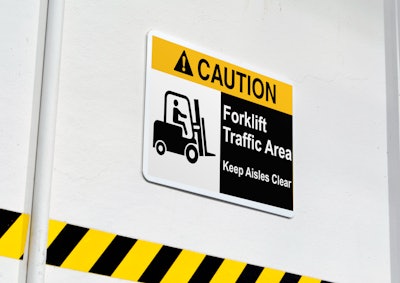
Warehouses are statistically one of the most hazardous places to work and safety depends on workers being aware of their surroundings and knowing which hazards are most common in their workplace. The most common injuries in warehouses are from:
- Forklifts – In 2013, OSHA reported that 37 percent of deaths and 71 percent of serious injuries were caused by being struck, thrown, or crushed by forklifts.
- Slips and falls – Over 12 percent of the major injuries reported in 2013 were caused by slips and falls. Many of these injuries were the result of improper training or workers violating safety rules.
- Falling objects – Falling objects accounted for 20 percent of the major injuries and deaths reported in 2013.
- Repetitive motion such as lifting, reaching, pulling, and pushing – According to the International Warehouse Logistics Association, most reported injuries in warehouses are the result of poor ergonomics.
- Failure to wear the correct personal protective equipment (PPE) – Failing to wear PPE exposes workers to additional risks. PPE helps protect workers from respiratory, impact, and crushing hazards. One of the most commonly cited violations in warehouses comes from workers not using proper respiratory protection.
By teaching workers about the most common causes of injuries, workers can better recognize and avoid hazards, improving warehouse safety.
OSHA Warehouse Safety Regulations
OSHA has many regulations designed to keep people safe while working in warehouses. These regulations can be found in OSHA’s General Industry Standard 29 CFR §1910. Some of the most commonly cited warehouse safety regulations are:
§1910.178 – This regulation requires businesses to train operators and perform routine forklift maintenance. It also contains strict rules for modifications which may affect the ability to safely operate forklifts. Employers must prove that modifications do not make forklifts more dangerous to operate (reduce visibility, stability, and so on).
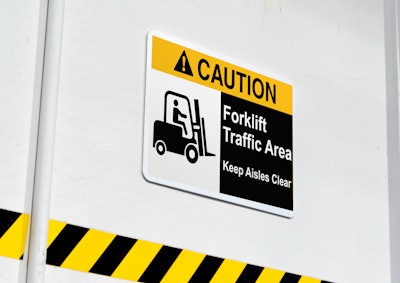
§1910.176 – Closely related to §1910.178, this regulation requires facilities to maintain safe clearances and keep aisles clear. In addition, OSHA requires employers to use floor marking and signs to permanently mark passageways that will be used by forklifts and other powered vehicles. Materials also must be securely stored, so they won’t collapse or fall on workers.
§1910.1200 – The second most cited regulation in warehouses, otherwise known as HazCom 2012, is designed to protect workers from hazardous chemicals through effective communication. To help protect workers, OSHA’s Worker Safety Series: Warehousing requires that warehouses provide:
- Cleanup kits wherever chemicals are stored
- A written spill control plan
- Proof that workers have been trained to handle chemicals properly
- Proper PPE
- Secure storage for all chemicals
- Proper labeling for all chemicals
§1910.132 – Another important safety regulation concerns the use of PPE in the workplace. Specifically related to warehouse safety, OSHA found that workers are often not trained about the following:
- When to use PPE
- What PPE is needed
- How to properly wear PPE
§1910.23 – This regulation requires employers to guard openings in floors and walls. Every stairway, ladderway, hatchway, and chute opening must be guarded according to OSHA’s standards. These requirements help keep workers safe from trips and falls.
The best way to keep workers safe is to follow OSHA’s rules and regulations. These regulations are designed to mitigate most workplace hazards. Having the proper training, the correct PPE, the right equipment, and an approved safety plan will go a long way towards reducing injuries.