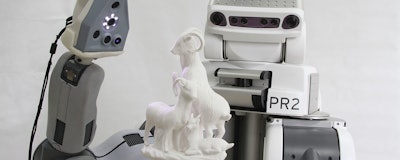
A company’s quality control team is only as good as the tools it has available to work with. Given this, handheld 3D scanning technologies have become essential for quality control operations within industrial settings. These technologies capture the geometry of a physical object and transform it into a set of data: a triangle mesh or point cloud. Basic metrology tools such as calipers and gauges are time-consuming, are prone to human error and result in less overall measurement information. Even Coordinated Measuring Machines have their limitations in terms of mobility and the size of objects that can be measured. 3D scanners offer the combination of speed, accuracy and large fields of view, freeing up valuable labor hours and offering flexibility into the quality control process.
Streamlining Operations Case-in-Point
Willman Industries Inc., a Wisconsin-based iron foundry that conducts design work, pattern making, heat treating and machining, is able to use 3D scanning to make sure that castings meet expected values. The company works with large castings that are upwards of 30,000 pounds. Casting layout, a check of dimensions against drawings and specifications, can now be done digitally instead of manually. Using a handheld 3D scanner, the casting is digitally captured and compared to the original CAD files. This process, which previously could have stretched over seven to 10 days, has been reduced to six to 10 hours.
“We’ve made numerous improvements to our process with it [the 3D scanner]. Our dimensional control has improved not just from measuring the castings but from checking multiple process inputs,” says Randy Parker, Willman’s quality manager.
The same concept can be implemented on a smaller scale for tooling. The forms used to make tools need to be periodically checked to make sure that the shape is still accurate after substantial usage. On a traditional production line, parts and finished products can be 3D scanned and compared to the original CAD designs to ensure that specifications are being met and there aren’t any deviations. Being able to conduct these measurements using software is a valuable practice for any industrial setting.
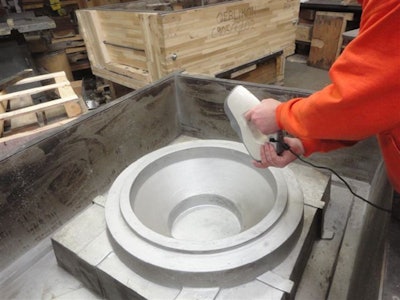
3D Scanning and Robotic Arms
Automated 3D scanning, using a robotic arm, has great potential within the quality control field. Due to the fast capture rate of this technology, it is well suited for quality control checks on a conveyor. However, in order to implement this technology into everyday operations, it is important to understand how the technology works — starting with modes of operation.
Some 3D scanning solutions allow for capturing in autonomous mode, where the scanner and robot arm can scan an object without a pre-programmed trajectory. The software can play a key role in achieving best results in this mode, analyzing the surfaces being scanned to determine if all necessary data has been captured and, if necessary, rerouting the scanner to fill in missing data. This mode is particularly useful for scanning large sets of objects of different shapes and sizes.
Automated 3D solutions will commonly also offer a programmed mode of operating, effective for scanning the same class of objects in large quantities. Some technologies are easier to program than others, with a few even allowing the user to physically guide the scanner around the object, "teaching" it the path to follow.
Adding Artificial Intelligence Into the Scanning Process
3D scanning is most easily employed in areas of quality control where there are clear yes/no criteria. After an object is scanned, do the dimensions match the ideal model that is on file? In future, the ability to judge pass or fail will be integrated into the scanning device itself. However, an area where there is even greater potential is combining 3D scanning with artificial intelligence (AI)for scenarios that require more “subjective” decisions. Technology such as the NVIDIA Jetson supercomputer on a module is significantly enabling the development of such applications of 3D scanning.
Indeed, the most exciting applications will be those where the criteria are not easily definable and the embedded computer needs to be taught to make these decisions. Let’s say a plant is manufacturing car seats. One quality control measure may be focused around ensuring that the seams of the seat are straight, or straight enough. These decisions are typically made by a person who can judge by eye that a seam appears to be acceptable. The quick mental calculation that can be done by a person is more complicated for a machine. With AI-based 3D scanners, these decisions can be analyzed and “subjective” decisions can be produced by the device using set parameters.
Another scenario where this type of decision flexibility could be very useful is in the aerospace sector. AI based 3D scanning can be used for the dent inspection of airplanes, identifying and measuring impressions that may not be easily recognizable by the human eye alone. The scanner would be passed over all external surfaces of the airplane, detecting any dents and, with the use of AI, would decide which need to be addressed in the immediate future and which can be simply monitored for the time being.
The use of 3D scanners in industrial quality control is already streamlining operations for the innovative companies that have embraced the technology. However, large-scale adoption, and solutions that marry 3D scanning with automation and AI, will continue to help improve the accuracy and lower the time investment required for this practice. While the industrial sector has granted a lot of its attention to 3D printing technologies, 3D scanning will and has been just as important.
Andrei Vakulenko is Chief Business Development Officer at Artec 3D.