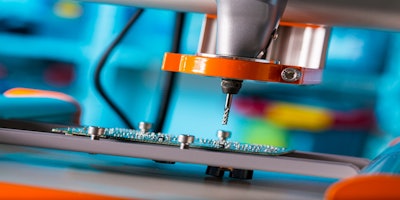
P C B M A N U F A C T U R I N G W
H
I
T
E
P
A
P
E
R
w w w . m e n t o r . c o m
FIVE STATISTICS THAT WILL DRIVE
CHANGES IN PCB MANUFACTURING
Five Statistics that Will Drive Changes in PCB Manufacturing
w w w. m ento r.co m /v al o r
2
Manufacturing is an old process that has changed little in recent years. Worse than that, it is part of an older
business process that many argue is no longer fit for the needs of the electronics market. New paradigms in
buying patterns are putting pressure on factories to become a whole lot more flexible. Innovations, such as
“Industry 4.0” in Germany, attempt to meet these market-force requirements with technology-based solutions.
The reality is that the problem surpasses manufacturing and includes the whole business process that has
become entrenched in bad habits.
And although efforts are made to streamline and optimize, the big picture is not changing. With so many
different profiles of electronics manufacturing companies and operations, there can be so many excuses why
not to change. Newer, smaller, up-and-coming companies can take advantage of legacy business practices,
which surely signals a major change coming for the current industry players. In this paper, we expose some of
the most shocking statistics in manufacturing, which highlight opportunities available today that enable
significant changes to happen.
We’ll consider five manufacturing statistics that illustrate the most compelling opportunities, which, when
viewed as part of an overall business process, are mind-blowing. While looking at these statistics, remember
that a successful manufacturing business simply can deliver the most compelling products that the customer
wants, when they want them, and at a reasonable price. This includes a choice of products from different
companies that are competing. The compelling product that the customer chooses may be the one with the
specification that most meets their needs, whether it is the most fashionable, the most cost-effective, or
simply available at the moment. The compelling product can not have a known market-quality issue or not be
available for purchase for any reason.
95% OF MANUFACTURING BUSINESSES FOCUS ON OPTIMIZING JUST 1% OF THEIR
TOTAL BUSINESS COST
If you take an example of the latest technology products built today in China, the contribution to the final
product retail cost, before sales tax, can be as little as 1%. Why then, are companies so focused and concerned
about this, to the detriment of factors like quality, flexibility, risk, and costs such as depreciation and
distribution? It started historically, where labor cost in “olde-worlde” factories that once existed close to the
market represented the majority of the fixed cost of the operation, in many cases around 30%. With product
cost a major competitive factor, the move toward off-shoring of manufacturing to locations with lower labor
costs started, which for many recently has been China, although now also, Vietnam. Once all major companies
had off-shored manufacturing as a key part of their business, the once competitive edge of accessing lower
cost labor was lost, so that now even the most prestigious brand names are fighting literally over the
reduction of the last 1% that labor cost now contributes to the final price of fashionable high-tech products.
The issue is that during this process, other cost contributors as well as the other factors that affect how
compelling a product is to a customer have been ignored, while they have gradually become much more
significant.
Distribution cost was originally a key argument against off-
shoring, although in reality, the cost of long-haul bulk shipping
when considered on a per unit cost basis was not so significant.
Today, however, it is not only bulk shipping that is inexpensive.
Consider an example where a modest technology-based
product, such as a quality LED bulb, retailing at around $20 in a
general store in the United States can also be bought on-line
from a small company in China for $4, which includes free
shipping. We have to assume from this that $4 represents a fair
price for the manufactured product with a reasonable profit for
the manufacturer, some profit for the Chinese sales company,
and of course the real cost of postage. The decision then for the customer looking at this deal is whether they
pay $20 for the bulb today or wait three to six weeks for the product to be delivered from China, saving 80%
of the cost. In an energy conscious and austere world, with so many lightbulbs potentially needing upgrading
The true proportion of manufacturing versus other costs has been
exposed.
Five Statistics that Will Drive Changes in PCB Manufacturing
w w w. m ento r.co m /v al o r
3
in an average house, the wait for many will be worth it. For sure, the reason for the $16 differential can be
explained in many ways, including depreciation, taxes, risk, as well as costs related to domestic logistic
networks and cost of retail outlets.
