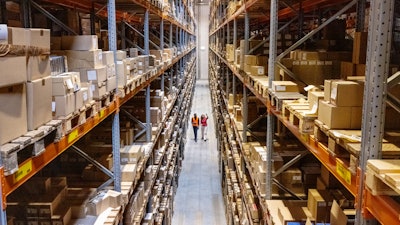
In the quest for supply chain optimization, innovation emerges as a game-changer. It is all about leveraging modern technologies to make the supply chain more efficient, resilient and sustainable. The integration of supply chain services is one such innovation, shifting the perspective from a tactical view to a strategy-led vision of a more interconnected world.
This involves the strategic use of technology to enhance interoperability and streamline operations and by integrating more stakeholders into the planning process to develop holistic and feasible strategies. Adrian Wood Director of Strategic Business Development at DELMIA, takes a closer look at how the supply chain is continuing to optimize through innovation and evolution.
Enabling the resilient supply chain
Supply chain resiliency is not a short-term endeavor. For most, it will be a journey of progressive evolution, capabilities and results. This evolution can be broken down into key milestone stages that help define important steps and how to focus on process and technology changes.
Dassault Systèmes
Early Stage Evolution (Stages 1-2)
Companies here probably still rely on manual processes, spreadsheets or homegrown applications and their focus is usually entirely on internal operations. The opportunities at this stage are to enable new levels of automation and more robust processes.
This will help stakeholders manage the data and workflows needed to stop βreactingβ and start making more proactive and collaborative decisions. There are also opportunities to introduce the first levels of optimization to help develop better forecasting and planning of operational models.
Mid-stage Evolution (Stage 3: The Tipping Point)
The fundamental change in focus at this stage is to stop thinking of the supply chain as an isolated and internal operation. Most supply chains are heavily dependent on additional stakeholders inside the organization.
- Operational divisions support the business model, so additional stakeholders need to be included in the decision-making process. Finance is an especially important role to include in the process as they represent the fundamental business metrics and goals for success.
- Supply chain planning is generally strategic in nature, but tactical execution can influence performance and long-term goals. For manufacturers, production operations can both present opportunities in developing strategic plans and disrupt plans already in place. Including manufacturing execution and scheduling as part of the planning process can help achieve strategic goals. There are many challenges related to collaboration and the management of new types of data and information, but achieving this level of maturity means companies have developed a robust Sales & Operations Planning (S&OP) process and have started to enable the first elements of Integrated Business Planning (IBP)
Late Stage Evolution (Stages 4-5)
Previous stages enabled a maturity level of all internal processes and planning. But since supply chain operations are often outsourced or dependent on third parties, it is important to consider external stakeholders as part of the collaborative process too. In addition, the growing scope and complexity of the planning process requires new levels of automation beyond just facilitating workflow and data management.
- External stakeholders: Whether it is alternative supply sources, contract manufacturers or logistics partners, it is impossible to make confident supply chain decisions without being able to model the details of the extended value network.
- Autonomous supply chains: It is likely that the workforce managing the supply chain process is becoming busier and/or more constrained. With the explosion of the volume of data and variables now being considered, optimization should now be applied to resolve supply and demand changes automatically wherever possible (e.g., within certain thresholds of acceptable outcomes). This way, supply chain professionals can manage βby exceptionβ and spend their time on value-added activities. In addition to including external stakeholders, supply chain organizations need to recognize the critical dependencies of other internal divisions on overall success. Some of the greatest opportunities (or risk mitigation) come from considering manufacturing and product design and engineering as critical stakeholders in the planning process.
iStock
Integrating manufacturing and engineering for supply chain optimization
Integrating manufacturing and engineering into supply chain optimization involves a holistic approach that brings together all aspects of a business's operations. This includes the synchronization of end-to-end operations from planning and scheduling to production and shipping.
Manufacturers must also achieve digital integration of supply chains with their engineering chains to remain competitive. This requires the use of innovative technologies such as intelligent automation, Artificial Intelligence (AI) and cloud-based platforms.
The integration also involves:
- Streamlining information flows
- Aligning physical flows with manufacturing improvement programs
- Fostering close relationships with suppliers to reduce costs
This integration can result in substantial improvements in efficiency, product quality and customer satisfaction. It can also enhance profitability by optimizing the utilization of raw materials and production capacity. Further, integrating supplier practices into the optimization process is also crucial. This can be achieved through Lean Management and Total Quality Management paradigms, which emphasize close relationships with a concentrated base of suppliers.
The combination of these elements leads to a more resilient and efficient supply chain, capable of adapting to changes in demand and supply and capable of delivering superior customer service.
Achieving supply chain sustainability
Sustainability in supply chain management allows you to meet standardized processes without affecting the environment. Achieving more effective planning helps optimize supply chain and logistic flows to reduce emissions, energy consumption and waste across the value network. Matching supply and demand with optimized S&OP also means a more efficient use of resources, raw materials and energy.
However, connecting the supply chain to engineering and production operations also provides unparalleled new opportunities to drive sustainability initiatives:
Achieving supply chain sustainability involves multiple considerations. It requires a holistic approach, considering the entire supply chain from raw materials to customer delivery. The aim is to minimize environmental harm and ensure socially just practices.
- Optimization techniques: These involve lean practices and just-in-time processes that reduce waste and enhance efficiency.
- Collaboration: Engaging with suppliers, customers and even competitors can foster unprecedented types of partnerships that enhance sustainability.
- Technology: Utilizing Industry 4.0 technologies such as AI, IoT and blockchain can significantly improve the supply chain's efficiency and sustainability.
It is also crucial to consider the resilience and agility of the supply chain. A sustainable supply chain is more adaptable and capable of weathering disruptions, which is particularly relevant in the current context of global economic recovery.
Furthermore, the emphasis is not limited to environmental sustainability but also includes the human aspect. This extends to ensuring fair practices across the supply chain and preserving human rights.
Finally, it is worth noting that achieving supply chain sustainability is not only an ethical imperative but also a business necessity. It enables companies to meet increasing customer expectations for sustainable practices, provides a competitive advantage and contributes to long-term business success.
Embracing these innovations can lead to a high-performing supply chain that enables business efficiency and a successful customer experience.
---
Adrian Wood has been the Director of Strategic Business Development for the DELMIA brand at Dassault Systèmes since 2019. He is responsible for developing new and innovative business markets and reinforcing the company position as an innovative leader in key industries.
Adrian WoodDassault Systèmes