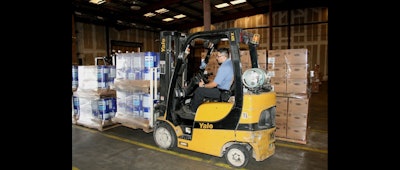
Global sales in the chemicals industry exceeded $5 trillion by 2013, and more growth was projected — ranging from 5 percent to 7 percent. Transporting all of those chemicals to the point of use requires a robust logistics network. That industry also was projected to grow, at a compound annual rate of about 5.48 percent, from 2014 to 2019.
Transporting and storing chemicals is a complex business, requiring special handling techniques to ensure environmental safety, as well as the safety of workers and nearby communities. Safe handling is regulated by a variety of government agencies, including the Environmental Protection Agency, Department of Transportation and Occupational Safety and Health Administration, and thus it can be complicated to ensure you follow every regulation correctly. Here are a few tips to help you ensure you’re in compliance.
Identify Hazardous Materials
This sounds simple, but it actually can be one of the hardest steps to follow. According to OSHA, a hazardous material is any substance that can cause physical safety issues (such as fires or explosions) or health issues (such as irritation or burns) or that can cause cancer or other diseases. The EPA has so many lists that it actually provides a list of its lists. The U.S. DOT has yet another list. Individual states have lists. Your best bet is to validate the material in question against these lists and to work with your supplier and customer to understand the characteristics of the substance in question and the best way to handle it safely. In general, shipper responsibilities are governed by Title 49, Part 173 in the Code of Federal Regulations, while worker safety is governed by OSHA.
Label Materials Carefully
Both OSHA and the U.S. DOT have very specific labeling requirements for every material or class of material. It is imperative that all materials be properly labeled, both for safety reasons and to control liability. Fines for violations can be up to $250,000 per incident from the EPA and $75,000 for knowingly violating the federal hazardous material law. Safety considerations aside, it makes business sense to be certain you’re in compliance.
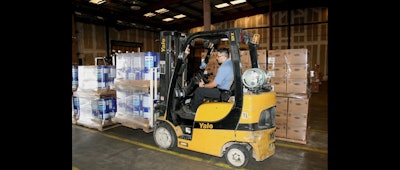
Don’t Skimp on Training
For the safety of your employees and your community, you should ensure that every employee has an appropriate level of training in proper material handling for any chemicals on your premises, and also those that your company is transporting. Training should include safe handling techniques, first-aid remedies and emergency procedures. You are required to provide protective equipment and clothing, and your employees should know when and how to use it.
Even employees who may rarely or never come into contact with substances should receive first-aid training and emergency-procedure instructions to ensure safety and compliance.
Use the Right Packaging
Chemicals must be stored in the correct containers at all times. Sometimes companies justify using unapproved packaging because they are storing or moving only a small quantity of a chemical, but this is not a good practice. Even very small quantities of some chemicals can cause serious injuries or death. Using packaging designed for the class of chemical will help eliminate the risk of injuries due to leaking, fire or explosion.
Store Chemicals Strategically
Certain chemicals may be relatively benign on their own, but may become caustic or explosive when combined with another substance. Know the reactivity of chemicals under your control, and ensure that substances that should not be combined are stored and transported separately. Just as with packaging, this rule holds true even for very small quantities, especially if you are unfamiliar with the potential volatile reactions of the substances.
Use DOT-Approved Marking During Transport
The U.S. DOT has precise requirements for marking containers and trucks that are carrying chemicals, and it also specifies the documentation and paperwork required for shipment. The required documentation includes information pertaining to emergency response as well as compatibility.
If your organization is engaged in chemical logistics, even occasionally, it is a good idea to familiarize yourself with the regulations that cover safe handling and transportation of chemicals, especially hazardous chemicals. Knowing the federal regulation and OSHA requirements for training and safe handling of chemicals can protect your employees, your community and your company.
Lynn Place has 30 years of professional experience in the manufacturing, market research and advertising industries. Place is Vice President of Marketing for SolvChem Custom Packaging Division, and specializes in consumer packaged goods, new product development and strategic planning.