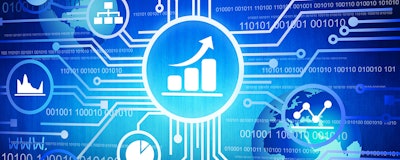
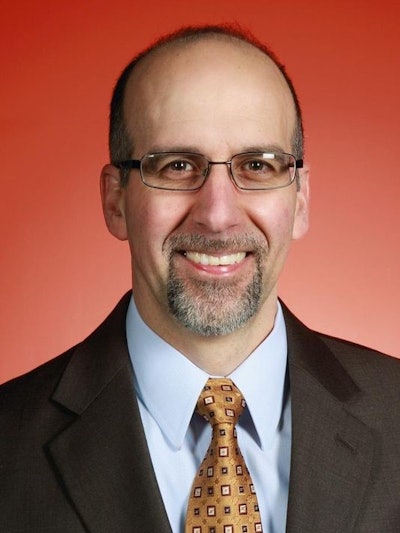
A company’s journey from lab to commercialization can be its best learning tool. The process of ‘making’ a product gives companies the opportunity to perfect their technology, improve quality, control costs and even discover new applications. However, many companies give away — or diminish — this opportunity when companies use third-party solutions to manufacture their innovations.
After spending 40 years commercializing and manufacturing new technologies, I am a strong advocate for companies manufacturing their own technologies. There may be some advantages to outsourcing, for example, short-term savings or capital structures. For companies that make decisions based on longevity and maximized long-term value, however, in-house manufacturing will deliver a better long-term return. The bigger win comes from taking the long view.
Quality Improvement
The biggest advantage to manufacturing a new technology in-house comes from the ‘continuous learning loop’ that it provides. This loop allows a manufacturing team to feed information back to their R&D team with each development cycle. As companies scale, each team will see and understand what works, what does not work, and look for the ways to improve. These improvements are not just limited to the product design, but includes raw materials, process optimization, or packaging. Issues that may have been overlooked in the lab environment, like improved raw materials or large-scale waste management, can add a significant cost at commercial volumes. When companies break this learning loop by outsourcing manufacturing, they impair the ability to find, control and eliminate the barriers to a product’s evolution.
Scale
Most inventions — from IT to chemical inventions — occur in the lab, where prototypes are developed and controlled by highly-skilled technical experts. However, the lab will never be able to replicate the realities of the manufacturing floor. Situations that can be easily managed in the lab, like material handling, equipment maintenance and waste management, have significantly different implications on the manufacturing floor. These variances, which often do not reveal themselves until production actually begins, can affect production times, product yield and cost.
When a company chooses to outsource its manufacturing, the company loses sight of those variances and how the manufacturing partner overcomes them. As the manufacturer figures out how to scale production, they often develop new process pathways or workarounds because they cannot replicate what occurred in the lab. In the meantime, the inventors of the technology may fail to learn about the barriers they face in bringing their product to market. Your company will no longer be the decision-makers when it comes to cost or energy efficiencies and you lose out on opportunities to adjust technologies or work on solutions to improve production overall.
Cost
It can certainly be a challenge to convince investors that in-house manufacturing is the best or most viable financial option. Take the short-term view and outsourcing can appear less expensive, but this decision comes at a significant long-term cost.
Understanding what it truly costs to manufacture a product is critical to knowing whether or not a product can be actually sold into the market. Yet, there are countless manufacturing costs that affect final price and your ability to grow. What is your process yield? How much waste is generated? What are the detailed costs for raw materials, processing equipment, maintenance, warehousing, etc?
What do all these costs have in common? They are all determined during the manufacturing phase, not in the laboratory. And they are learned — and controlled — during the process of scaling up production. It is not easy to estimate true manufacturing costs during lab trials. Without significant manufacturing experience on your team, it is easy to project cost that that understated the final production price and margins. Outsourcing manufacturing may allow a company to influence its starting costs, but they will never know what it actually costs to manufacture their product, or more importantly, how to influence or reduce those costs over time.
Knowledge Protection
There are countless ways that our laws protect intellectual or physical property and most companies do have confidentiality and manufacturing agreements in place with their manufacturing partners. However, as binding as those agreements may be, there is frankly nothing that will stop a third-party manufacturer from acquiring your technology once they produce it on your behalf. After all, these manufacturers are the ones that directly handle your materials, implement fixes when things go wrong, and develop the processes needed to seamlessly manufacture your product.
Along the way, it becomes nearly impossible for that manufacturer to fully divorce themselves from your technology. So, while they may technically honor your agreement, at the end of the day you have not only handed over your technology to another, you’ve also asked them to learn how to make it.
Equally important these days, most manufacturing processes themselves now fall into their own technology category. Today’s manufacturing processes are highly automated and technically-advanced systems. Developing this manufacturing technology in-house can yield both an advantage over your competitors, as well as possible IP that could be monetized at a future time.
Businesses that plan on being around for a while, and want to fully leverage their core technology in a variety of applications, should strongly consider what they stand to gain from manufacturing their products. It generates greater long-term value for the company, the people it employs and the supply chain that surrounds it — all in what is today a very circular economy. I equate the outsourcing of manufacturing to letting someone else do your homework: you may get an ‘A’ in the short-term, but you never actually learn enough to do well on your finals!
Mike Alt, M.S. is Vice President of Technology & Manufacturing at SiGNa Chemistry.