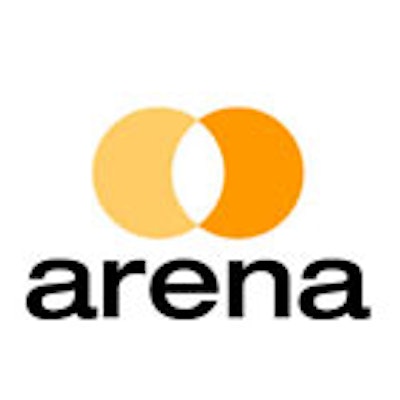
Reduce Regulatory Delays
by Formalizing Design
Control Processes
Whitepaper
arenasolutions.com
©2013 Arena Solutions, Inc. Arena and Arena Solutions are trademarks of Arena Solutions, Inc., Reg. U.S. Pat. & Tm. Off.
All rights reserved. Other product and company names are the property of their respective holders.
1
arenasolutions.com
The path to market for a medical device is fraught with potential obstacles and pitfalls. And the seemingly
Herculean feat of achieving and maintaining regulatory approval looms as an especially imposing task for many
medical device manufacturers. But as daunting as the prospect of working with regulatory bodies might seem, it
is unavoidable. Failing to fully comply with them can lead to serious–and costly–delays in delivering new products
and updates the existing product, as those require DHF/DMR updates and sometimes RA submission.
One of the key strategies to successfully navigating the regulatory pathway, however, boils down to being
prepared, organized, and thorough. And while this advice may seem obvious or simple, its importance can’t
be understated. Luckily, effective product lifecycle management (PLM) solutions, such as Arena PLM, can help
to facilitate proper management of quality documentation in order to ease the pains of the regulatory approval
process while accelerating time to market.
Quality Management Systems
According to the quality system regulation (QSR) known as 21
CFR Part 820, medical device manufacturers must implement
and maintain certain measures to ensure that the devices they
make perform as intended. In essence, this regulation requires
manufacturers to tightly control a product’s design—including
changes that might be made throughout the development
process—by carefully specifying the steps and procedures that
make up each design phase. It also mandates that companies
provide documentation to demonstrate compliance,
specifically in the form of a design history file (DHF) and a
device master record (DMR).
Whether a company submits a 510(k) or premarket approval
(PMA) application, it must be prepared to readily furnish the
appropriate QSR documentation and additional details to FDA
upon request. The same is true for FDA inspections. The catch
with inspections, of course, is that it’s not always possible to
know exactly what information FDA may seek.
But it is possible to make sure everything is in order and organized internally should a request arise from either
an inspection or the regulatory approval process. If all pertinent documents are cleanly maintained and easily
accessible at any time, and if all quality management system (QMS) components are in place, full compliance
with required regulations can be streamlined, stress can be minimized, and approval-related delays can be
reduced or minimized.
Reduce Regulatory Delays by Formalizing
Design Control Processes
Source: FDA
©2013 Arena Solutions, Inc. Arena and Arena Solutions are trademarks of Arena Solutions, Inc., Reg. U.S. Pat. & Tm. Off.
All rights reserved. Other product and company names are the property of their respective holders.
2
arenasolutions.com
The Importance of DHFs and DMRs
When it comes to demonstrating compliance with 21
CFR Part 820, two elements are crucial among many
other critical elements: the design history file (DHF),
the device master record (DMR), and Change and
Document controls.
The DHF is a collection of documents generated
throughout the product lifecycle—including plans and
documents covering procedures related to design input
and output— that explain the design of the product. As
specified in 21 CFR Part 820.30(j), which covers design
controls, medical device manufacturers must “establish
and maintain a DHF for each type of device” to show
that “the design was developed in accordance with the
approved design plan,” as well as FDA’s general quality
system regulations, at each phase of the product’s
design, from inception to design transfer.
The DMR, which is an all-
encompassing collection of
documents and records (including
device specifications, process
specifications, quality assurance
procedures, and packaging and
labeling specifications) is mandated
by 21 CFR Part 820.181. All docs
and records, including DHF and
DRM, must be carefully managed
according to the document
control and change management
requirements specified in this
regulation.
The Role of PLM Tools
FDA expects DHFs and DMRs to be clean and organized and has the authority to demand that these expectations
are met. The agency can respond to more serious infractions, for example, by stopping shipment, issuing a recall,
shutting down a product line for investigation, or even shutting down the product line entirely. Furthermore, FDA
can request an inspection at any time, with any level of specificity. In light of these demands and potentially serious
consequences, it is crucial for medical device manufacturers to be prepared.
©2013 Arena Solutions, Inc. Arena and Arena Solutions are trademarks of Arena Solutions, Inc., Reg. U.S. Pat. & Tm. Off.
All rights reserved. Other product and company names are the property of their respective holders.
3
arenasolutions.com
Managing quality documentation and design control processes can be a complex and hard-to-wrangle
proposition. After all, the manufacturing of a product tends to involve several steps and a multitude of different
parties, from separate departments and internal personnel to external component and service providers along the
supply chain. Additional challenges derived from the collaboration of cross-functional teams that have different
agendas and speak different functional languages.
Every part of the design process must be supported by a document in the DHF, and every document in the DMR
must be carefully controlled. Every single step taken by the manufacturer, including any changes made to the
design, must be governed by a documented procedure and approved by the appropriate personnel.
