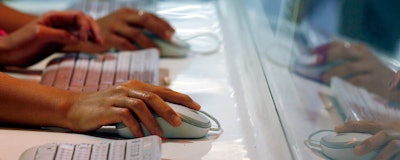

Integrating Enterprise Resource Planning (ERP) systems and Manufacturing Execution Systems (MES) enables organizations to achieve the goal of super lean manufacturing. This is because these two systems complement and enable each other.
According to Gartner: “By 2020, at least 35 percent of new product-centric ERP deployments in large enterprises will be software as a service (SaaS) loosely integrated with on-premises manufacturing execution systems (MES).” This emphasizes the importance of shifting these two disparate systems from a mere coexisting mode to an integration mode.
ERP and shop floor systems operate on different interpretations of "real time” — ERP focuses on strategic management of the business, while MES is associated with the punctual execution of the process. When managers can visualize, monitor and document manufacturing processes on the shop floor, they can detect process deviations and trends to improve production while also reducing overages and optimizing delivery schedules. When the systems work in unison, and not just in parallel, they allow the manufacturing industry to adapt to the dynamic demands coming from customers, regulators and suppliers.
As one unified system, there are multiple possibilities for improved flexibility and efficiency. Here are a few key examples.
Better Demand Forecasting
Using fully integrated systems, demand changes that are recorded in ERP systems can be fed into manufacturing schedules to ensure that quantities of products manufactured are more closely aligned with demand. This is essential because of all the costs associated with having too much or too little inventory.
Having shortages or stock outs is detrimental to both short and long term revenues since delays in delivery schedules can tarnish a company’s perceived reliability and long term customer relationships. The only alternative after running out of inventory is to place rush orders. Ordering materials at the last minute is one of the main supply chain risks because of their negative impact on the overall performance and the additional charges incurred by requesting expedited deliveries.
By integrating ERP and manufacturing data for more accurate demand forecasts, companies can avoid over-estimating demand, which results in excessive inventory. When companies invest upfront in a lot of extra inventory that can’t be quickly turned into profit, their cash is tied up and can’t be put to better use elsewhere.
Real-Time Adjustments
Better system integration supports more efficient execution of change orders. New manufacturing processes that impact production times and expenses can be shared immediately with enterprise systems so that any pricing or product delivery information can be updated. Likewise, any product changes requested by customers can be transferred to production systems as soon as possible to avoid delays in fulfilling orders.
If there is a quality issue on the floor, real-time notification to the business systems can be made to take the necessary corrective action as soon as possible. When defective material is detected, it can be quickly removed from the inventory and returned to the supplier for a replacement or refund. The manufacturer saves money by eliminating scrap due to defective raw material and also reduces exposure to recalls and possible liability issues.
Just-in-Time Delivery
Satisfying customers by delivering demands at an agreed time, leads to customers’ trust in a company’s competence.
Just-in-time (JIT) delivery, and the surgical precision it requires, has been around for quite some time. But now that supply chains are becoming increasingly intertwined with smart sensors introduced with the Internet of Things (IoT), supply chain managers can track inbound and outbound inventory with incredible detail, and this visibility allows brands to react immediately to changes. ERP schedules can be more realistic by incorporating quicker production times based on the latest improvements on the shop floor. When necessary, downtime as a result of damaged or defective equipment can be reported to the ERP system to push back delivery dates. Even in transit, sensors on containers or trucks deliver real-time insights to products across the supply chain.
Frequently, manufacturers’ MES and ERP systems are developed by different software vendors and speak different languages, which means that integrating the systems can be a challenge. With the growth in the amount of data used to improve the production processes, the cross communication and interaction between components has increased. To reduce the cost of communication and to increase the efficiency of these systems, middleware can be an option to ensure a free flow of information to achieve leaner, more efficient and effective manufacturing.
Real-time information exchange between the business layer and the production layer can increase overall equipment efficiency (OEE), reduce cycle times, and provide management with greater visibility for improved decision making. The accuracy of information and speed with which it can be delivered due to ERP and MES integrations allows for more nimble and lean manufacturing, the goal of every organization that wants to keep a competitive edge.
Javier Jiménez is President of Magic Software Enterprises Americas.