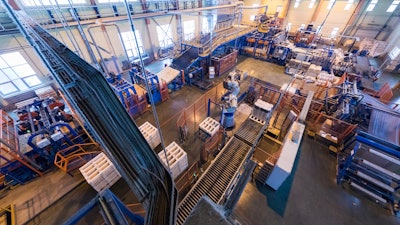
Manufacturing leaders today face pressure to maximize productivity, reduce costs and maintain exceptional quality — all simultaneously. Many companies have transformed their industrial engineering and supply chain management, yet the shop floor remains overlooked.
Manufacturing Operations Management (MOM) fills the gap by offering a comprehensive approach that expands upon traditional Manufacturing Execution Systems (MES). MOM brings the benefits of full digitalization, including real-time visibility and the use of virtual twin technology to capture implicit knowledge and best practices.
MOM software directly addresses shop floor challenges by applying technology to evolve management systems beyond previous limitations. Unlike legacy systems that merely tracked production, today's MOM platforms unite quality, maintenance, inventory and workforce management under one digital system.
This integration eliminates silos, creating a seamless information flow that gives manufacturers complete operational visibility and control.
The integration of several functions into one workflow is especially valuable for manufacturers that must navigate tight profit margins and address workforce shortages. MOM offers an adaptability edge, helping the company drive innovation to meet those simultaneous demands for productivity, cost reduction and quality.
Real-time visibility for proactive management
Perhaps MOM's most transformative feature is real-time operational visibility. Traditional manufacturing decision-makers often rely on data that is hours or days old, creating persistent gaps between the shop floor reality and management actions.
MOM solutions eliminate this gap, providing instant insights into production status, equipment health, quality metrics, material supply position and workforce productivity. Shop floor managers and operators have real-time machine performance data, inventory levels and production updates at their fingertips. Integrated IoT sensors paired with advanced analytics generate predictive alerts, allowing teams to proactively avoid disruptions.
For example, global cosmetics and personal care products maker L'Oréal added MOM technology to its worldwide manufacturing operations. They chose DELMIA Apriso from Dassault Systèmes for installation across more than 30 plants. The company reports the following benefits:
- Better consistency in the execution of production, quality and inventory management
- Implementation of a full global traceability program across the organization
- Increased "first time right" production, which directly impacts OEE by reducing defects and rework
Additionally, L'Oréal took advantage of DELMIA Apriso to identify patterns and anomalies, for truly predictive management.
The OEE edge
OEE is short for Overall Equipment Effectiveness, a manufacturing metric used to identify truly productive production time, as a percentage of total production time. It is calculated on three factors: availability, performance and quality:
- Availability measures the proportion of time equipment is operational compared to planned production time
- Performance evaluates whether the equipment operates at its maximum speed
- Quality assesses the percentage of good parts produced versus defective ones
An OEE score of 100% indicates perfect production with no downtime, optimal speed and zero defects. It serves as a benchmark for efficiency and helps manufacturers identify areas for improvement to optimize operations.
While L'Oréal has not disclosed specific OEE metrics, a published case study indicates the company achieved better visibility and control over worldwide operations, which are crucial components of OEE improvement. L'Oréal's stated goal was to build an Industry 4.0 solution that integrates operations across all factories worldwide through paperless manufacturing and digitalization of all shop floors.
Scheduling and resource utilization
Resource utilization, both human and machine, has always been a challenge in manufacturing. Traditional fixed scheduling methods don't easily adapt to rapidly shifting demands or constraints. The result often leads to inefficiencies that reduce profitability.
Advanced MOM systems integrate with enterprise software, adjusting production schedules dynamically in real-time based on production changes, supply chain issues, resource availability and operational conditions. By automating complex operational processes, MOM solutions minimize operational bottlenecks and reduce costly delays.
These solutions account for equipment availability, operator skills, material constraints and order priorities simultaneously, maximizing throughput and minimizing waste.
Manufacturers implementing MOM have reported marked improvements in production efficiency and throughput, shorter lead times and substantial cost reductions. Configurable operational best practice capabilities also ensure consistency and efficiency across multiple manufacturing sites globally.
CoorsTek Transformation
CoorsTek is a 110-year-old technical ceramics manufacturer with operations spanning 27 global facilities. Facing complex production processes and demanding customer requirements, the company implemented the DELMIA Apriso Manufacturing Operations Management Suite to enhance manufacturing efficiency, quality control and maintenance operations.
“When you make precision ceramics, you form the ceramic in a specific way, then fire it through a kiln and finish it through grinding or CNC operations. It is incredibly asset intensive,” explained Brian Frimel, CoorsTek's Senior Director of IT.
With over 10,000 pieces of equipment in their global operation, equipment uptime is critical to on-time delivery.
The Apriso implementation has transformed CoorsTek's shop floor visibility and quality management. The company now executes inline inspection processes to identify quality issues before products are shipped.
As Matt Mehlbrech, VP of Information Technology, noted, “We have minimized quality escapes and we’ve seen direct reductions in our scrap.”
Real-time monitoring has enabled proactive maintenance planning, dramatically reducing unplanned downtime across facilities. By standardizing scrap codes within the system, the company can better analyze and improve specific areas where defects occur.
For shop floor operators, the MOM implementation has streamlined daily workflows by providing centralized access to work orders, machine allocations, quality requirements and digital work instructions. Paper-based processes have been eliminated.
“We’ve removed stacks of binders from the shop floor,” said Bob Sendek, Director of ERP Program Management. “We no longer need to worry if we are working on the latest revision, as that’s what is always presented to the user. Shop-floor users can record quality information at the point of use, including critical parameters, which we can run different checks against to ensure a product is within its process capability.”
The results speak to the transformative power of comprehensive MOM solutions. CoorsTek has improved predictability in production output, enhanced quality consistency and created a more responsive manufacturing environment that can adapt quickly to customer demands. The company’s successful digital transformation earned them a CIO 100 Award for their orchestration of different systems to modernize their shop floor operations.
Mehlbrech added, “We want to use the platform to simulate, predict and prescribe what we need to do on the shop floor and allow us to be more nimble than we've ever been before.”
Strategic differentiation
As manufacturing continues to evolve in complexity and competitiveness, MOM solutions have become essential rather than optional. Companies that embrace these technologies gain not only operational advantages but strategic differentiation in their markets. Whether improving OEE metrics, reducing cycle times, optimizing material synchronization or enhancing quality control, MOM delivers measurable impact across the manufacturing enterprise.
The transition from traditional production monitoring to comprehensive operational management represents more than a technology upgrade — it's a fundamental shift in modern manufacturing excellence.