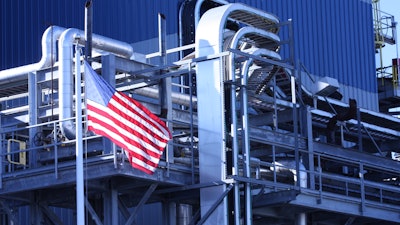
The COVID pandemic has led the U.S. industrial sector to take a hard look at the efficiencies and cost-effectiveness of operations and supply chains. While production improvements can be addressed by implementing process improvements, updating infrastructure, upgrading IT platforms, and making equipment investments, supply chains are obviously more complicated.
Enhancements in this arena need to offer efficiencies that are realized not only on a day-to-day basis, but in realizing business continuity goals related to unplanned events, like a pandemic. With this in mind, we offer the following collection of articles and interviews that look at reshoring as a potential solution. In addition to examining a potential reshoring surge, weβll also investigate the challenges that remain in bringing more jobs back to the U.S.
According to David Commiskey, VP of Customer Solutions at GlobalTranz, while the initial shock of COVID-19 has subsided, many supply chains face a major wake-up call after experiencing exponential sourcing delays. And in doing so, a number of shippers are considering nearshoring supply chains.
For a variety of reasons, shippers with a manufacturing base in China are increasingly considering nearshoring options. Prior to the COVID-19 pandemic, some manufacturers moved or considered moving operations to other countries in the region, including Vietnam and Taiwan, due to tariff threats. In the wake of COVID-19, an increasing number of businesses, particularly pharmaceutical manufacturers, are looking to nearshore their operations to gain greater self-sufficiency, visibility, and control over their supply chains.
We are seeing an increasing number of our customers considering Mexico for their manufacturing. Overall, shippers are taking their contingency plans more seriously than ever before, and looking to strengthen their supply chain resiliency, particularly with regards to essential parts and components.
The E-Commerce Effect
As consumer behavior evolves and e-commerce continues to grow, retailers are rethinking how they utilize their brick and mortar footprints, with many repurposing stockrooms to serve as mini-fulfillment centers. This allows retailers to get continuously closer to their consumers to facilitate the same day/next day delivery they have come to expect. With a growing emphasis on e-commerce and delivery to the consumerβs home, many shippers are seeking 3PLs that can provide dedicated Final Mile solutions.
Our experience is that shippers are not leaning away from globalization, but they are re-evaluating their strategy and taking a more holistic approach. The traditional approach to globalization was primarily driven by cost-savings. However, as tariffs and COVID-19 have demonstrated, there are other important factors for shippers to consider when it comes to their supply chain. Risk mitigation has grown in importance, leading shippers to diversify their supplier base to ensure they have contingency sources for key products, parts, and components.
We have seen shippers making plans and conducting business case analyses, both pre-USMCA and currently, with regards to nearshoring in Mexico. However, the COVID-19 pandemic has slowed some of these plans as economic slowdowns have created uncertainty with regards to customer demand in the near- to mid-term future. Nearshoring can carry significant upfront costs, and some businesses are wary of making those investments in the current economic and political climate.