If customers are willing to buy goods on-line from China with the wait and risk of dealing potentially dodgy
traders, how much better would it be if the factory was based on U.S. soil, using the same model as the
Chinese sales company, shipping directly to customers? On-line shopping and direct shipping for brand-name
goods is already available, but so far, it is a half-hearted attempt to establish a web sales presence because the
goods still need to be shipped in from China, stored, and managed in on-shore warehouses, with all the risks
and depreciation of product value that it brings. Therefore, this shopping method does not bring compelling
business flow to the brand leaders by itself, and so pricing at such on-line outlets is usually comparable to
on-shore retail. An on-shore factory with direct shipping could have a far higher degree of success with a
small and simple warehouse inside the factory. The factory must then be flexible to respond to more random
shopping demand requests from customers, while remaining productive. The labor cost today in such an
on-shore factory could be five to ten times that of the corresponding factory in China, but it represents about
$2 per unit in our light bulb example, small by comparison to the cost saving from distribution. This argument
will be valid to a different extent in different sectors and sizes of operations in the industry. There are key
factors in the manufacturing equation then that must be considered, ones which in themselves also yield
some mind-blowing statistics.
SMT OPERATIONS OFTEN RUN AT AS LITTLE AS 20% ABSOLUTE PRODUCTIVITY
The important word her is “absolute”. Sometimes, there seems to be more effort put in to making reasons and
excuses that allow reporting of artificially higher productivity levels than finding ways to actually improve. In
high-volume manufacturing, where production lines were dedicated to a specific product and where the lines
could run at full capacity all the time with fully optimized SMT machine programs, the level of absolute
productivity could be as high as 85–95%.
Only holiday shut-down, equipment maintenance, some time for material issues, and the occasional machine
break-down would affect the headline achievement. Unfortunately, very few SMT operations continue to
operate in a high volume way. With the increasingly fast evolution in technology and the fashionable status of
many technology products in global markets, a multitude of variants of each product are being sold
concurrently, each of which exhibits limited life-cycles, with only a small window at introduction to attract
premium pricing and a significant risk of steep price depreciation thereafter. The depreciation factor has
become a significant driver in recent years to reduce the amount of stock in shipping, hubs, warehouses, and
distributors. The effect of this on the factory is the
need to not only produce a high mix of products
but also to cope with sudden changes of demand.
These factors are the key cause of the low
productivity seen in many SMT operations
currently. The productivity reported in such
factories is much higher than the 20% absolute
value, which only a few will admit to. Factors such
as certain aspects of changeover time, line balance
losses, engineering setup time, maintenance, and
new product introduction time can all be used in
the calculation to boost the headline number. The
reality is that many of the so-called “unavoidable”
losses are effectively ignored, even though they
may actually be avoidable; and as product mix and
volatility of demand continue to increase,
attention on these issues will be necessary. It is
easy in a simplistic way to calculate the effect of
lost absolute productivity on the business as a
Red lanterns are often ignored or turned off as excuses become the
norm.
Five Statistics that Will Drive Changes in PCB Manufacturing
w w w. m ento r.co m /v al o r
4
whole. If, for example, a factory was capable of 80% absolute productivity when running high-volume
production, and if now it is running at 20% in a high-mix scenario, it means that the total cost of
manufacturing per product, excluding materials but including labor, is 400% higher.
Most of this lost productivity can be regained, even in a high-mix and high-volatility scenario. The creation of
common material feeder setups that adapt dynamically to customer-demand patterns, where optimization of
work-order sequences are done simultaneously with the choice of product grouping, is critical. This can be
done with today’s best tools almost completely automatically, while providing the assurance that individual
SMT machine program optimization is not compromised severely through any incorrect grouping and feeder
arrangement setup. Many operations can, using these software tools, achieve productivity levels in high-mix
scenarios that approach that of high volume. Adoption of the lean material management logistics further
enhances flexibility on the shop-floor to carry out planning changes in a way that is fluid, and without
significant loss or risk. For our on-shore company idea, this level of flexibility without loss of productivity is
essential for the factory to meet the close-coupled demand pattern from the customer. Consideration of
materials is our next mind-blowing manufacturing statistic.