Because of the sheer volume of people and processes involved—not to mention the level of organization
required—assembling and maintaining a DHF and DMR can be extremely tedious without an effective PLM system
in place. Paper-based systems, in which everything must be checked manually and are never real-time, can cause
delays while increasing the opportunity for error. Adopting a cloud-based PLM software solution, in contrast, can
expedite time to market while facilitating regulatory compliance.
How Arena PLM Can Help
Serving as an efficient solution for electronically
tracking the development of a product, Arena
Solutions’ cloud-based PLM software makes it
possible to ensure that all relevant parties—including
suppliers—are in accord and up to speed on a given
project. The software solution offers the additional
benefit of enabling the consolidation of all compliance
information in one centralized location.
Arena PLM allows for the management of bill of
materials (BOM), DHFs, DMRs, and quality system
records to be compiled, edited, and viewed and
approved by personnel across a company in an
organized, controlled manner. All documents in a
DHF can be accurately and reliably tracked from their
inception while records in a DHF—as well as all the
related changes—can be carefully managed as well.
The software allows companies to streamline and
formalize their document-management processes.
Also necessary for medical device manufacturers are the change and revision-control features of the BOMControl
platform. The software enables compliance with 21 CFR Part 11 and other relevant regulations, which mandate
that electronic records be carefully managed and controlled by authorized personnel. The software carefully routes
any changes to a document or to the product design to the appropriate personnel for review; the authorized party
can then opt to sign off on the changes or not. All changes can be tracked electronically and are approved via
traceable electronic signatures.
©2013 Arena Solutions, Inc. Arena and Arena Solutions are trademarks of Arena Solutions, Inc., Reg. U.S. Pat. & Tm. Off.
All rights reserved. Other product and company names are the property of their respective holders.
4
arenasolutions.com
PLM Beyond the DHF and DMR
Using quality systems regulations as a framework, medical device manufacturers also create internal quality
management systems that consist of standard operating procedures (SOPs), work instructions, and policies in
which employees must be properly trained. Arena PLM makes it easier to maintain these quality management
measures because they can be documented, with each and every change tracked, in a centralized and easily
accessible location.
PLM serves as a critical tool during audits as well. To ensure compliance with applicable regulations, auditors
might ask to review any number of documents stemming from any phase in the design and development lifecycle.
The PLM software allows for quick and easy retrieval of requested documentation.
In addition to its demonstrated value; in documentation and product record management, product records,
streamlining compliance, and traceability, Arena PLM offers the additional advantage of being a cloud-based
software as a service (SaaS) delivery model. Personnel need access only to an Internet browser to operate the
system as companies do not need to involve their own IT departments or servers.
In order to ease or minimize the validation burden from the manufacturer and help comply with applicable
regulations such as 21 CFR Part 11, in which medical device manufacturers must ensure that the systems they
use to manage electronic records are validated, Arena offers a validation maintenance service (VMS). Each release
is validated in-house against a well-defined set of intended uses for each release. Customers are then provided
with validation documentation to confirm that updates to the software have, in fact, been validated and Arena PLM
conforms to its predefined intended uses.
PLM
SUSTAINING
PROTOTYPE
PRODUCTION
NEW PRODUCT
INTRODUCTION (NPI)
CONCEPT
©2013 Arena Solutions, Inc. Arena and Arena Solutions are trademarks of Arena Solutions, Inc., Reg. U.S. Pat. & Tm. Off.
All rights reserved. Other product and company names are the property of their respective holders.
5
arenasolutions.com
Conclusion
Medical device manufacturing, by virtue of its dealing with life-critical products – is rife with challenges. Stringent
regulatory requirements burden globally disparate cross-functional personnel. These stakeholders become mired
in multiple phases of a lengthy product development cycle – while striving to maintain exacting quality standards.
Implementation of a cloud-based PLM solution, such as Arena PLM, however, can promote good manufacturing
practices while enabling robust product recordkeeping, traceability, change and document management. In turn,
medical device manufacturers can effectively streamline operations, nimbly navigate unexpected bumps along the
regulatory pathway, and ultimately expedite time to market.
©2013 Arena Solutions, Inc. Arena and Arena Solutions are trademarks of Arena Solutions, Inc., Reg. U.S. Pat. & Tm. Off.
All rights reserved. Other product and company names are the property of their respective holders.
6
arenasolutions.com
About Arena
Arena invented cloud-based PLM. For over a decade, Arena has
been redefining PLM with a suite of cloud applications that enable
engineering, manufacturing and their extended supply chains to
work better together—from first prototype to full-scale production.
Arena helps innovative manufacturers bring better products to
market faster with cloud PLM offerings that speed prototyping,
reduce scrap and help manufacturers collaborate on product
changes with strategic partners worldwide. Based in Foster City,
California, Arena has been ranked as a Top 10 PLM solution, Top 5
Supply Chain Collaboration application and also holds a spot on the
San Francisco Business Times’ Best Places to Work List for 2013.
Contact
Arena Solutions
Foster City, CA 94404
P. 650.513.3500
F. 650.513.3511
2013.06.27.cleantech.wp
Cloud. Connected. Content. Makes Making Easier.