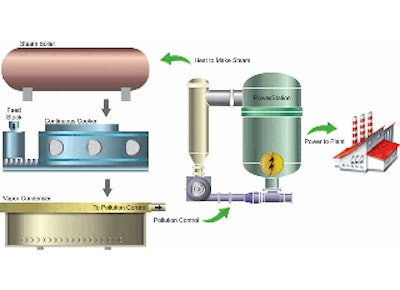
Animal Rendering Processing Introduction
There are several types of animal rendering plants and systems, such as wet, dry and edible rendering. Moreover, the designation of a rendering plant is typically based on the predominance of a specific animal, which is commonly paired with the plant’s location. Some product designations are:
- Poultry by-products, Poultry meal, Poultry fat
- Meat by-products, Meat meal, Beef fat
- Fish meal, Fish oil
- Yellow grease, Fatty acids
- Beef or Mutton Tallow
There are approximately 205 rendering facilities (http://www.nationalrenderers.org/) in the United States and Canada. These plants create a variety of products that are critical to specific industries. Some rendered co-products include:
|
|
|
|
Ener-Core in the Rendering Process
Ener-Core, Inc.’s Power Oxidization or PowerStation technology provides a unique opportunity for rendering facilities in that it can abate these odorous, low-BTU gases, while also producing electricity and valuable heat energy.
Most rendering facilities have an early processing step that includes a batch or continuous cooker(s). The continuous cooker is an agitated vessel generally heated by steam from a gas-fired boiler. It brings the raw material to a temperature between 240º and 290ºF which evaporates moisture and frees fat from protein and bone. The cooking process is also a large contributor to odor emissions.
Odor control is one primary air emission concern that is faced by rendering facilities. In most applications, the odor abatement is handled by a regenerative thermal oxidizer (RTO) or a direct-fired thermal oxidizer (TO). Ener-Core can take the exhaust from the cooker(s) or from the vapor condenser(s) and use it to make power and steam while abating the odors.
The Ener-Core Process
The Ener-Core process starts with pressurizing the waste gas and the supplemental fuel before sending them into a heated pressure vessel. A ceramic bed within the vessel hosts an exothermic reaction and retains the heat energy maintaining a self-sustaining reaction. The energy that comes out of the oxidizer is paired to a turbine to generate electricity, all while producing near-zero nitrogen oxide emissions (NOx). The system does not use any catalysts, and it manages to accelerate the natural oxidation reaction (which typically takes 10-20 years for methane in the atmosphere) such that the entire reaction takes place in approximately two seconds.
The PowerStation effluent delivers an ultra-clean exhaust that not only generates roughly 1.8 megawatts of power capacity but can also steam via the integration of a waste heat boiler. The Ener-Core PowerStation operates flamelessly, which means the NOx emissions from the overall cooker process is reduced substantially lowered from boiler offsets.
Conclusion
Two significant sources of rendering costs are: 1) energy, and 2) environmental compliance and odor control. Most rendering facilities spend a significant amount of their operating budgets on energy and treatment equipment for air and wastewater effluents. Energy is typically the single highest-cost element within the overall operating cost structure of most rendering facilities, and can represent as much as 50 percent of the overall operating costs.
Most forecasts indicate that electricity prices, and even natural gas prices, will rise in the coming years, and the rendering industry will feel the impact of rises in energy prices even more significantly than most industries, given the significance of energy costs within the industry’s overall operating costs. Similarly, the standards on air quality emissions are expected to continue rising over time, which may also have an impact on the operating costs of rendering facilities. Ener-Core’s technology enables the rendering industry to hedge against these future increases in energy costs and increases in air quality standards, and lower their costs by utilizing their air emissions as a source of their on-site power generation.
Natasha Solouki is Executive Assistant in the Sales Department and Mark Owen is Director of Sales at Ener-Core, Inc., the world’s only provider of commercialized Power Oxidation technology and equipment that generates clean power from low-quality and waste gases from a wide variety of industries.