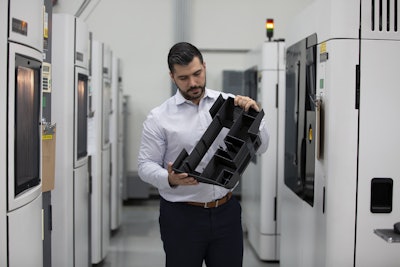
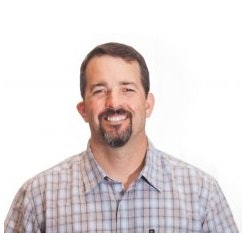
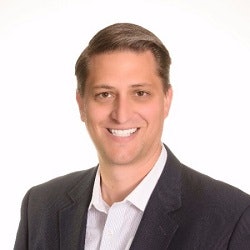
Predictions at the start of 2018 indicated that it would be a year of growth for the manufacturing sector. Additive manufacturing specifically had indications of industry-growth at a grounded level – less focus on grand innovation and more practical steps forward by enhancing the technology and introducing more versatile materials.
For Stratasys, a company that both produces additive technology for in-house manufacturing operations and offers custom manufacturing services through Stratasys Direct Manufacturing, it was an especially critical year of producing practical advances in technology and a consistent parts manufacturing output.
A year later, Stratasys looks to 2019 and the evolutions manufacturing will experience at the end of a decade. Scott Sevcik, the VP of manufacturing solutions at Stratasys, and Kent Firestone, CEO of Stratasys Direct Manufacturing, speak to their predictions for additive manufacturing in 2019.
What do you think will be the biggest change/evolution in additive manufacturing in 2019?
Kent Firestone:
One of the things we’ll start to see more and more is the use of additive parts in structural applications. That’s mainly going to be led by additive metals. Improvements in additive metals technologies and materials will expand current capabilities and open up additional opportunities for implementation of structural additive parts.
As service providers push more into serialized production, we need to adopt a lot of the processes and software that traditional manufacturers are using. Any kind of improved monitoring on additive machines and industry standards will help to drive wider adoption. There has been a lot of work going on over the last few years in trying to create standards for the AM industry. They are typical in a manufacturing environment, so to grow additive towards that next step in manufacturing, standards are critical.
Scott Sevcik:
We’ll definitely see more adoption of standards. We have major OEMs and tier one suppliers that have moved beyond initial qualification and are driving their specifications down into the supply chain aggressively. As these OEMs begin to share the extent of this publicly, we’re likely to hear some pretty staggering numbers of production parts, particularly for aircraft, that have already been printed, certified, and are flying today. But, the real sign of industrial readiness we’ll see is that we’ll take the first major steps from customer specs to standardization.
We’ve worked with the National Institute of Aviation Research for over a year to fully characterize our process. This is leading to a publicly accessible design data set, which has in turn led to interest in international specifications. Specifically, there is an SAE International specification coming that will be used to drive consistent performance with FDM. For years we’ve had customer specs and customers locking down processes, but now, because of the work we’ve done to enhance process repeatability, we’re finally moving into a phase of maturity where the industry is adopting a standard. We’ll have something that can become common across suppliers and supply chains for the first time.
Speaking of data, how are analytics and cloud-based processes impacting manufacturing? Do you feel that additive is behind?
Scott Sevcik:
There is an industry impact today with more databases and more data being collected. There’s a lot of scrutiny on how the industry is using the data collected. Now that we have so much data to work with, we’re going to start zeroing in on the real benefit of the data.
Additive manufacturing is way behind in this regard. If you look across the industry, there is almost no additive equipment that will interface with a MES (manufacturing execution system) or MOM (manufacturing operations management) system and bring data off the platform for use in process control, process monitoring and manufacturing planning.
At Stratasys, we took our first step this year by adding the MTConnect interface to our third generation F900 launched in the summer of 2018. It’s one of the first pieces of additive equipment that has the ability to stream process data off the system during the build. This type of interface and data architecture is critical for customers who are shaping their factories toward a digital future.
Kent Firestone:
AM should rise to the manufacturing level to be considered a production process. The cloud is where a lot of data and equipment are moving to, but one of the issues with the cloud is customer confidentiality of files. That’s something we should be cognizant of as our industry moves to where the rest of the world is going – we have to figure out ways to protect our customers' data.
What is 3D printing’s place in embedded intelligence and Industry 4.0?
Kent Firestone:
3D printing has a place in the “just in time” manufacturing realm in Industry 4.0. One of the primary focuses of Industry 4.0 is the connectivity of the machines, and additive machines are capable of that. It’s up to the OEM suppliers of additive manufacturing equipment to enable them to participate and connect in that kind of environment.
Scott Sevcik:
In production, the fact that a part is produced additively needs to ultimately disappear into the background. From an industry 4.0 standpoint, it needs to behave like any other technology in order to make it as easy to adopt as possible. Our next-generation equipment has to be designed, not for the factory of the 80’s, but for the factory of the 2020’s.
On the other side, we are a cornerstone enabler of elements of that digital factory future. The tool-less production capabilities that you get from additive manufacturing allow for distribution of production. The speed at which you can continue to improve products is an enabling capability that 3D printing brings into that digital environment. It’s not only being able to move that data around, but being able to do something physical with that data.
Is there a limit to precision manufacturing with additive? Do you think we will ever reach the same consistency as IM&T or CNC machining?
Kent Firestone:
From what I’ve seen, currently and over the last 25 years, I’d say yes there is a limit. We continually get better and better, but there are fundamental differences in the technologies. You can program a cutter-path on a CNC machine much more precisely than you can build a part in an additive process, whether it be plastics or metals. Today, we’re not there; long term, it will be a challenge for additive to get to the same point as CNC machining in terms of accuracy. However, additive has a lot of benefits that you can’t get with traditional manufacturing. To me, it’s a balance. You have to use additive where it makes sense.
Scott Sevcik:
Additive isn’t one technology; there are additive technologies that are very good at high-detail precision and other technologies that are better at mechanical properties. The right uses of different technologies, both additive and subtractive, will come down to best fit, application by application.
Will a bulk additive plastic process ever be more accurate than CNC? We’ll see. From a geometric standpoint, we won’t see it soon. There are a lot of thermodynamics at play. But we have now seen a thermoplastic additive process demonstrate mechanical properties and repeatability on par with traditional technologies, and just a couple of years ago, no one was predicting that. So, I’ll be the cautiously bullish one.
Regardless, we are far from being done in advancing these technologies. There are 30-year-old additive technologies that are hitting their stride, but with major advances still to come, and there are 5-10 year old processes that still have immense upsides as the processes become better understood and controlled. While we will continue to improve, enabling new part types and changing supply chain economics, there will always be applications and parts and properties that are going to be better served with the traditional technologies.
Additive adoption will ultimately be driven by the parts it can enable and the economics it can change, the cool factor of the fact that those parts are produced by an additive, rather than a traditional, technology will eventually fade into the background. Hopefully, in 2019, we’ll see the thinking mature as well and more and more recognition that additive is a new set of tools in the toolbox, not a one-size-fits-all replacement for a few hundred years of industrial process development.