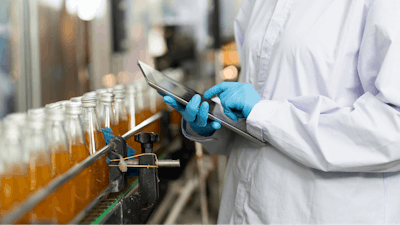
The capacity of AI is ever-expanding, but it was generative artificial intelligence (Gen AI) tools such as ChatGPT that swept up a consumer storm and are already being implemented in industry settings.
While some pundits had Gen AI touching every facet of working practices, in reality it is now clear to see some defined and valuable use cases coming where Gen AI can be seen as a major productivity tool. Nowhere more so than in process manufacturing settings for workers on the food and beverage factory floor.
The new AI-connected food and beverage worker is helping solve skilled labor shortages and making blue collar work appealing for Gen Z.
A large serving of AI for the food and beverage industry
Faced with a shortage of skilled workers, attracting Gen Z workers to the food and beverage manufacturing shop floor, which has traditionally been seen as dull, dirty or dangerous (the three Ds of manufacturing), has proven an ongoing challenge. Then along came Gen AI, with new tech such as AV and VR that has transformed the traditional shop floor into a productive, and cool, place to work.
U.S. food and beverage manufacturers need to work to the highest standards. With global AI in food and beverages market size being calculated at an all-time high of $15.36 billion in 2025 and growing exponentially over the next decade.
That means training and reskilling frontline workers with different levels of knowledge, competence and language issues is vital while keeping practices health and safety compliant for the new tech-enabled manufacturing era. Enter Gen AI and the new generation of connected worker platforms, where content creation and delivery are in their DNA.
Not only is Gen AI in food and beverage manufacturing a win for workers, but it is also a win for CPG companies globally, where Gen AI use cases could increase the economic impact of traditional AI by 15% to 40%. McKinsey estimates bridging that gap means unlocking an additional $160 billion to $270 billion annually in profit and part of this can be achieved through an enhanced workflow among increasingly connected workforces.
Food and beverage manufacturers bite off more than they can chew when providing vital training content
Food and beverage manufacturers with little AI experience can start small with a simple early-stage test on a product line for anomaly detection or even look beyond their equipment to support schemes that expand as far as training and workforce development.
From checklists and skills, to procedures and knowledge transfer, content creation isn’t a one-stop-shop. And with costs, inflation and geopolitical uncertainty on the rise, taking workers away from their duties on the shop floor to create content is becoming a no-go area for management.
Creating content isn’t the only hurdle to overcome. Arguably, facilitating content retrieval on the shop floor is an even greater challenge.
From the device to the shop floor: The value of AI in retaining an inspired frontline
Bringing new technologies, such as connected worker platforms and Gen AI to the shop floor is transforming the dark and dirty shop floor into a more engaging workplace that is revolutionizing food and beverage manufacturing.
The food and beverage manufacturing industry are grappling to attract a younger workforce, which is an area of recruitment where Gen AI may prove useful. But as more manufacturers aim to recruit Gen Z workers, it’s essential to ensure all instructions are available on digital platforms.
Gen Z workers are more familiar with the adoption of AI through the tools arising through and around their education, meaning they would be more susceptible to working amongst AI support systems.
Younger workers are tuned in to search for answers and instructions digitally, so making content available digitally is critical to retain these workers and empower them to take ownership of their role, a growing necessity for the younger workforce, especially in the food and beverage processing industry.
AI is empowering food and beverage workers to work smarter, not harder: Buy-in is key
One of the largest obstacles the food and beverage manufacturing industry encounters is not only the capability to recruit empowered frontline workers, but also to retain them. Technology holds the answer.
Regardless of skill shortages, food and beverage manufacturers need to communicate to their staff about the value of these AI tools and explain just how their adoption is implemented.
Here’s what these AI tools can achieve to sustain and inspire the food and beverage workforce.
1. AI aids workflows with intelligent content transformation
Frontline workers in the food and beverage manufacturing industry need content that can be easily and quickly understood and assimilated. That means it needs to be in multiple formats such as text-based instructions, but creating all this content takes a lot of time and capital.
