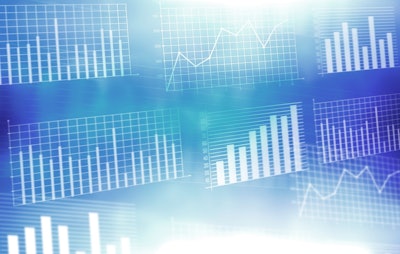
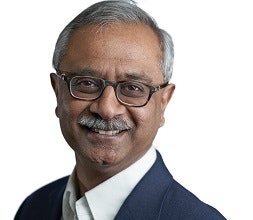
The goal of a poka yoke mechanism is to make it nearly impossible for workers to make a mistake. More specifically, it ensures that mistakes within the process are immediately visible, so they can be eliminated at the source.
The challenge of poka yoke is the time and effort it requires to implement, program and maintain, as well as needing to eliminate the flaws of existing methods of data collection and observation.
Manufacturing technology on the horizon promises to transform poka yoke by disrupting many of the elements that make the value it delivers so costly to achieve.
In this article, I’ll lay out four benefits of the coming age of new factory technology that could be applied to simplify and accelerate poka yoke. But before I do that, I want to explore what it is that makes traditional poka yoke so challenging to perform at scale.
The Rewards (and Costs) of Poka Yoke
The magnitude of the effort it takes to implement poka yoke speaks to its enormous value: a factory can benefit significantly from even the smallest gains in productivity and quality. But poka yoke is also self-limiting in the sense that the overhead required by some of the activities listed below makes the undertaking impossible—and makes the status quo more financially attractive than optimization.
First, it takes a lot of effort. Think of all of the overhead required by any one poka yoke solution:
- To start, you must quantify whether a problem exists.
- Then, you must prove that the problem is worth solving given all the other competing challenges you’re faced with.
- Then, you must spend hours or days on the line, painstakingly observing and measuring the status quo.
- Then, there’s the effort of crafting the solution—which could be as simple as a new fixture in a workstation, or as complicated as a redesign of a component part to prevent an error-prone state from being physically possible.
- And, finally, programming the specific logic of the solution while interfacing with existing fixtures and devices, including light curtains, interlock switches, safety mats and power guards. Programming this Rube Goldberg-like system is often done using PLCs (Programmable Logic Controller) and ladder logic—neither of which are easy to master (see Figures 1 and 2), and both of which predate 3rd and 4th generation programming languages that have dramatically sped up the software development process.
Whichever path you choose, all of this often requires the re-alignment of people and materials throughout the organization.
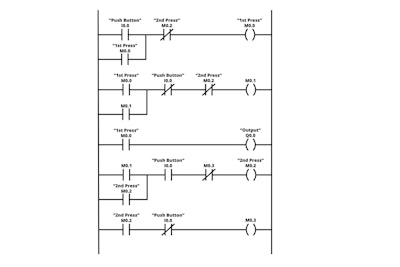
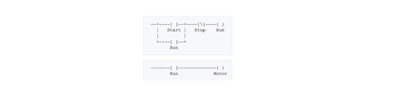
Then, you need to do more observation to confirm the solution creates value, and further refine the solution to perfect it.
And then the cycle starts over.
Complicating this is the observer effect (famously articulated by Werner Heisenberg in quantum physics as the uncertainty principle): the act of observation perturbs the system.
In the factory, the act of observing an operator at their workstation changes the way they perform their work. An operator under observation may subconsciously or deliberately change their style to impress or game the observer. Put plainly, you could spend days on the line and not even see the behavior you’re trying to fix.
When Technology Meets Tradition: Intelligent Poka Yoke
In an era of mass customization and ever-shortening times-to-market, the industry needs to accelerate poka yoke. Not by narrowing the focus, compromising the methods, or lowering our expectations, but by turning to technology to amplify these principles and accelerate the outcomes.
In particular, there are four areas where newly available technology which automatically gathers and analyzes data from human activities will help.
- Identifying the most important steps for optimization. Every poka yoke exercise currently begins with a question: Is this opportunity going to show return on investment (ROI) for the effort required to improve it? Intelligent poka yoke will arm the process engineer with the information that they need for every process element to more quickly identify the most important opportunities. Or, better yet, it will automatically reveal the best candidates for poka yoke—ones that align with key manufacturing KPIs like productivity and quality—before the engineer even thinks to search for them.
- Shortening observation times. What if the process engineer didn’t have to painstakingly perform days’ worth of observations? What if, instead, they could complement a much shorter observation period with data and video that was already waiting for their analysis? A hypothesis could be proven simply by analyzing data that’s already been captured.
- Enabling rapid experimentation. You don’t know if a poka yoke project is successful until you’ve measured the changed state—something that you can’t measure until you’ve implemented the change. Which means that no poka yoke project is complete until a post facto cycle of observation and measurement has been performed. Intelligent poka yoke, if it fulfills requirement #2, by definition allows you to perform more experiments in less time. Instead of pausing your second project to perform measurements on your first, you can let your tools gather data while you focus on the next improvement. This is the equivalent of the well-understood example of conducting A/B tests on your website: you simultaneously and rapidly iterate a site design to see which tweak—a different color here, a different image there—drives more revenue. Websites rapidly evolve to the optimal state; what if poka yoke could do the same?
- Eliminating the observer effect. If data collection is not a one-off event but instead a persistent practice, then operators won’t get nervous with the presence of an engineer on the line. In fact, as we have seen, it becomes a part of daily life and is ignored. This means that the data gathered will be more valuable not just because there’s a far larger sample size, but also because there’s less bias in the data collection methods. The result is more accurate data, which leads to better outcomes.
Hello, Intelligent Poka Yoke
Poka yoke has remained stubbornly manual because Industry 4.0 technology has been focused on machines and machine-driven datasets.
Industry 4.0 is effectively blind to the activities of humans, even though humans remain manufacturing’s biggest contributor to value and to variability.
The next generation of Industry 4.0 technologies will finally usher in true digital transformation in the factory by helping the human workforce increase the value they deliver—and accelerating the efforts of the engineers to reduce the variability they create.
The practice of poka yoke is about to get even more important because, with the next generation of tools, the overhead of poka yoke is poised to drop. When poka yoke can be built, applied and iterated at scale, minor improvements can cascade into major financial gains that may be felt as high as earnings per share.
Dr. Prasad Akella is the CEO of Drishti.