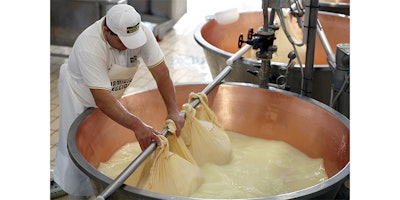
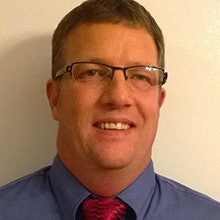
Like flour to bread or hops to beer, skilled labor is essential to food and beverage manufacturing. And supplies are quickly running out.
Across the U.S., producers are citing the lack of qualified workers as their most critical need to keep production lines operating at peak efficiency. Over one-third of respondents in a 2017 survey of food and beverage manufacturers said they planned to hire staff, and more than half are expanding their in-house training programs to improve the skill sets of their workers.
A second 2017 industry study, sponsored by Advanced Technology Services (ATS), found that the leading cause of unscheduled downtime within respondents’ facilities was aging equipment (42%), followed by operator error (19%) and lack of time needed to perform necessary maintenance (13%). In each case, the lack of trained personnel negatively impacts the situation, either directly or indirectly.
The skilled labor shortage is creating challenges across the manufacturing spectrum. Employers are forced to pay inflated wages to attract and keep the best people, while training costs for under-skilled workers eat into profit margins and depress investments in other areas of the business.
Without skilled labor, production is slowed and expansion is difficult. Many manufacturers believe the answer lies in moving facilities outside the U.S., where labor is plentiful and less expensive; yet all too often, companies encounter a culture shock when foreign employees are tasked with operating and maintaining highly complex equipment. The resulting need for training, at levels even higher than for domestic workers, offsets much of the anticipated wage savings.
Of all the core disciplines affected by the shortage of trained personnel, machine maintenance may be the most troublesome for food and beverage producers. Thirty-five percent of U.S. manufacturers are currently seeking maintenance technicians, and an even higher percentage are shifting at least some maintenance responsibilities to operating personnel — a dangerous tactic at a time when equipment is becoming increasingly automated and complex. One in four manufacturers, according to the 2017 survey, have decided to outsource their maintenance responsibilities to meet the need.
Regulatory requirements, combined with production efficiency, are helping drive the need for better maintenance. With enforcement of Food Safety Modernization Act (FSMA) mandates beginning in September, food safety is more critical than ever. Industry standards like the Global Food Safety Initiative (GFSI) and FSSC 22000 are also influencing controls and tolerances. Most companies understand the need for qualified technicians to keep equipment operating within the tight specifications these initiatives require.
As a result, many food and beverage companies are looking for automation and control engineers, maintenance techs and specialists in electro-mechanical and other disciplines. While these firms typically see maintenance as an operational expense, an increasing number — more than one-third in the ATS study — believe machine maintenance is actually a profit center that can deliver greater production capacity.
Perceptions of Manufacturing Jobs
There’s no doubt that the generational shift brought about by retiring Baby Boomers is a major cause of the skills shortage. But just as important is the fact that newer generations are not choosing machine maintenance as a career — a decision that is having profound implications.
Many young people simply do not envision a career that involves a factory floor. In the latest Career Interest Study of nearly 10,000 high school and college seniors by the National Society of High School Scholars, students were asked to rank their top 100 preferred employers to work for; Google, Walt Disney Company, Apple, the FBI and the CIA were at or near the top of the list, while Hershey’s and Coca-Cola were the only food and beverage manufacturers to crack the top 50.
Despite this, the top four factors graduates look for when choosing an employer are: “fair treatment of all employees,” “gaining skills to advance my career,” “basic benefits,” and “work/life balance,” according to the report. All four can be found in most food and beverage companies. Furthermore, given today’s increasingly computerized and automated factory environments, the opportunities for advancement among tech-savvy young people have never been greater.
Closing the Gap Requires Effort
With Generation Z — the cohort born in the mid-90’s and only now beginning to consider its career options — outnumbering the Millennial Generation by over one million people, the opportunity is ripe to begin closing the skills gap. Three interconnected strategies will make the difference:
Encourage a new vision. Parents, teachers, guidance counselors and entire communities need to be made aware of how different, more exciting and more rewarding manufacturing is as a career. What’s more, they must be convinced to take part in persuading this next generation of workers to consider pursuing a job in manufacturing.
Kids of all ages love to watch the manufacturing process; for proof, one need look no further than the appeal of the long-running Science Channel series, “How It’s Made.” Manufacturing careers, especially those positions that cross industry lines, give workers the chance to participate in making everything from airplanes to artificial heart values. And unlike the noisy, dirty environments of old, factories are cleaner and far more technical places to work than people realize.
Support training partners. Local trade schools and community colleges are the best development partners local food and beverage manufacturers can have. Most schools will tailor their programs to meet the demands of local employers; classes in electronics, hydraulics, mechanical systems, robotics, PLC and production automation are ideal for maintenance engineers and technicians.
And yet coursework leading to a degree is not essential. The Society of Manufacturing Engineers (SME), through its ToolingU training partner, offers two certifications that are in strong demand: Certified Manufacturing Technologist (CMfgT), providing a knowledge of controls, programming, continuous improvement and process design, will qualify a young person for an entry-level equipment maintenance position; while Certified Manufacturing Engineer (CMfgE), a more advanced designation requiring both education and work experience in advanced manufacturing, provides advancement for existing employees. Both certifications can be earned online through via one-hour classes done at the student’s own pace. Tests are administered online as well.
Be flexible. All too often, employers have blinders on when seeking employees with particular skill sets, believing prior food or beverage experience is critical. But specialized training is more transferrable than you think. Industries where there have been headcount reductions, for example, are fertile grounds for recruitment.
It also pays to broaden your criteria. Young people with limited experience, yet who exhibit an aptitude for mechanics or computers, can become productive very quickly with a little training. If a recent graduate passionately tinkers with go-carts, PCs or drones in their spare time, chances are that person will respond well to instruction.
There are many ways to create options for employee development. Tuition reimbursement and train-to-work programs give workers basic skills they can build upon; onsite training programs bring the classroom to the workforce, making training convenient for companies and employees alike. The best training companies can supply highly experienced instructors and curricula tailored to the company’s specific needs. Lunchrooms or other meeting areas are turned into temporary training rooms, with class times set according to any schedule — even third shift. Instructors can even bring in equipment identical to what is used on the line, ensuring transferrable knowledge.
There’s no question that the skills shortage affecting food and beverage producers is real and persistent. Yet manufacturers can play an important role in solving this challenge. By being proactive, clear, and upbeat about the opportunities to be found in today’s factory environment, it’s possible to restock the supply of talented young people interested in the field — and keep this key ingredient in the manufacturing mix well stocked, long into the future.