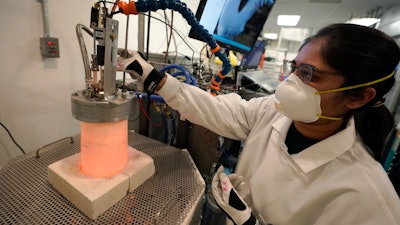
The manufacture of "green steel" moved one step closer to reality Friday as Massachusetts-based Boston Metal announced a $120 million investment from the world's second-largest steelmaker, ArcelorMittal.
Boston Metal will use the injection of funds to expand production at a pilot plant in Woburn, near Boston, and help launch commercial production in Brazil. The company uses renewable electricity to convert iron ore into steel.
Steel is one of the world's dirtiest heavy industries. Three-quarters of world production uses a traditional method that burns through train loads of coal to heat the furnaces and drive the reaction that releases pure iron from ore.
Making steel releases more climate-warming carbon dioxide than any other industry, according to the International Energy Agency — about 8% of worldwide emissions. Many companies are working on alternatives.
The financial package by global steel giant ArcelorMittal is the biggest single investment made to date by the firm's carbon innovation fund. Microsoft is another investor.
Tadeu Carneiro, CEO of Boston Metal, said its technology is "designed to decarbonize steel production at scale" and would "disrupt the industry."
The company's technology was developed at the Massachusetts Institute of Technology. Professors Donald Sadoway and Antoine Allanore, experts in energy storage and metallurgy respectively, are the founders.
Instead of burning coal, their process runs electricity through iron ore in a metal box or "cell" the size of a school bus to separate the iron from the oxide. Operators then collect the liquid iron from the bottom, Carneiro said. Boston Metal said it can eliminate all carbon dioxide from its steel production and hopes to ramp up production to millions of tons by 2026. As a bonus, it said, it is able to extract metals from slag normally considered waste.
Steel is in the early stages of a transition to cleaner processes that have less impact on the climate. Many major European steelmakers have announced alternatives to traditional coal-fired steelmaking and some automakers are buying the cleaner steel to fulfill promises to shareholders and customers.
By far the most steel is made in Asia. Both China and Japan have made moves in the direction of cleaner steel.
In the United States, most steel is already cleaner, because it is made by melting down old steel, for example junked cars. That can be done in electric kilns and emits a fraction of the climate-changing gases as virgin steel production.
It will be years before steel is cleaned up on a mass scale, Carneiro said. "It takes time to develop and scale up and get traditional and conservative industries to change things."
Several industry alliances are working to speed things up. A non-profit called ResponsibleSteel, for example, brings together stakeholders from up and down the supply chain — mining to finished steel products — to cooperate on cleaning up steel.
In related news, on Thursday, U.S. steelmaker Nucor announced it will start making heavy grade steel at a new $1.7 billion mill in Brandenburg, Kentucky, using electric furnaces to make new steel from scrap. The company says the product is intended for the offshore wind industry.
Offshore wind is key to many plans to address climate change, because it partially replaces fossil fuel-burning electricity. It will require massive amounts of steel as turbines are built miles offshore from U.S. coastlines. Nearly 90% of an offshore turbine's weight is steel, and each one, including the foundation, requires roughly 180 tons of steel per megawatt, according to the industry group American Clean Power.