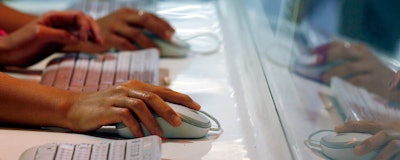
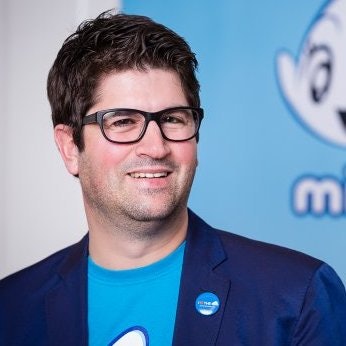
Considering the massive global ecosystems of manufacturers and customers that supply chains comprise (in 2014 Gartner estimated that the supply chain management and software market alone represented $9.9 billion), one critical piece that’s often treated as an afterthought is the service and maintenance of all of the technology within those supply chains. The importance of this servicing element can’t be understated: according to recent research, on average, manufacturing businesses lose $1.6 million for every hour of IT system downtime. Crunching those numbers further, that amounts to almost $40 million a day, or a staggering $14 billion a year — and that’s just for one organization!
As a result, it’s clear that supply chain-dependent organizations would be wise to apply as many safeguards as possible to avoid the crippling business effects of IT system downtime. One of these safeguards is the use of software specifically designed to help organizations manage their field service operations — a category known as field service management (FSM) software, which, according to a recent report from MarketsandMarkets, is a market that will be worth more than $5 billion by 2020. Just as a service provider such as Comcast has technicians out in the field to help fix internet or cable outages for consumers like you and me, supply chain organizations should have field service technicians available at the drop of a hat to do the same for their customers (as well as for their own organization’s operations).
In practice, an organization with far-reaching supply chain operations (such as a manufacturer) can use FSM software to track their field service teams to ensure that all the technology elements of its supply chain — from the factory to the end-user and all points in between — are up and running. After all, a chain is only as strong as its weakest link. And this is especially useful today with the pervasiveness of the Internet of Things (IoT), as automated machinery that’s connected to the IoT can now, through FSM software, tell field service technicians in real-time when and where maintenance is needed — thereby avoiding the dreaded money pit that IT system downtime represents. Furthermore, the benefits of FSM software don’t just stop at cost savings, but extend to a more efficient use of an organization’s personnel/resources, an opportunity to differentiate organizations against their competition, and a platform for delivering enhanced customer service.
However, the IoT is a double-edged sword for supply chain-dependent organizations, and it’s mainly because of this last point above: customer service. The issue is that the real-time visibility and insight provided to manufacturers by IoT-connected devices and machinery has also conditioned customers to not only expect, but demand, real-time customer service. And the problem here is that the amount of IoT devices and machinery is growing at an exponential scale, while the number of technicians available to service and maintain that technology is growing at a much slower rate — if at all. So it’s easy to see why this imbalanced equation is causing a customer service headache for supply chain organizations.
But what if the FSM industry adopted a new business model — one that could shift the balance of technology versus technicians back to a sustainable equilibrium for supply chain-dependent organizations? This would be the tipping point that could help manufacturing organizations leverage FSM to realize the true promise of the IoT. And the FSM industry need look no further than some of the forward-thinking companies that lead the way in the sharing economy, such as Uber and Airbnb. By introducing technology that enables the crowdsourcing of field service to independent, for-hire field service technicians (just like Uber does for drivers), FSM software providers would be able to help manufacturing organizations find those technicians anywhere and anytime — which would check that critical box of providing real-time customer service. And by utilizing crowdsourced field service (or “crowd service”) for IoT-connected supply chain machinery, manufacturers will not only be able to deliver real-time customer support, but could also provide service and maintenance before those technologies suffer an outage simply by checking their operational status from home base. Think about that: through crowd service, supply chain-dependent organizations can proactively ensure that they never face that dreaded IT system downtime that essentially delivers a $1.6 million bill every hour.
This crowd service concept has the potential to be highly disruptive in the FSM industry (to say the least), but unlike many other technology-based developments that are termed as disruptive, crowd service isn’t simply a pipe dream. FSM software providers are not only laying the groundwork for crowd service as we speak, but are actually deploying the technology in the field (excuse the pun) — and many in the FSM industry expect crowd service to completely revolutionize the way that supply chain-dependent organizations service their customers in 2017 and beyond. So if you’re seeking a way for your organization to provide the customer service that the IoT demands — while helping ensure that you don’t foot the terrifying $1.6 million/hour bill from IT systems downtime — you might want to add “look into FSM and crowd service” to your list of New Year’s resolutions.
Manuel Grenacher is CEO of Coresystems.