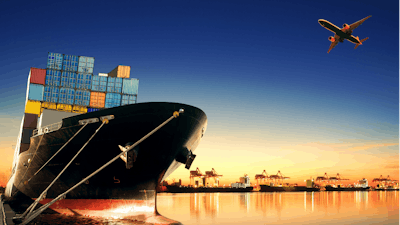
The COVID pandemic has led the U.S. industrial sector to take a hard look at the efficiencies and cost-effectiveness of operations and supply chains. While production improvements can be addressed by implementing process improvements, updating infrastructure, upgrading IT platforms, and making equipment investments, supply chains are obviously more complicated.
Enhancements in this arena need to offer efficiencies that are realized not only on a day-to-day basis, but in realizing business continuity goals related to unplanned events, like a pandemic. With this in mind, we offer the following collection of articles and interviews that look at reshoring as a potential solution. In addition to examining a potential reshoring surge, weβll also investigate the challenges that remain in bringing more jobs back to the U.S.
Melvin Bosso is a principal with Myrtle Consulting Group, a firm that βdrives operational transformation within global manufacturing, processing and distribution organizations.β He recently sat down to discuss what he feels manufacturers have to understand, acknowledge and embrace when considering reshoring and other supply chain strategies.
Jeff Reinke, editorial director: We know about some of the main re-shoring advantages, but are there others that are being realized but not as highly touted?
Melvin Bosso, Myrtle Consulting: The COVID-19 pandemic appears to be one of these major earthquakes that forces everyone to reshape, rethink and redefine their understanding and perception of world trends. As a consequence, many known concepts gain a new life: risk, resilience, crisis, working from home, βstaycationβ are just a few examples.
Reshoring is also an example of a dynamic that had started long before COVID-19 and will continue far beyond the emotional reaction to the catastrophic effects of the crisis.
Reshoring actually started to impose itself to some as early as in the late nineties, depending on where in the world companies were active. It is indeed driven by an improved understanding of the balance of costs between manufacturing and distribution but, as your question notes it also refers to supply chain flexibility and market accessibility.
The past 20 years have seen the world accelerate its globalization and relocalization journeys. As business leaders have gained a deeper understanding of their respective company dynamics, they work to find the balance for their supply chains. We see four major clusters of reasons why a company makes a decision on how to deploy their supply chains: Costs, Service, Technology and Risk.
While the first three clusters are widely understood and are perceived to be very accessible to all, most organizations have had to rethink their understanding of the fourth cluster - Risk. The fact that the North American supply chain community is generally thinking about an evolution of the strategic focus of supply chain from just-in-time to just-in-case is an example of how the notion of Risk has been redefined by COVID-19.
JR: Is there a way for states to try to compete for the jobs that are coming back to the states, or are companies pre-determining the sites of the re-shored jobs?
MB: States and companies will have to work together to determine the right direction for all stakeholders. As stated earlier βCosts, Service, Technology and Riskβ are the four main drivers for reshoring decisions.
With COVID-19, states that are looking to build lasting partnerships have the opportunity to engage and target companies on any one or any combination of reshoring initiatives. The feeling is that most of these reshored jobs are either going to union-friendly locations, or those closer to ports. Is that true? If so, what can states (like my home state of Wisconsin) do to overcome some of these "deficiencies"?
Like most broad statements in business, this feeling is neither completely true nor completely false. The nature of potential jobs being directly or indirectly created by reshoring would be established as part of an effort to improve overall supply chain performance. Reshoring should not be understood as a linear process, equally applicable to all companies and at all times.
In our experience, it is a company-specific process, with high stakes that should be inextricably glued to the company strategy. As a result, external stakeholders that have interest in a reshoring dynamic should invest in understanding business strategies and find ways to add value in the deployment of said strategy.
JR: Which industries are seeing the biggest uptick in re-shored jobs?
MB: In 2016, different sources estimated between 0.5 to 3 million jobs created by reshoring. With very little deep and independently corroborated studies to confirm these numbers, or other studies since 2016, it would be imprudent to confirm any trends in job creations. Some companies in manufacturing have publicly announced reshoring activities, and we know that some companies are actively thinking of reshoring as part of their strategy.
JR: Are there specific supply chains that are triggering companyβs decisions to reshore?
MB: With COVID-19, the world has experienced the effects of a supply chain without supply when China, and more broadly Asia, locked down. All supply chains that run with a just-in-time inventory strategy had to deal with a shortage risk. All essential industries are coming out of the crisis thinking about alternatives. Many are working, or will be working, to find ways to change their exposure.
The pharmaceutical and healthcare industries appear to be the ones that are showing the greatest interest in gaining a greater hold of their supply chains.
Food and beverage industries are also very central in supply chain leadersβ minds. Here, again, reshoring or onshoring has enormous complication levels that will have to be part of the equation. The ongoing 5G face-off of world powers and the global structure of the high tech industry also suggest a strategic need to rethink the location of technology manufacturing and service assets around the world.
JR: COVID is definitely having an impact on reshoring trends β do you think these moves will be short or long-term?
MB: On thing is for sure - 2021 is not going to look or feel like 2019. Supply chain strategies are likely to be more in tune with their risk exposure than in prior years.
That being said, reshoring started long before COVID-19 and it will continue long after. Companies will continue to optimize their network using as much information as possible. We expect that once the COVID-19 dust settles, we will go back to a world with a higher tolerance for risk and where reshoring and offshoring will continue based on cost, service and technology β¦ for most. Great companies will make a conscious effort to try to keep risk as a priority.