
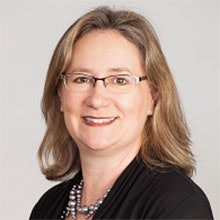
Food and beverage manufacturers have invested heavily in their assets, which can be a significant portion of the capital invested in a plant. The top two pressures often faced are maximizing the return on these assets (ROA) and managing and mitigating risk due to the failure of critical assets. Unscheduled asset downtime results in lower production efficiency and higher maintenance costs, directly impacting profitability. In the food and beverage industry, unscheduled downtime can also incur the costs of wasted product that must be disposed of when a production process halts and cannot be completed. Aberdeen Group has identified the following Key Performance Indicators (KPIs) of Best-in-Class companies:
- 4.6% Downtime
- +16% Operating Margin vs. Corporate Plan
- 12% Decrease in Year-Over-Year Maintenance Costs
- +14% ROA vs. Corporate Plan
Cost savings is not the only reason to improve asset efficacy. Ineffective equipment can also affect the quality of the product being manufactured. Foreign matter contamination resulted in 44 recalls in 2016, and one of the most common causes for these contamination events is improper or absent maintenance of equipment and facilities. An important element of the preventive controls requirement of the Food Safety Modernization Act (FSMA) is ensuring that assets are properly maintained and operated. An Enterprise Asset Management (EAM) solution which can support and enhance an effective asset management strategy is indispensable to achieving asset reliability.
Predictability — 'Failure is Not an Option'
Every organization wants to operate at peak efficiency, and functioning equipment is vital to keeping product moving out the door. Unreliable assets can turn your production floor into a break room, as your production workforce idles while assets are down. The right maintenance strategy is an essential component in supporting costly assets. Maintenance tends to be viewed as an overhead burden that must be strictly controlled and reduced when possible; however Best-in-Class companies have observed how the maintenance organization can contribute to the overall financial success. In order to move from a reactive to a proactive approach to maintenance, the company must have access to asset information. With this information, a company can determine the best maintenance strategy for each asset, and implement it accordingly.
Many Best-in-Class organizations have begun to implement predictive maintenance, which is designed to determine the operating conditions that indicate when maintenance should be performed. Assets are maintained based on data collected from expert observation and monitoring equipment. Predictive maintenance is performed before downtime occurs and only when needed, instead of at set times when equipment is shut down as with preventive maintenance. Predictive techniques reduce asset downtimes, inventory costs and labor demands. One difference between preventive and predictive maintenance is the timing of the activities being conducted; with the preventive strategy, tasks are completed while the equipment is shut down, while predictive maintenance is carried out in normal production modes. While a predictive strategy can be initiated with a simple approach of performing and recording visual inspections to detect impending problems, data which is electronically recorded can be analyzed to glean valuable information about an asset’s performance, which can then be used to continually improve the asset’s maintenance program.
As part of their maintenance strategy, companies must also take into consideration the retiring workforce that is maintaining those aging assets. According to industry surveys, almost 3.5 million manufacturing positions will need to be filled over the next decade as baby boomers retire, and it is anticipated that 2 million of those jobs could stay empty. New employees entering the maintenance workforce do not have the institutional knowledge to determine if maintenance is needed or know how to best perform the maintenance tasks, particularly on the more tricky components. EAM systems can be utilized to mitigate this workforce gap in several ways. Collecting machine data and supporting predictive maintenance strategies can play a large role in filling that gap, by reducing the maintenance workload to only address known pending failures. Best-In-Class companies are addressing the aging workforce by equipping new employees with operator training modules and detailed work and safety instructions which are applicable to the specific asset and type of work being performed. To be effective, these materials should be available to the employee at the point of work, ideally provided via a mobile solution. This investment in material development and accessibility can ensure that best practices already embedded in asset management systems are effectively transferred to new and inexperienced employees.
Visibility — 'An Investment in Knowledge Pays the Best Interest'
The best decisions are made when all of the important information has been considered. Unfortunately, many enterprise systems operate in silos. Integrating the EAM solution with ERP software provides manufacturers the ability to streamline maintenance operations through better planning and scheduling of production and maintenance tasks. An integrated solution offers enterprise-wide visibility of the complete asset lifecycle, from the design phase to the final disposition. Integration also allows manufacturers to connect their maintenance applications with higher-level business systems more easily which in turn results in increasing responsiveness and an ability to make quick and intelligent asset management decisions. Also important for an effective asset management strategy are the adoption of asset analytics, dashboards and alarm management modules to automate data collection, analyze and monitor asset data, and escalate adverse events to appropriate decision makers at the right time and in the right format to prevent equipment failure.
Mobile solutions have become a key component in the overall strategy, as mobility improves bi-directional data quality which is important to continuous operational improvement initiatives. By equipping employees with mobile devices to record the results of equipment inspections and maintenance work performed, the manual data entry process is eliminated, resulting in time savings, more data being collected, and fewer data collection errors. Best-in-Class companies are 56 percent more likely to utilize mobile devices to provide the valuable information needed to perform the work such as instructions, safety checklists, hazard materials data sheets, inventory availability and access to prior work history.
Conclusion
Efficiencies realized by effectively managing labor, inventory and other support services directly impact the bottom line by helping control costs. Effective asset management practices and systems can result in significant benefits — cost savings, operational efficiencies, increased asset reliability, longer asset life and increased safety. Also, sustainability benefits should not be overlooked. By maintaining energy and emissions, the Best-in-Class companies not only reduce operational costs but also put themselves in a better position to comply with future environmental regulations and to be viewed as environmentally conscious.
As asset management becomes more predictable and more visible, the organization can begin to focus on other areas for continuous improvement.
Kay Jenkins is director of AssetPoint, a CMMS/EAM solution, at Aptean