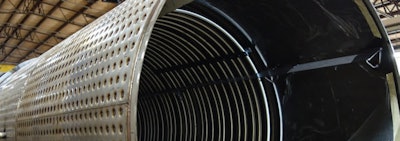
ABSTRACT AND ATTRIBUTES OF ASME VESSEL HEAT TRANSFER SURFACES
Abstract and Attributes of ASME Vessel
Heat Transfer Surfaces
Thermal heat exchange surfaces are utilized on vessels for controlling
temperature and quality of the contents of the vessel. Heat exchange
surfaces can be designed for heating or cooling. Jacketed vessels are
used in many industries and can be used to remove the elevated heat
of reaction (heat reactor vessel) or reduce the viscosity of high viscous
fluids. There are basically three types of external jacketed heat transfer
surfaces: conventional jacket, half pipe jacket and dimple jacket, which
are welded to the outside of the vessel. Internal coils can also be utilized
and can be used as a stand-alone option or in combination with any of
the other types of external jackets.
This white paper serves as an educational and informational reference on
heat transfer methods that use steam or fluid, including:
n Types of heat exchange surfaces
n General application information and comparison
n Optional surface treatments
n Manufacturing terms and definitions
n Regulatory code review
Photo: Stainless ASME tank with dimple jacket and internal coil.
Discover the attributes
and best uses of
ASME vessel
heat transfer surfaces.
© Apache Stainless Equipment Corporation
Conventional Jacket
Conventional jackets are basically an
open jacket with an annular space
containing the heat transfer media on
the exterior surface of the tank. In some
instances, internally welded baffles
within the conventional jacket control the
flow of the heating or cooling agent. In
Apache’s experience, water, oil or heat
transfer fluid is typically used as heat
transfer agents for conventional jackets.
Variable coverage areas and pressures
are available in conventional jacket
designs.
2 © Apache Stainless Equipment Corporation
Shells, bottom head, top head or the
entire tank can be ASME certified.
Best uses
Conventional jackets are best used for
low pressure applications below 50psi.
They are also used in high fluid volume
applications. The major advantage is
that this jacket type allows for the low-
est pressure drop. Conventional tank
designs are often used in small vessels
under 100 gallons.
Note: While the conventional jacket de-
sign allows the lowest pressure drop, it
can also drive up cost due to the thick-
ness of the material required since there
is no reinforcement in the design to ac-
comodate the jacket’s external pressure
requirements on the vessel wall.
Inflated dimple laser or resistant spot
welded dimple jackets are other technol-
ogies available.
Application, specifications, cost and
contractor experience are important fac-
tors when choosing the type of dimple
jacket construction.
Best uses
The dimple jacket design provides a
large heating or cooling transfer area
up to 200 psig. Dimple Jackets are very
versatile. They can be used to provide
heat transfer or cooling for virtually any
shape or size of vessel. Dimple jacket
technology is not limited to tanks.
On large tanks, dimple jackets have a
lower price point and maintain a higher
pressure drop compared to conventional
jackets. On small vessels, conventional
jackets have a lower price point followed
by dimple jacket and half pipe solutions.
Note: Dimple jackets are not recom-
mended for thermal cycling or when
shocking is required. Typically the
stronger half-pipe design is recom-
mended for those applications.
3 zone Dimple Jacket ready for transport
Formed
sheet and
plate header
Dimple Jacket
Dimple jackets utilize a thin gauge stain-
less steel layer that is plug welded to
the vessel shell in a regular pattern. The
punched and spot welded areas are
called dimples, which create turbulence
of the heating or cooling fluid flowing
through the jacket. The Dimple Jack-
et design allows for thinner vessel shell
walls than a conventional jacket design
due to the strength of the dimple pattern
design.
Dimple Jackets are manufactured in
several different pressures and patterns.
Apache provides both 12 ga. and 14 ga.
material. Each pattern is validated and
proof tested per ASME regulations.
Apache has proofed and
certified designs up to
1 ¾” at 200psig at 300o F
but can go to higher
temperatures depending
on the application.
Apache provides a CNC
punched “pre-formed”
sheet. It is MIG and plug
welded to the shell.
Simple schematic
shows conventional
jacket construction
Schematic shows plug welds on dimple jacket
Half Pipe Coil Jacket
The half-pipe jacketed vessel has a split
pipe (split evenly or rolled formed sheet)
wound around the vessel and welded
into place. This design provides op-
timal strength and can be rated up to
500psig. Half-pipe jackets are recom-
mended for high-temperature and liquid
heat-transfer applications.