75% OF RAW MATERIALS IN AN SMT FACTORY NEED NOT BE THERE
The adoption of lean material logistics is an essential part of providing flexibility in the SMT production
operation. As an enhancement to ERP’s management of materials, in terms of accuracy and control especially
for material WIP on the shop-floor, Lean material logistics can also reduce the amount of buffer stocks in the
factory. The key issue that this resolves is that of inventory accuracy. Because SMT materials are on bulk
carriers, such as reels, many more materials are issued to production by ERP than are actually needed. In a
high-mix environment where discrete production runs are quite short, it can be that most materials issued will
not be immediately consumed by the targeted work-order. Because of the nature then of the SMT machines,
there can be variable and volatile spoilage of materials during the placement operation, both through the
machine and manual operations. The amount of materials left unused after executing a work-order is
unknown. Most often, it is not practical in a
production environment to manage lost or
unused materials to the extent that overall
inventory accuracy can be maintained. The
proof of this is found in the result of the
periodical stock check, which reveals the need
to write-off significant amounts of materials,
often worth millions of U.S. dollars per year for
larger operations. Accumulating inventory
inaccuracy brings unexpected internal material
shortages, which in turn leads to the habit of
instructing MRP to over-order materials
creating bloated warehouse inventories,
providing a buffer of excess materials until such
time as the inventory corrections are made at
the next stock check. The introduction of Lean
material management eliminates 95% of the
material WIP on the shop floor because
materials are issued only when needed to the
SMT machines and other assembly processes
and are then returned to the warehouse when
no longer required on the shop-floor.
During this process, inventory accuracy is maintained through the collection of data directly from each SMT
machine so as to account usage and spoilage. The rate of material consumption is used to generate the pull
signal for the next material delivery, in conjunction with the progress information against the production plan,
in the case of changeovers. Because the material inventory accuracy is maintained, internal material shortages
Inventory turns will double as warehouse space halves.
Five Statistics that Will Drive Changes in PCB Manufacturing
w w w. m ento r.co m /v al o r
5
are eliminated as continuous updates are made to ERP. MRP can then maintain buffer stock levels in a more
timely and consistent way according to only the real business need, re-ordering materials only where there is
a significant spoilage issue. As a result, warehouse inventory can be reduced by as much as 75% without risk
of shortages to production occurring. As well as the reduced cost of material investment of the excess
materials, which is one of the major factors in any electronics manufacturing operation, flexibility to change
production schedules and even to execute changes in product life-cycles is enhanced, with reduced risk of
material obsolescence.
30% OF PRODUCTS LEAVING THE FACTORY WERE NEVER TESTED
It has been proven statistically that the incidence of defects found in the market is proportional to the number
of defects found during manufacturing, no matter how much testing is performed. The conclusion is that the
whole test and inspection process is merely a filter of issues, which cannot find all defects. There are different
categories of defect that happen in the market. Straight out manufacturing defects can happen in areas of the
product, usually minor, that are not tested or are not testable. Some defects will pass tests in the factory only
to fail once the product has been in use for a while in the market, such as defects caused by poor and brittle
soldering, or misplacement of parts where there has been just enough connection to last a short time until
the product is stressed. Beyond this, there are material defects and failures caused by usage of the product
outside of designed parameters. Being able to qualify design and material application issues can be of huge
benefit in the reliability of safety critical products such as automotive, medical, aerospace, industrial control,
and even branded consumer goods, but this is expensive to achieve when faced with significant numbers of
manufacturing-related defects.
Knowing the market-quality statistical situation, the
emphasis for quality moves away from test and more
toward the manufacturing processes themselves.
Manufacturing defects are most often caused by variations
in the production processes, some with a simple cause-
and-effect, while others occur as a result of two or more
factors working together. As a first step, each process
needs to be qualified and checked that the setup and
operational guidance was done correctly according to the
specific instructions and documentation. Today’s leading
process preparation tools can create SMT programs, test
and automated inspection data, as well as operation
standards for manual processes, from a single product
model in an accurate and consistent way. These tools
include the simulation of the operation, for example, the
visualization of correct rotations for SMT placement,
confirmed checks that use alternative or substitute
materials will not cause placement issues, revision control, and BOM checks across all of the different assembly
processes. Once the process preparation has been completed, the second step is then to ensure adherence,
that is, to ensure that all production operations are carried out in the exact way specified and that any
variances are highlighted and eliminated. For most SMT and related operations then, the test and repair
processes are the third and final step.
