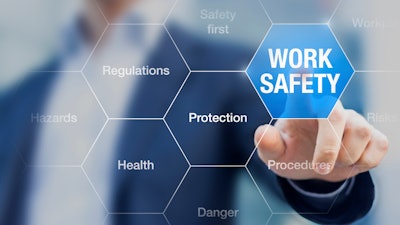
Employee safety in the manufacturing industry should be the most critical part of the job. Yet, with other challenges, including the ongoing manufacturing labor shortage, safety often gets put on the back burner.
What’s at risk when safety isn’t prioritized, or manufacturers lack digital automation tools?
- Company fatigue limits could be exceeded because you lack real-time visibility into hours worked.
- Your plant could lack the required safety personnel to get the day’s work done.
- Workers could end up performing work that wasn’t planned or scheduled, leading to unapproved overtime.
- Missing badge events could mean you don’t know where people are in a safety event.
The right digital tools can reduce safety incidents while enabling continuous on- and off-site improvements. By leveraging digital technology, manufacturers can better mitigate risk while improving safety for all parties and improving relationships. Let’s face it, when people get hurt – or worse – on the job, all stakeholders suffer: manufacturers, employees, contractors, their families, and customers. Business reputation can also take a nosedive and when that goes down, lost revenue often follows.
Here are some specific ways technology can help proactively reduce potential safety breaches.
Unplanned or Unscheduled Work Risks
Failing to plan is planning to fail. Poor planning and scheduling can lead to unsafe practices. When a site is in constant reaction mode because management failed to schedule a safety monitor or trained welder, for example, risk increases and can even become embedded into company culture.
Some jobs are more dangerous than others. But with the right automation tools, operators can improve safety when they:
- Know the location of all personnel to reduce muster time and ensure OSHA compliance in an emergency.
- Eliminate safety blind spots and decrease time to safety by tracking equipment usage.
- Get alerts for reaching fatigue limit status.
It’s not enough to rely on headcount and manpower reports when digital automation tools prevail. Software helps planners see daily onsite workforce by vendor, skill, and count and matches that information with the plan. Should a safety incident occur, this information becomes invaluable by enabling them to know who is onsite and when.
The Costs of Fatigue Management
Fatigue and overtime go hand in hand. When fatigue policies are broken, or come close to being breached, overtime racks up. Plus, accidents and injuries are just waiting to happen—not to mention expenses increase. According to OSHA, working 12 hours per day comes with a 37 percent increased risk of injury. Further, fatigue-related, health-related lost productivity time at work costs employers an estimated annual $136.4 billion.
Technology can help to accurately monitor workers (and assets) and provide fatigue violation alerts and data in real time. For instance, data can show if a contract warehouse associate has been on the job for 14 consecutive hours in a day or for 14 consecutive days in a row.
Using real-time access gate data, onsite hours are tracked and flagged so lives and companies are safer. This allows manufacturers to proactively mitigate risk by reducing dangerous overtime shifts or by sending someone home before an accident occurs.
Avoid Exceptions
You don’t know what you don’t know, like who is working outside your controls. Constant overtime and missing badge events have the potential to become prime candidates for unsafe situations.
When workers fail to badge into a facility or if someone simply lets them in through a different gate or side door, management is unaware of who is onsite. This is not an ideal situation because it poses risk. Technology can send alerts when instances like this are occurring so they can be stopped in their tracks and eliminated in the future.
A shortage of skilled workers can lead to an understaffed and overworked plant, posing an additional safety risk for the industry. While incentives like the CHIPS Act and Inflation Reduction Act have boosted manufacturing projects, the shortage of skilled workers is delaying work.
Vocational and STEM-focused educational programs can improve future numbers of skilled workers. Meanwhile, efficient technology that supports on-the-job safety and training is a competitive advantage. Reduction of manual error, efficiency, time savings, and safe workplaces all appeal to potential employees looking to succeed in their roles.
Technology that tracks skill levels, offers fatigue dashboards, and tracks employee location can stop safety problems before they happen. For example, in a plant covering 700+ acres, manually tracking employee location is virtually impossible. Digitally tracking scan-ins at each rally point allows managers to take quick action in a safety event to ensure everyone is accounted for and away from the dangerous event.
When safety becomes de-emphasized in favor of getting the job done quickly and more profitably, worker well-being goes down and employer liability goes up. Potential employees will trust companies who value safety and have the technology to reflect it.
At the end of the day, the right digital technology helps to improve collaboration at your plant. Every employee wants a safe workplace, and technology brings real-life visibility into data management, which can be leveraged to decrease risk and maintain a healthier environment.
After all, facilities that are efficient and running correctly are more likely to get products out the door and jobs done without sacrificing safety.