And it’s not all about new content. CPG factories will already have thousands of existing content files such as standard operating procedures and work instructions but converting each one into an easily accessible location is also costly and time intensive.
According to a global Lenovo survey of 600 IT leaders, 79% feel AI will free employees to focus on more meaningful work, which is key in the food and beverage processing industry where deadlines are tight and produce has a shelf life. The full value of connected worker solutions can take time to materialize due to the time and effort required to import and build the required digital work instructions into the platform.
2. Delivering work instructions in multi-media form
Streamlining the creation or conversion of each type of content using AI-powered content transformation will drastically reduce the amount of time it takes to provide digital or written instructions in one secure location. The ability to convert documents in a matter of minutes, into easy to comprehend Digital Work Instructions from lengthy, written standard operating procedures, will reduce deployment times, allowing for faster time to value.
Video is fast becoming one of the most consumed forms of content, especially for Gen Z. In fact, 57% of Gen Z-ers prefer to learn about new products by watching short-form videos.
So when it comes to creating digital work instructions, companies shouldn’t overlook the power of video to improve user engagement. But creating video-based instructions for shop floor workers is a challenge particularly for factories that lack sufficient financial and human resources.
But AI-powered video instructions changes all that. It can pull out relevant information and sequence it into structured written steps. Images can also be helpful to provide visual context at each step. AI in digital work instructions for food and beverage manufacturers can take the form of several user-friendly components.
Workers can access a step-by-side visual guide on how to carry out a task. This helps to improve troubleshooting as operators can access a broader library of content. Younger workers can also benefit from the knowledge of senior operators in a way that engages them and meets their new workplace expectations.
3. Tearing down language barriers with multilingual transcription
Immigrant workers account for 2.92 million manufacturing workers in the U.S., and the majority of these workers will not speak English as their first language.
Despite this, most global food and beverage manufacturers struggle to ensure that critical operational content is available in all the languages of their diverse workforce. AI-powered transcription can break down global language barriers and encourage worker inclusion, by translating all types of content into the required language.
What makes AI-driven transcription useful over human translators is speed. Gen AI tools can translate recordings in a matter of minutes as opposed to hours. This is an intelligent capability that automatically translates the audio from videos into relevant subtitles in the preferred language of the user.
Not only does this reduce the effort to create and maintain content, but it also improves the comprehension and retention of information leading to better safety, quality and productivity on the shop floor.
4. Intent-powered search to meet user demands
Concise communication and comprehension are key to helping improve worker and team productivity. When you’re working in a fast-paced and loud manufacturing environment, errors are naturally going to happen.
But what if workers had a tool that could intelligently interpret the user's input and beautify it by automatically improving its grammar, vocabulary and punctuation to ensure optimal readability?
AI can empower workers to work smarter, not harder by providing them with intelligent search capabilities that not only grasp their inquiry's intent, but also adapt to human nuances like typos or vague terms. This ensures quick and accurate responses to inquiries like how to troubleshoot a broken mixing machine with a jammed mechanism. AI makes sure they are presented with the right information at the right time.
One of the first things Poka did this year was add embedded AI semantic functionality to improve their internal search engine on the Poka app, making it easier for users to find the content they need without needing to scroll through an entire content library, wasting valuable time on the frontline.
A new “Ask a Question” functionality, enabled by Gen AI, takes this search capability one step further to empower workers on the shop floor. Users can skip the time-intensive process of sifting through pages of information and instead use Poka to find specific answers in a faster and more intuitive way.
This information sits within the knowledge articles created by the customer and will be referenced when searching for answers to eliminate any AI misinterpretations.
Transformative power is in the AI of the beholder
The U.S. processing manufacturing industry’s future is intertwined with long-term integration AI, and Gen AI is here to help in the functions of food and beverage manufacturing, including as connected worker platforms. While different technologies continue to expand, so does the number of food and beverage manufacturers embedding or looking to embed AI into their processes.
The connected worker is living proof that Gen AI’s ability to enhancing job skills and support other training and development can walk the walk within food and beverage manufacturing practices.