The most often neglected tool, however, is the application and use of traceability data within manufacturing.
As safety-critical segments such as automotive, medical, and aerospace know, the collection of traceability
data of processes and materials is essential to quickly determine the scope of any market-quality issue and
then reduce the scope of any costs or liability. However, if the traceability data is accurate, complete, and
timely, information about the defects is already there and could be found before the products left the factory.
Analysis of traceability data can show such issues as PCBs that were printed with solder paste but were then
left for too long before placement was completed, perhaps caused by some machine breakdown, which
condition has historically been shown to cause a higher incidence of poor solderability that result in market
Testing provides only a filter through which defects
prevail into the market.
Five Statistics that Will Drive Changes in PCB Manufacturing
©2015 Mentor Graphics Corporation, all rights reserved. This document contains information that is proprietary to Mentor Graphics Corporation and may
be duplicated in whole or in part by the original recipient for internal business purposes only, provided that this entire notice appears in all copies.
In accepting this document, the recipient agrees to make every reasonable effort to prevent unauthorized use of this information. All trademarks
mentioned in this document are the trademarks of their respective owners.
F o r t h e l a t e s t p r o d u c t i n f o r m a t i o n , c a l l u s o r v i s i t : w w w . m e n t o r . c o m
4-15 TECH12830
defects. It is quite impractical to think that every possible deviation from the normal operation of a production
line can be noticed and addressed as it happens, especially those cases where risks of defects occur as a result
of two or more simultaneous issues; for example, a screen printer executing a cleaning cycle that results in a
slightly more uneven paste, at the same time as the use of an alternate material that had a slightly smaller
body height than that specified to the SMT machine, then going through a reflow oven which was at the high
end of its temperature profile range. In isolation, none of these three issues are likely to cause a defect, but
combined they could create a placement that “floats” off its designated position, creating a so-called “one-
off” defect that may not be found until it is a failure in the market. Complete, accurate, and timely traceability
data can be the ultimate quality tool, acting in a far better way than regular test processes.
80% OF FACTORY MANAGEMENT KNOW THESE STATISTICS, BUT FEEL POWERLESS
There is usually a different management process relating to the business of a product compared to the
business of manufacturing. In an OEM company, manufacturing is usually treated as a non-profit operation,
with factories working to a budget. This effectively creates a barrier that can prevent product performance-
related issues, such as the cost of poor quality in the market used to justify an internal request in the factory
for new quality management software. Having been in this situation for many years, the current OEM factory
operating principles in terms of productive and flexible operation cannot effectively meet the needs of the
customers and the business, and they are now distinctly behind the times. The use of EMS services often
means this barrier between the business and manufacturing is larger, bringing with it commercial
implications. It can be seen already in the market that certain EMS companies are now offering to work far
more closely with their customers as understanding of the mutual benefits is gained, although this is quite a
rare case.
Going forward, seeing the significance of the numbers suggested here, put into financial terms, it is clear that
with the new volatile patterns of demand from customers, together with the increasing need for more
product variants, the inevitable need is for extreme flexibility from factories that once were clearly focused on
mass production. Considering the complete needs of the business with the analysis of all costs, of which
manufacturing is only a part, brings the realization that the operation and location of manufacturing
processes needs to be reassessed. Manufacturing close to the market is an accepted economic principle, so
why is most electronics manufacturing now done in China? How can the labor contribution in China of just 1%
on the retail price be allowed to be so significant? How can we allow factories to produce only one third of
their potential output, or, to put it another way, be three-times larger and more costly than needed? How can
the access to products by the customers, in terms of pricing, delivery, and quality, be differentiated by
answering these questions? The case of the $4 LED bulb costing $20 in the United States is ridiculous, and yet
typical.
Software that provides specific tools to enhance ERP, providing the ability for cost reduction, increased
flexibility, and improved quality are available, but they are limited in their application mainly because these
questions are not being asked in a serious way by people responsible for the business. Using these tools in a
factory that is then closely coupled with the market can create the basis for a complete rethink of electronics
manufacturing. Perhaps then, for example, U.S. customers could get $8 LED light-bulbs with next-day free
delivery, a much more compelling and competitive product.