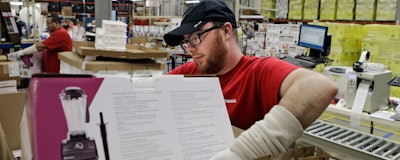
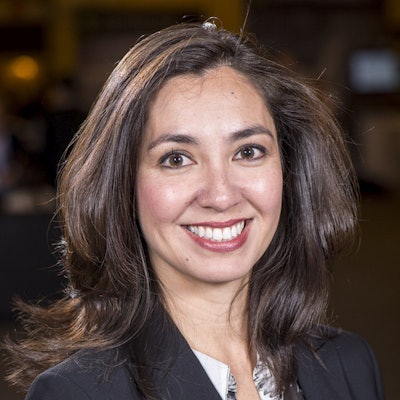
There are a number of substantial challenges facing the global manufacturing industry, including speed of product development, innovation and a considerable skills gap in the workforce. Manufacturers are consistently challenged to find the right talent to accommodate growth and keep their operations running smoothly.
According to research from Deloitte, within the next 10 years, nearly three and a half million manufacturing jobs need to be filled. The widening skills gap is expected to result in two million of those jobs remaining vacant. Major factors contributing to this shortage of experienced workers include natural business growth, retirement among baby boomers and a lack of science, technology, engineering and mathematics skills. In addition, manufacturers are faced with ever-increasing competition and higher pressure to innovate.
Employees are the lifeblood of any company. In the coming years, it will be critical for manufactures to harness employees’ collective knowledge and use collaboration for both employee training and innovative product development to keep growing their businesses.
The following tips on collaborative learning and product lifecycle management can help manufacturers effectively design, develop and collaborate on products, as well as train, develop and increase satisfaction among their workforce.
Encourage Continuous Learning
Learning should be an essential part of the culture of a manufacturing organization. However, as the workforce has grown, manufacturers have been challenged to find scalable methods to bridge the skills and knowledge gaps. Embedding cloud-based collaboration technologies within an organization’s business and learning processes provides simple ways to create, share and discover learning content and connect with colleagues using tools and methods they are already familiar with.
Manufacturers must adhere to the laws, rules and regulations of the countries in which they operate, as well as the countries in which their customers operate. Collaboration technologies may help manufacturers adhere to legally-mandated compliance and/or training goals, or an organization’s internal code of conduct.
To promote course offerings required for regulatory compliance, organizations can integrate learning management systems into learning communities. Considering the cost of developing formal learning content, the greater the adoption of course offerings, the better the ROI.
With social collaboration technology, employees have a space to ask instructors, experts or other peers to clarify, discuss and reinforce understanding of information or processes well beyond the initial training. Global organizations that leverage social collaboration platforms frequently report increased information-sharing and cross-office collaboration.
Collaboration technologies can also provide rich content and experiences for onboarding and up-skilling employees. With an internal repository for information, teams or departments may also avoid repeating mistakes that have been made in the past.
Connect and Streamline Critical Business Functions
According to a recent survey from IDC, companies may lose as much as $30,000 per employee per year due to inefficiencies in everyday tasks, including reading and responding to email and searching for and gathering information.
In a small office, employees might already be versed in the activities that everyone else is working on and which experts to ask for help. However, with larger and global organizations, finding the right expert to consult may be a daunting task.
With a social collaboration platform, experts can quickly and easily create, share and make documents available to employees across their network. In addition, search tools, activity feeds, tags and featured content capabilities make it easy for employees to locate the content or expert they are looking for.
According to a recent survey by Strategy Analytics, mobile workers comprise nearly one-third of the total U.S. workforce. As such, it’s important to ensure workplace technologies are accessible by mobile workers, as well as those in different geographies.
Harness Knowledge
Many manufacturers risk substantial loss of knowledge due to movement and career shifts of skilled workers. With retirement among boomers expected to substantially increase by 2020, and the shortage of skilled workers to take their place, global manufacturers must preserve knowledge and skills to ensure business success down the line. This includes both development of expertise through sharing knowledge as well as capturing this information in an easily accessible and consumable way for future employees.
Incentives are frequently overlooked by manufacturers large and small. Manufacturers can encourage knowledge-sharing among highly-skilled workers by leveraging a variety of communication formats, such as videos, blog or Intranet posts or question and answer forums. This allows for capturing information in visual, simple, searchable or bite-sized learning formats. Incentives may include prizes for participants, such as gift cards to local restaurants or retailers, formal recognition for an employee’s expertise, or part of an employee’s development or career advancement plan. Companies can also incentivize participation in mentoring and development programs and training courses. Such efforts help encourage cross-department communication and may afford new or more challenging programs with a rise in participation.
Revamp Performance Management
Many of today’s workers are feedback-driven and expect consistent reviews on their activities at work. In a recent global survey conducted by Oxford Economics in partnership with SAP, 1,400 millennials shared that they want more feedback from their managers.
As organizations adjust to increasingly digitizing their workplace activities, the ability to adapt to change is more important than ever. Companies must not only see their changes through, but be able to course correct and execute those changes across all levels of employees, from the most senior to the most junior. At a foundational level, adjusting and modifying deeply-rooted modes of working becomes key.
If the systems where goals are recorded and accomplished aren't connected, it's hard to spot when employees are struggling with objectives, or for workers to know if company priorities are changing. Strong performance management technology, coupled with collaboration systems, can help save time and increase agility during the review cycle.
Balance Speed with Quality and Efficiency
In today’s competitive business landscape, speed is an important attribute for manufacturers. Organizations with rapid product innovation may be first to market and able to enjoy a higher market share and increased sales. However, hasty or poor decisions upstream in the design process may lead to impacts downstream in the supply chain. For example, selection of the wrong material or lack of validation on the design may lead to disruption in manufacturing or delays to market. This results in significant money lost in opportunity cost and wasted labor and materials. To achieve commercial success, companies must balance quality and efficiency with the desire to be first to market.
With collaborative product design and innovation, manufacturers are better equipped to evaluate areas of improvement in the product life cycle and determine ways to minimize delays to market. This is especially key for areas that are highly synergistic and require significant input and coordination across multiple departments, such as product research and development, quality assurance and regulatory and safety processes. Best practices include:
- Embrace continuous innovation — Adopt continuous innovation to cultivate changes in design thinking and innovation processes, challenge current thinking and generate fresh ideas. With a shared space to capture decisions and priorities, organizations can quickly move from ideas to driving implementation, irrespective of changing project team members.
- Solicit feedback — Seek and incorporate insights from distributors, partners and consumers to ensure feedback that runs the gamut.
- Track product and design changes — Tie internal discussions to the innovation and design process. Manufacturers may integrate collaborative discussions and decisions with product life cycle management applications to easily track changes.
- Leverage analytics — Pull in data on product performance to uncover opportunities, areas of improvement or risk to drive the right discussions and course correction.
Whether your organization’s goal is to reduce training costs, streamline processes, maintain talent, or maintain their competitive edge by driving innovation, social collaboration is an integral part of the manufacturing workplace. With social collaboration platforms that bring together people, data, information and processes, customers, partners and colleagues are able to seamlessly communicate, collaborate and drive real business results. By leveraging these elements for learning and development, manufacturers are set up to help ensure operational viability and business success.
Daisy Hernandez is Global Vice President of Product Management, Enterprise Collaboration Software (SAP Jam).