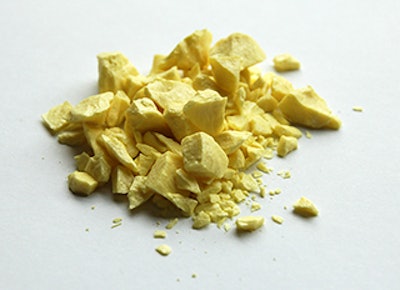
As a part of April's focus on Environmental Controls, Chem.Info sat down with Matthew Hodson of Principal Technology to talk about sulfur recovery as a vital part of any oil or gas operation.
What Prompts A Facilty To Need A Sulfur Recovery Unit?
Natural gas and oil producers, processors and refiners incorporate sulfur recovery units into their overall plant processing systems to reduce environmental sulfur emissions (in the form of sulfur bearing compounds like hydrogen sulfide and sulfur dioxide) and to ensure compliance with their operating permits, federal and state regulations. The oil and gas produced from sulfur-containing formations is often referred to as "sour" and is traded at a discount when compared to "sweet" oil and gas because of the additional processing required to remove the sulfur compounds.
In addition to being harmful to humans above threshold concentrations, if not removed, the sulfur compounds would remain in natural gas and refined petroleum products. When end users burn products containing sulfur, either as fuel in engines or natural gas for heating and industrial processes, the sulfur compounds are emitted into the environment as sulfur dioxide, a precursor to acid rain. Most environmental emission regulations related to sulfur are promulgated from the Federal Clean Air Act, The Environmental Protection Agency (EPA) and related federal regulations. One of the most recent sulfur regulations, and one that is visible to most Americans, is the Ultra Low Sulfur Diesel requirement, which limits the amount of sulfur in on-highway diesel fuel.
The requirements for sulfur recovery and emission limits are often specific to both state regulations and the type of process. Natural gas processing facilities, as an example, have different requirements than petroleum refineries. These differences are often based on the implementation of the required regulations by the states, the type of facility operated by the owner, and the different types of processing units operating inside the plant. Facility owners work very closely with consulting engineers specializing in the permitting process, their internal environmental experts and the state to establish the emission requirements for a new plant or process or significant changes to an existing process.
Can Sulfur Recovery Save A Facility Money?
Sulfur recovery units are inherently low energy consumers, especially when compared to other gas processing and refinery processes. During normal operations a traditional sulfur recovery unit can be a net-producer of medium pressure steam, which can be used in other parts of the plant, while only consuming a nominal amount of electricity required to operate pumps and blowers. The amount of plant utilities consumed and steam produced by the sulfur recovery unit is heavily dependent on the size of the plant and the type of oil or gas treating process.
Implementation and operating strategies for sulfur recovery units are heavily driven by the need for reduction in sulfur environmental emissions. While the elemental sulfur produced from a traditional sulfur recovery unit is a salable commodity, because of its abundance and transportation costs, the sales value rarely contributes significantly to the bottom line of plant operations. A poorly designed, maintained and operated sulfur recovery unit, however, can have a significant negative impact on operations through curtailed throughput caused by sulfur unit shutdowns.
What Can A Facility Do With The Recovered Sulfur?
Traditional sulfur recovery units produce high quality elemental sulfur in either molten liquid or solidified form. Depending on market conditions, location of the sulfur recovery unit, and transportation costs, elemental sulfur produced from plant operations can be sold as a feedstock for other industrial processes. Because of its relative abundance, and the transportation costs to haul elemental sulfur from remote plants, operators sometimes must bear the additional cost to transport this byproduct of oil and gas processing to larger markets.
Because sulfur is an essential plant nutrient, it is widely used in agriculture, from soil augmentation directly or as a feedstock to fertilizer production. It is the primary source to produce sulfuric acid, the world’s most used chemical, employed in many processes in the chemical and manufacturing industries. For road construction, sulfur asphalt is a viable alternative for asphalt road binder, while sulfur concrete is a relatively new corrosion resistant material that performs very well in harsh environments. Sulfur has numerous commercial and industrial applications and is used in many textiles, rubber products, daily household products – such as detergents, paints, paper and carpets, in pharmaceuticals, and even in cosmetics.
Matthew S. Hodson, P.E. (Texas), is president and CEO of Principal Technology Inc., a provider of total system solutions for natural gas, refining, chemical, process and manufacturing facilities based in Plano, Texas. Information on Principal Technology’s capabilities and services is available at www.principaltechnology.com. Contact Matthew Hodson at [email protected].