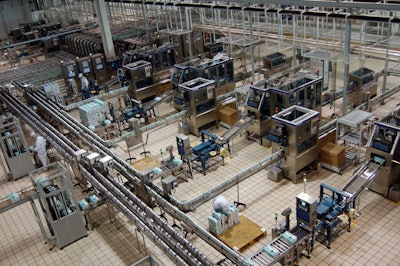
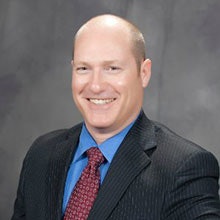
Automatic adjustments to improve uptime. Laser arrays to scan for operators. Servo technology to changeover equipment on the fly.
New technologies are removing physical interaction from the automation equation. It’s the next generation of machine safety solutions.
But not so fast. Machines do not yet independently strive for safety. Food and beverage packaging is all about folding, cutting, pressing and moving in a fast-paced environment. Conveyors alone are involved in 30 percent of all machinery accidents.[1] There’s no doubt that equipment in these facilities is extremely dangerous — and one of the highest risk zones in a plant. If a machine is big enough to form a carton, chances are it can take a finger with it. In a perfect world, all food and beverage plants would be equipped with smart machines and adequate guarding. But in reality, companies are still working to build and maintain safer facilities. Operators still engage with machines manually, and work with semiautomatic equipment.
Identifying Areas of Improvement
General safety solutions might not work with the specific and individual setup of your plant. Instead, each production area needs a risk assessment, confirmation that safety standards are being met and solutions that are tailored to the equipment and the process. This doesn’t have to take an eternity or cost a fortune — software is available to walk you through an automated risk assessment.
PMMI, the Association for Packaging and Processing Technologies, also works to develop risk assessments and safety standards for North America. Their work describes the hazards and the solutions required to make a plant safe.
First, don’t let the following concerns hinder implementation:
Loss of Machine Access
One concern is that machine safety can reduce efficiency as operators have restricted access to machines. This doesn’t have to be the case. For instance, guard locks can be adjusted for points of access, allowing an operator to alert a machine to the need for access. This gives the machine the opportunity to get into a safe mode so the operator can walk into the machine and make necessary adjustments, safely without impacting productivity.
Employees Overriding Safety
If a safety solution hinders an operator from being productive, they’re likely to find a way to override it. While improved safety might not provide unbridled freedom to interact with a machine, it should help maintain safety and also give employees the appropriate, responsive access required to efficiently perform their jobs.
Cost
A major concern is that food safety solutions for the packaging line can’t offer the return on investment needed to justify a project. Improved safety can result in fewer accidents and offers gains in energy usage and productivity. As one example, a safety system that has maintained records of equipment interaction can help error-proof a system and diagnose future safety issues.
Safety does not stand in the way of profit or productivity in the packaging line. It can and should improve the efficiency of a plant. Some new equipment and technology that are getting us there include:
Toolless Changeover: Any changeover that requires someone to grab a wrench, pliers or screwdriver can invite potential ergonomic ailments for the operator. With toolless changeover, the equipment slides apart, decreasing interaction with pinch points and sheer points common to the packaging area. Additionally, toolless changeover ensures error-proofing and improves uptime.
Sensor Technology: The safest and most productive facilities use laser technology that scans for any humans in high-risk zones. Traditionally, an operator would need to shut power off completely to accomplish a task safely. With sensor technology, the appropriate machines can slow down or cease their processes. Operator safety is improved, and you gain higher productivity and energy efficiency, but remove the need for a shutdown and restart.
Humans and robots working collaboratively and safely is the future. But it only works when the sensor technology, control systems, motor, drives and other components are more integrated.
To find out more valuable information on modern safety initiatives affecting the food and beverage industry, check out the food and beverage industry safety guide here.
[1] Source: Packaging machinery — in all manufacturing industries. Health and Safety Executive