state of foresight. Sharing what will happen in the future given a set of certain conditions in the present. That knowledge will allow an exponential increase of productivity across the value chain.
Imagine the potential of having full awareness and visibility of all mission-critical conditions of your operations from raw materials to end products. And also, knowing that you are making intelligent proactive decisions to optimize any potential “muda” or waste. This type of knowledge has a major impact on the bottom-line for many organizations that know how to look for it.
I also believe in the immense power of a fully responsive and proactive knowledge center that creates solutions to potential issues that appear on the shop floor. Knowledge truly is power. Most organizations rely on their people to manage the collective know-how of the company. However, when employees retire or leave to work for the competition, all of that know-how walks out of the door with them. Creating a permanent digital centralized knowledge center will become a point of differentiation for any organization striving to become world-class.
Manufacturing Business Technology: What are some of the challenges manufacturers face before and during implementation that hinder its success?
Porfirio Lima: I believe that one of the biggest challenges that manufacturers face while leading an AI-related initiative, perhaps ironically, has to do with people. In my opinion (and from experience), digital transformation is 1 percent technology and 99 percent leadership. If top management of the organization and all key stakeholders don’t believe in digitization and feel forced to make a transformation, it will most certainly fail.
Another key constraint is that organizations often choose a specific department within the organization to lead the charge (IT, Maintenance, Manufacturing, etc.); however, this is the path of most resistance. Digital transformation is a cross-organizational effort. It requires a devoted multidisciplinary team to lead through all of the key hurdles that may arise in each area of the organization with their domain expertise and their digital transformation mindset.
Finally, another major challenge within companies seeking to digitally transform is that they see their previous IT investments as “'til death do us part” solutions, and only seek tools that can leverage their current IT investments that were made a decade or more ago. Here’s an analogy to help explain: If you were to try and cut a metal sheet with a pair of scissors, you may be able to do it but it would take a lot of time and effort and, of course, not yield the right quality. Most legacy IT systems were built in an age where AI was not even on the horizon. And Big Data was measured in how many floppy disks the software needed to be installed. Yes, I am painting a grim version of IT systems, but this is the reality. Many organizations still have software that runs in Microsoft 95, use ancient versions of Internet Explorer, and are, overall, not compatible with the current understanding of Big Data and AI.
Manufacturing Business Technology: Do you have any tips on how manufacturers can implement AI into their operations quickly, without waiting years to see real ROI?
Porfirio Lima: First, if you do not have the right operating culture on the shop floor properly implemented DO NOT ENGAGE, I REPEAT, DO NOT ENGAGE(!) in trying to do a digital transformation, implement lean manufacturing, Six Sigma or any other methodology that will standardize the way your shop floor is managed. Get all your people on board, from the shop floor to the top floor. Once you’ve done that and your team can do everything you want on paper, then start your digital transformation effort. You can’t skip this extremely important step. Period.
Second, do not try to solve new problems with old tools. Some of the systems that you currently own pre-date the age of the internet and Big Data, so be willing to let go of things that are currently working “just fine” for new solutions that will work even better. “Just fine” isn’t enough to compete today. Be bold. Be brave and make sure that your leadership team embraces this mentality of exchanging legacy systems for newer technologies.
Third, have a dedicated team of Subject Matter Experts leading your digital transformation efforts with a holistic view of the business to avoid making new solutions with a short vision that will eventually yield disconnected and siloed solutions
And, finally, rethink the way your organization thinks about data. I had a conversation with the CIO of a multinational company, and I remember this phrase: “We have the KPI’s that we can measure, not the KPI’s we actually need”. It’s important to focus on letting your teams explore a world of full data access. If they were to have a “Magic Wand” to wave, what kind of things would they like to measure to make business decisions in their roles? As a result, you may hear requests for KPI’s that were never considered before, like a Knowledge Downtime because you can now measure how much time people spend looking for information that they don’t have readily available to consult. That could be complemented by a Knowledge Index that shares how many times people solve problems with their own expertise and experience without consulting any formal source of knowledge or how many times they actually have to go know-how hunting. These are just simple examples of AI and smart data-enabled KPI’s could transform the way you manage your operations, increase productivity and develop talent.
Manufacturing Business Technology: In conclusion, can you share with our readers how digital transformation and AI eases operational burdens for manufacturers?
Porfirio Lima: Today’s manufacturing industry is at a crossroads. Change is happening at an unprecedented speed. Most of the manufacturing assets installed have reached capacity of 15 years or older. There is a tremendous amount of disconnect between IT’s business systems and OT’s operational systems and technology. Everything is converging in a state of business complexity that results in a lack of clarity and a blurry view of what truly happens within the business. This eventually leads to poor decision-making and impacts productivity and profitability.
AI and digital transformation play a major role in simplifying this chaotic environment and provide clarity to decision makers of what the important issues truly are.
For context, it is almost impossible for me, with my limited medical knowledge, to identify and even less, cure, a critical disease with a stethoscope. I need X-ray vision. I need MRI scans and advanced treatment solutions to effectively diagnose the conditions and symptoms. And, perhaps most importantly, I need the knowledge to actually make educated decisions about the prescription to cure the disease.
AI and digital transformation will become the tools for manufacturers so they can diagnose what is truly happening within their organization and arm organizations with the collective know-how of their talent to be able to determine prescriptive solutions to improve productivity. All in all, what an exciting time to be in manufacturing!