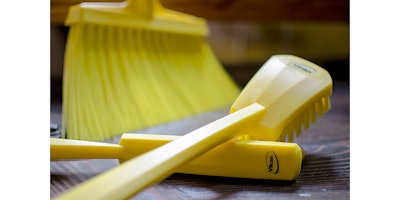
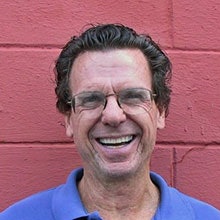
In an effort to improve the safety of a food manufacturing facility, and of the products produced, more and more food manufacturers and processors are implementing color-coding plans. A color-coding plan offers a facility-wide system to keep workspaces organized by outlining specifications such as where and when certain tool use is appropriate by assigning colors to either tool type or zone within a facility. Benefits to utilizing this kind of plan include meeting safety regulations, boosting quality assurance, reducing miscommunication throughout a facility and reducing spend on tool replacement and product waste.
This practice, while growing — particularly in the industry of food and medicinal manufacturing — is still fairly new. With little literature detailing best practices and the fact that color coding plans are unique to each facility, outlining one from scratch can be a daunting task. Noting ways to avoid some of the biggest mistakes made by manufacturers can help alleviate some of that stress.
Not enough people are involved in the planning process. We cannot stress how important this first item is. All too often, the planning and purchasing decisions are being left to one party — in many instances an operations manager or purchasing team member. We recommend involving management team members and purchasing agents, as well as line workers, in this decision process from the very beginning. It is vital to consider the opinion of the people who will be enforcing the plan, budgeting for the plan and, of course, the people that will be affected by the sensibility of the plan on a daily basis in the facility. Each viewpoint will be vastly different and therefore must be taken into consideration.
Decisions are made hastily. A color-coding plan is generally not something at the top of a facilities’ priority list, although it should be. Plants are often looking to find something to suffice regulations or industry standards that meet the basic requirements for color-coding so they can get back to doing other things. Oftentimes, the facilities that fall into this pattern of hastily purchasing color-coding tools have to re-evaluate these decisions in the long run because they did not take the time to consider what will best fit the unique needs of their plant. We recommend taking the time to discuss these facility-specific requirements with the producer or distributor of the products to ensure the right decisions are made the first time.
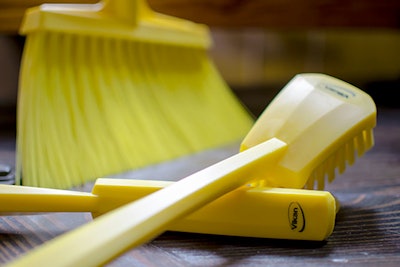
Purchasers are opting for all of the cheapest options. Certainly, we understand that purchasers are looking to meet budget restrictions and keep their bottom line looking good. Sometimes the cheapest option will work for your needs, but that is not always the case. Just as with any purchase, sometimes the job will require something that is more durable, long-lasting or created to specify a certain need. Oftentimes, those cases correlate to a bit of an increase in cost. That being said, selecting the correct tools from the beginning can be cost-saving in the long run if you are not having to replace these products as often. Your distributor should be able to help you discuss what tools are right for your needs and your budget.
Everyone is too focused on the big picture. Sticking to the first tip in this list helps to prevent tunnel vision from happening in the planning phase. Certainly, it’s important to keep the big picture in the back of your mind when drafting a color-coding plan. But oftentimes people stop here and forget to consider the practicality of the tools themselves: Will this tool fit this specific purpose? Is this tool durable enough for this purpose? How many do we realistically need? Where will we store the tool when it is not being used? All of these are examples of the small picture details that need to be considered in the initial planning phases of developing a color-coding scheme.
A company-wide training isn’t scheduled. Even if your color-coding plan is the best possible plan for your facility, it will fail if those who are expected to follow it are not made aware of the plan’s expectations. It is important for facility workers at all levels to receive instruction on the plan and how it is to be properly carried out. Additionally, it is recommended that this procedure allows ample time for discussion and questions. A color-coding plan is only successful if all those who are presumed to use it know how to adequately do so.
About the author
Bob Serfas is the founder and executive of R.S. Quality Products. The company specializes in sanitary, color-coded cleaning tools, manufacturing stainless steel, aluminum and fiberglass handles in ten colors. R.S. Quality Products also serves as a distributor for several manufacturers of premium color-coded tools. The company’s customers are mostly food processors and pharmaceutical firms, and it works with these businesses to set up color-coding programs.