Material used for half-pipe jackets are
commonly 304, 304L or 316 and can
be welded to a range of alloys. Sound
welding practices allow the half pipe to
be welded to high alloys.
© Apache Stainless Equipment Corporation 3
Internal Coil
Internal coils are utilized inside ves-
sels for transient heating or cooling of
the liquid contained in the tank typi-
cally on a batch basis.
Coils provide heating and cooling sur-
face contact and are manufactured as
a formed spiral around the inside of
the shell or a U-shape in the center of
the vessel from the top head down.
Internal coil heat transfer solutions are
found in many industries. However,
the ability to clean the coil effective-
ly and efficiently may be an issue in
industries that require extreme sanita-
tion and / or food safety protocols.
The internal coil design provides high
flow, high internal and external pres-
sures and high pipe ratings.
Half pipe heat transfer surfaces can
contain the entire vessel or part of
the vessel depending on the appli-
cation.
Other technologies include inflatable
half-pipe designs with laser or resis-
tance welded hat sections.
Best uses
Half-pipe jacket designs are often
used when the jacket pressure is
the determining factor in vessel wall
thickness. In terms of cost and ma-
terial thickness, half-pipe jackets fall
between dimple jackets and con-
ventional jackets on large tanks.
Best uses
Internal coils are often used in
industrial or chemical applications
where the product is not corrosive
to the coil.
Note: Depending on the loads of
the application, the required heat
transfer may not be attainable.
HEAT TRANSFER SURFACES
Standard weld (above) and full penetration
weld (below) on half-pipe jackets
Conventional
Jacket
Dimple
Jacket
Criteria
Best used for large volumes of water used to maintain high
temperature difference.
Conventional jackets are often used in small vessel design.
Pressure
Up to 50 psig optimally, but can be evaluated for higher
pressure depending on the application.
ASME
Shells, bottom head, top head or the entire tank can be
ASME certified.
4 © Apache Stainless Equipment Corporation
CONSIDERATIONS
Conventional jackets require greater shell thickness and expan-
sion joints to eliminate stresses caused by thermal expansion.
A row of small vessels showing channel weldments be-
fore the outer shell is added.
HEAT TRANSFER SURFACES
Criteria
Dimple jackets are well suited to steam applications.
High jacket pressures permitted without significant increase of
side structure thickness.
Efficient heat transfer at low media flow.
Pressure
250 psig with temperature limited to 500o F.
ASME
Approved by the National Board of Boiler and
Pressure Inspectors up to 250 psig.
CONSIDERATIONS
While dimple jackets are economical, it may not provide
drainage required by the steam application.
Formed plate or sheet headers and jumpers to maximize
strength and media flow.
© Apache Stainless Equipment Corporation
Half Pipe
Jacket
Internal
Coil
5
Criteria
High jacket pressures attainable without significant increase of
side structure thickness
Suitable for steam, water, hot oil and other medias.
Pressure
Rated up to 500 psig.
ASME
Half pipe coil jackets are not covered in
Section VIII, Division 1 of the ASME code.
CONSIDERATIONS
Half pipe may require multiple sections to reduce
condensate cover on the heat transfer area. The increased
strength and zone capabilities make the half pipe design
suitable for hot oil medium.
Tank showing half pipe construction.
Criteria
Utilized for heating and cooling surface contact with handling
high internal and external pressures.
Efficient heat transfer advantages.
Pressure
Rated to 900 psig.
ASME
Internal coils can be included as part of an ASME vessel but
aren’t required to be code stamped.
CONSIDERATIONS
Internal coils may be subject to contamination of the
vessel contents, especially if contents have
corrosive properties.
Internal coil shown as part of the bottom head.
The stay-bolt, also referred to as stay-rod, jacket is
another design for heat transfer that handles elevated
temperatures and pressures that cause stress. Rods are
individually welded between the inner shell and outer
jacket providing a robust jacket design.
In Apache’s food processing equipment line, Mepaco,
the stay bolt jacket is used on the ThermaBlendTM Cooker.
The cooker is engineered for large scale industrial batch
heating and cooling operations.
Due to the extremes in steam heating and cooling pro-
cesses combined with constant agitation from blending,
the 90+ psig, ASME rated, ThermablendTM stay bolt jack-
et is recommended for such demanding applications.
While the stay bolt jacket is used exclusively in the Me-
paco line, the dimple jackets used in the tank product
line are also used in Mepaco equipment requiring heat
transfer.
Mixers and auger carts can also be engineered with
dimple jackets to provide continuous heating or cooling
to food processing applications. Temperature control on
mixers, cookers and auger carts can also include steam
injection and CO2.N2 injection in addition to ASME dimple
jacketing.
Requirements for dimple and stay bolt jackets are depen-
dent on the food processing application.
Visit www.mepaco.net for more information.
6 © Apache Stainless Equipment Corporation
The heat shield removed on the ThermablendTM cooker
exposing the stay bolt jacket.
Mepaco Food Processing Equipment using
Stay Bolt and Dimple Jacket Heat Transfer Solutions
The auger cart is a pumping system that provides food
product transfer between processes. The dimple jacket
allows product to maintain required product temperatures
during transfer.
FINISHING
OPTIONS
PICKLE PASSIVATION
When required for the application, Apache provides
full immersion passivation as a means to remove free
iron and aid in the formation of the stainless material’s
passive oxide layer. Full immersion passivation is
also an efficient method of color cleaning the exterior
welds on a tank. Dimple jackets are often passivat-
ed as a by-product of another requirement that was
specified for the tank. Passivation also helps Thur-
malux adhere to stainless.
THURMALOX
Thurmalox is a high temperature industrial protective
coating that is used on conventional, dimple and half-
pipe jacket designs.
© Apache Stainless Equipment Corporation 7
The product is an air-drying, silicone based heat
resistant coating that protects thermally insulated
austenitic stainless steel from chloride induced stress
corrosion cracking. Apache uses Thurmalox 70,
which withstands temperatures to 1000ºF (538ºC)
with peaks to 1100ºF (593ºC).
It is formulated to contain the minimum amounts of
attainable chlorides, halides, sulfides, nitrates and
metals that induce external stress corrosion crack-
ing. An independent laboratory for leachable chloride
content tests each batch of Thurmalox 70 before it is
released.
Pickle passivated dimple jacket prior to insulation. Heat reactor vessel showing Thurmalox coating.
TECHNICAL
TERMS
Agitation
Agitation can be used in jacketed vessels and with inter-
nal coils to improve the homogeneity of the fluid proper-
ties. Agitation is commonly used in batch applications.
Chemical Reactor
A chemical reactor removes the elevated heat of reaction
to reduce the viscosity of high viscous fluids.
Formed Sheet and Plate Header
Apache uses large formed sheet or plate headers to en-
hance the flow capability of the jacket and maximize the
strength of the inlet and outlets of the jacket.
Heat Exchanger
A device used to transfer heat between two or more
fluids.
Heat Transfer Media
Media types include water, steam, glycol, hot oils and
other fluids.
Thermal Shocking
Thermal shocking introduces alternating low and high
temperatures for rapid cooling and / or heating applica-
tions.
Wetted Surface
The area of contact between the liquid and the wall of
the tank often used to determine the emergency venting
capacity required for the tank.
Zones
Heat transfer jacketing can be applied in individually
welded zones to allow for separate zones to be thermally
controlled on an individual basis.
References:
National Boards of Boiler and Pressure Vessel Inspectors
Apache and Mepaco engineering experts and project library
About Apache
The Apache Stainless Equipment Corporation employs
experts and artisans in the fabrication of stainless
equipment for a range of industries. Our expertise in
stainless and high- alloy vessels is shown on Apache’s
tanks and vessels, and Mepaco’s food processing
equipment used in the beverage, biotechnology, phar-
maceutical and food processing industries.
ASME is a leading developer of codes and standards
in the mechanical engineering community. These
standards enhance public safety and health as well as
promote innovation. Apache has been ASME certified
for over 40 years.
In addition to ASME, Apache is also accredited in
many other global standards. By setting parameters
for quality and compliance, we offer greater value for
our equipment products.
Apache consists of four business groups: ASME
tanks, portable vessels, contract manufacturing and
Mepaco®. With modifiable options, Mepaco’s product
line includes: thermal processing equipment, mixers,
blenders, augers, dumpers, sanitary conveyors and
material handling systems.
As a 100% employee owned company, Apache’s cul-
ture exemplifies continuous improvement, efficiency,
innovation and commitment to our customer.
Phone: (920) 356-9900 or (800) 444-0398
E-mail: [email protected]
Web: www.apachestainless.com
200 W. Industrial Drive | Beaver Dam, WI 53916 USA
ASME tanks manufactured by Apache are found in fuel refineries,
ethanol plants, chemical industries, pharmaceutical and biotechnol-
ogy companies, food processing facilities, water treatment facilities
and health and beauty product manufacturing plants.
Apache has fully equipped facilities that allow fabrication of our
products in-house.
Punched and laser cut dimple sheet prior to plug weld